The Role of Simulation in Sustainability: Exploring the Five Core Areas
It’s clear that the sustainability agenda is a priority for organizations these days. How can businesses utilize simulation technology to boost sustainability practices?
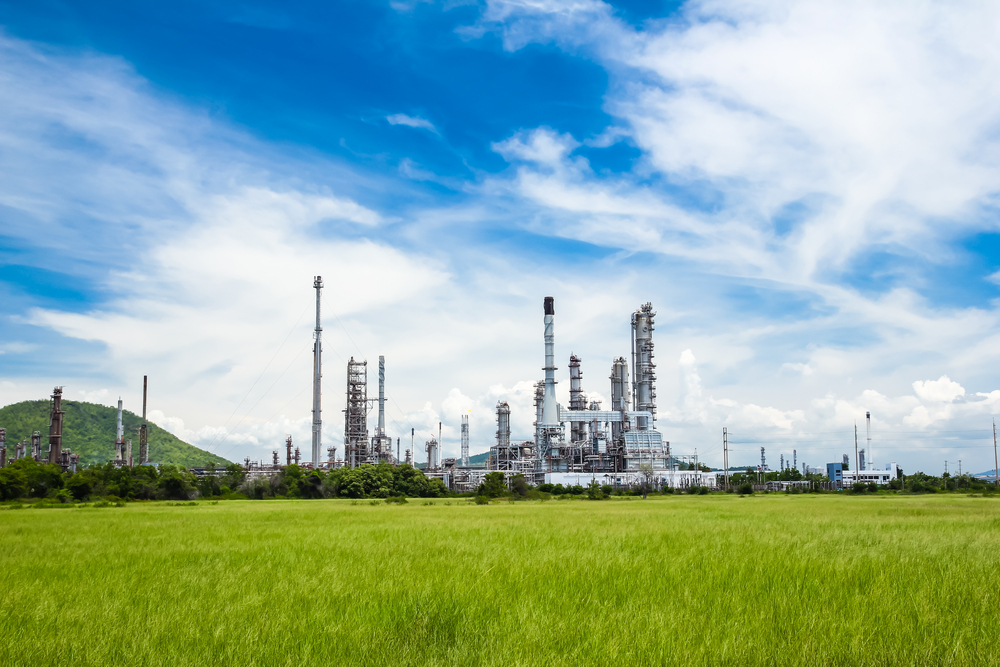
Manufacturing companies are striving to reduce any negative impact they may be having on the environment. A clear focus in recent years has been the adoption of renewable sources of energy such as electricity and hydrogen to power operations.
Back in 2011, Toyota installed the UK’s largest Solar PV array connected to an industrial site, with the aim of generating 4,300,000kWh of energy each year.
In American Samoa, there are comparable achievements. By using Tesla-created solar panels, this island is saving over 110,000 gallons of diesel fuel annually.
An increasing number of manufacturers are also exploring ways of developing existing brownfield land as opposed to building on greenfield sites.
The UK has reduced greenhouse gas emissions by 38% between 1990 and 2015, with 20% of electricity now derived from renewable energy, overtaking coal for the first time. Zero waste and circular economy policies have also made a significant impact in recent years as organizations look to help the UK government’s plan to slash emissions by 79% by 2035.
A similar emissions goal exists in the American White House, too. Their official briefing in early 2021 specifically listed a number of industries and detailed a country-wide effort to lower emissions.
It’s clear that the sustainability agenda is a priority for organizations these days. It is also important to make sure companies use the right tools to ensure beneficial change.
However, most of the efforts in the sustainability space within manufacturing have so far revolved around multinational companies, as they arguably have the biggest role to play as one of the most significant contributors to carbon emissions. Small and medium-sized enterprises (SMEs) on the other hand, although smaller in size, collectively contribute to the sustainability agenda and need to find ways to reduce their carbon footprint, locally and individually.
Simulation software can help play a pivotal role in sustainability for both multinationals and SMEs, but many in the manufacturing industry may not be aware of the different areas in which it can make a difference. There are five key points for using simulations in regards to sustainability for manufacturers: Efficiency, waste, design, packaging, and supply chain resilience. Before discussing these points further, we should elaborate on different ways to use simulation technology.
Ways to use simulation technology
For manufacturers, simulation technology largely revolves around making computer-generated models. It could be as simple as making a model for a new production part, or something as complex as a full-scale model of a full processing plant.
Designers are able to use simulated environments to model, manipulate, and test parts/assemblies before spending time and money on fabrication.
For example, a company can create a 3D model of a robotic arm. On their screen, they can then simulate motion on it and check for interferences, tolerances discrepancies, and design viability.
