Solutions
Robot programming
Robot offline programming allows you to program industrial robots for various processes without interrupting production. Create efficient, error-free robot programs on computers using your 3D CAD data and download to the physical robot.
Faster robot investment payback
Program robots 10 times faster without stopping production. Ensure fast robot ramp-up time and minimal downtime. Save and re-use your programs for future projects to enhance efficiency and productivity.
Improves production efficiency
Ensure products are made to the highest standards of quality consistently by optimizing robot movements and processes for peak efficiency and precision with minimal robot downtime.
Supports design for manufacturing
Eliminate last-minute modifications to fixtures and tooling. Thoroughly test and adjust virtual models of the robot cell and production setup well in advance of actual production.
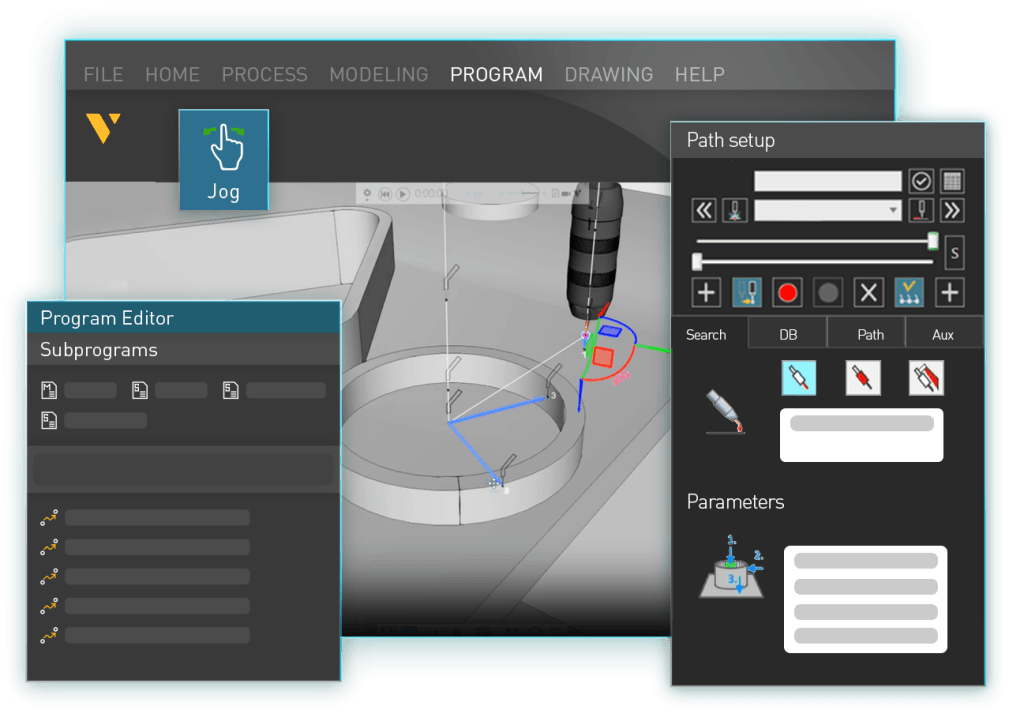
Why program your robots offline?
Imagine programming a robot to weld a circular part on a metal workpiece. The robot needs to move the welding torch in a 3D arc around the circumference of the part, and at the same time maintain a precise orientation with respect to the surface.
You can do this by teaching points with a pendant, but you’ll need a lot of points and it will take a long time. The gap between the torch will almost certainly vary, as will the orientation of the torch. What’s more, the robot cell won’t be available for production until you’ve finished programming. This downtime can last from days to weeks, resulting in lost production.
With robot offline programming, producing robot programs is faster, easier and more accurate. By importing a CAD model of the welding cell into offline programming software, you can easily define the desired torch path. The software then generates and verifies the robot program, checking for issues such as potential collisions. Once the program is verified, you simply download it to the robot controller, perform a low-speed test for confirmation and the cell is ready to resume production.
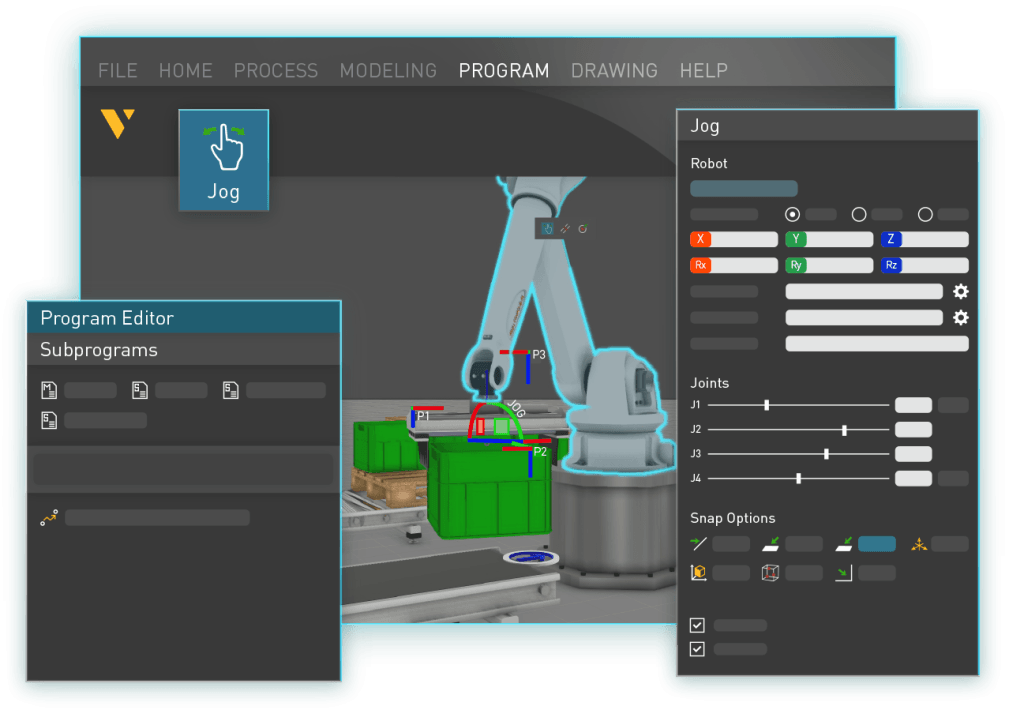
What is robot offline programming?
Robot offline programming is a method for programming robots without directly working on the physical robot or disrupting production. By using virtual models of the robot and its environment, you can plan, program and optimize robotic tasks in a digital space.
Once the program is verified for accuracy and safety, it is downloaded to the robot controller for execution. This approach reduces programming time, increases precision and maximizes production uptime by eliminating the need to halt operations during programming.
This is critical for pre-planning complex robot operations, ensuring efficiency and mitigating risk. Manufacturers using robot programming software have reported an 80% reduction in robot programming time and a 95% increase in robot utilization.