1. Efficiency
One key aspect of ensuring sustainable practices is more efficient and smarter production methods. Simulation software can help organizations achieve substantial efficiency gains in their production processes and outputs by allowing testing smaller changes on the shop floor from an early stage. The by-product of ensuring efficient practices is ultimately more sustainable strategies.
The key to efficiency is optimization. This can refer to space, process flow, or how you use a product in the first place.
With simulation, a designer can answer every question they may have, before implementing anything. They can lay out their factory and check on every step of the process. Something as simple as moving a piece of equipment to a different area might boost the efficiency of the whole plant by a notable amount.
Of course, physically moving equipment is no small task. With simulations, it’s incredibly easy. It could be as simple as the drag of a mouse and a few clicks in order to test different configurations.
This is one of the biggest uses for simulations in sustainability, as far as manufacturers are concerned. They can adjust their floorplan countless times, analyze the resulting efficiency, and make a decision from there.
2. Waste
The second core strength of simulation software is its ability to reduce waste via lean manufacturing methods. This applies to the production process by designing process flows that encourage the re-use of (raw) materials, but also covers productivity losses, work ergonomics, excessive transport paths of AGVs, forklifts, humans, and other aspects. In reducing functional floor space, lean manufacturing helps reduce carbon footprint. For example, some UK universities can now recycle damaged or faulty goods, and to reuse them in the production line.
Waste can also refer to the time spent doing non-production tasks. If a worker has to go to a different area to complete their daily tasks, then you can see the physical result of wasted time. Plants might decide to make “zones” in which tasks can be completed without having to move somewhere else or transport materials.
With a simulation, these zones can be created and brainstormed easily. The simulated environment can have a process’ equipment, personnel, raw material, and vehicles used to transport the material. The designer can then look at each piece and determine if there’s a low-waste configuration that can be made for the site.
In addition, the simulation can find ways to reduce physical waste. Perhaps changing the process will reduce the failure rate and increase the yield percentage. This is yet another way that simulation in sustainability works so well.
3. Design
Simulation software can help organizations to optimize their factory designs, be it floor space, production or process flows. Many manufacturers can be primarily focused on productivity gains from the use of simulation software to test new processes, but may not be aware of the energy-saving benefits of making small changes to ensure floor space is used in a more efficient way. The software also enables the creation of smart factories on existing brownfield land and helps to use less greenfield space. This further supports the development of digitization as part of the Fourth Industrial Revolution.
See how DHL designed, optimized, and verified the packaging process and production feasibility using 3D manufacturing simulation.
Design can also be used to describe single products. By designing a new product line via simulation technology, you can work out the early bugs before physically making a prototype. In practice, a product can go through a number of iterations before a final unit is agreed upon.
Each of these iterations involves time, money, and manpower. With a design in a simulated environment, you can expedite the process while saving money. You can even test the range of motion on a complicated part, all digitally.
4. Packaging
With the war on plastics a key element of sustainability, organizations are increasingly looking for ways of ensuring environmentally friendly packaging materials are used in the manufacturing process, whether it’s beverages, food, or other items. When it comes to packaging, much of the cost comes from expensive product trials and inefficiencies.
Simulation software can be used by packaging and palletizing organizations to test different materials, achieve efficiency gains, and achieve fewer usage of plastics. How does it work? The designer will model the unit as well as the packaging around it. They can use a number of simulation environments to find ways to optimize the packaging.
After that, they can simulate a dynamic stress test to see if the packaging will withstand transit, and make adjustments accordingly.
This software can find a theoretical minimum amount of material that needs to be used in order to achieve transport-safe packaging. Doing the same tests with physical packaging will cost a lot of money and require some extensive lab space and equipment for full testing.
5. Supply chain resilience
Lastly, simulation software can be used to develop a resilient supply chain, helping simulate elements of the wider chain to ensure that more transparent processes are applied to the real environment. This way, manufacturers can future-proof operations both on the shop floor and in their supply and delivery processes.
A major way to do this is by incorporating as much of the manufacturing process as possible. By doing more steps in-house, your operation can ignore outside supply chain issues. Meanwhile, companies who rely on a series of outside vendors could suffer financial and budgetary losses when something goes awry.
The software’s role in long-term sustainability
The battle against climate change becomes more urgent. With simulation software able to make an impact on the sustainability agenda in several ways, its importance is clear. Trade associations utilize the software to increase understanding of sustainability and communicate this to the industry. This will prove particularly beneficial to smaller organizations that are members of these associations. They typically need assistance when it comes to devising an effective strategy as they don’t have a chief sustainability officer in place.
Simulation software is now also used in academia and research, such as research centers and universities, and is playing its role in training the engineers of tomorrow. This is enabling a long-term understanding of sustainability for professionals pursuing a career in the manufacturing space, and helping to bridge the skills gap.
Read how students in Coventry University’s Electro-Mechanical Engineering use Visual Components’ 3D simulation software to carry out factory floor simulation.
The use cases of simulation software across these five core areas and its ability to impact both organizations and their people reveal a strengthened link between technology, innovation, and sustainability moving forward. By harnessing emerging technologies such as simulation software, manufacturers are better placed to ensure that sustainability is a key part of their business strategy and operations.
Further reading
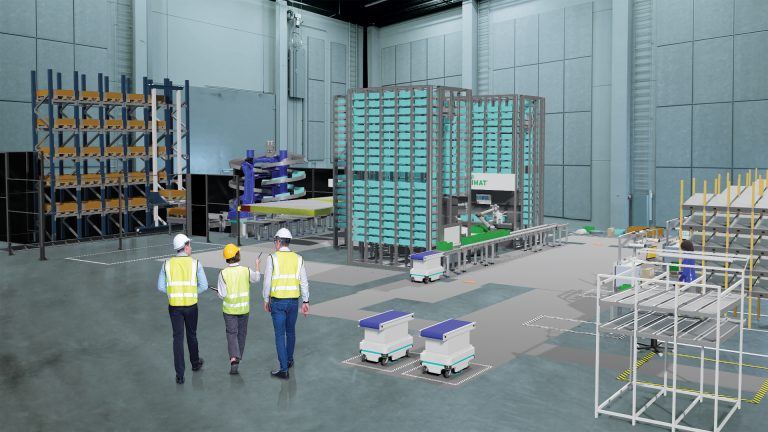
The future of automated manufacturing (and why humans still matter)
Automation in manufacturing has been evolving for decades, but its true impact isn’t in replacing people, it’s about making them more capable. We spoke with Mika Anttila, one of Visual...
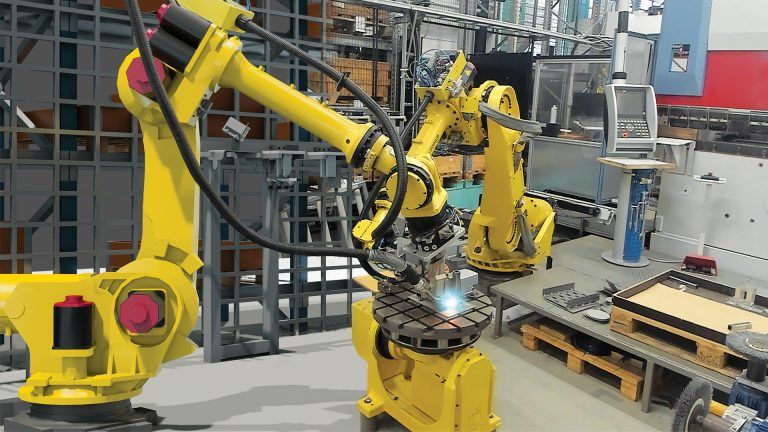
Understanding digital twins in manufacturing
Digital twins go far beyond static models or simulations. They bridge the gap between virtual and physical systems, offering real-time insights and control. But with so many definitions floating around,...
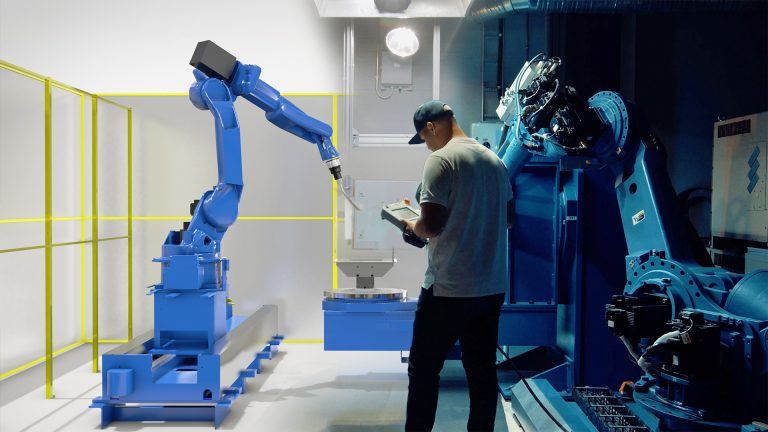
Tackling the manufacturing skills shortage with simulation and robot offline programming
The manufacturing industry is grappling with a significant skills shortage, exacerbated by the pandemic and an aging workforce. According to The Manufacturing Institute, 78% of companies are concerned about this...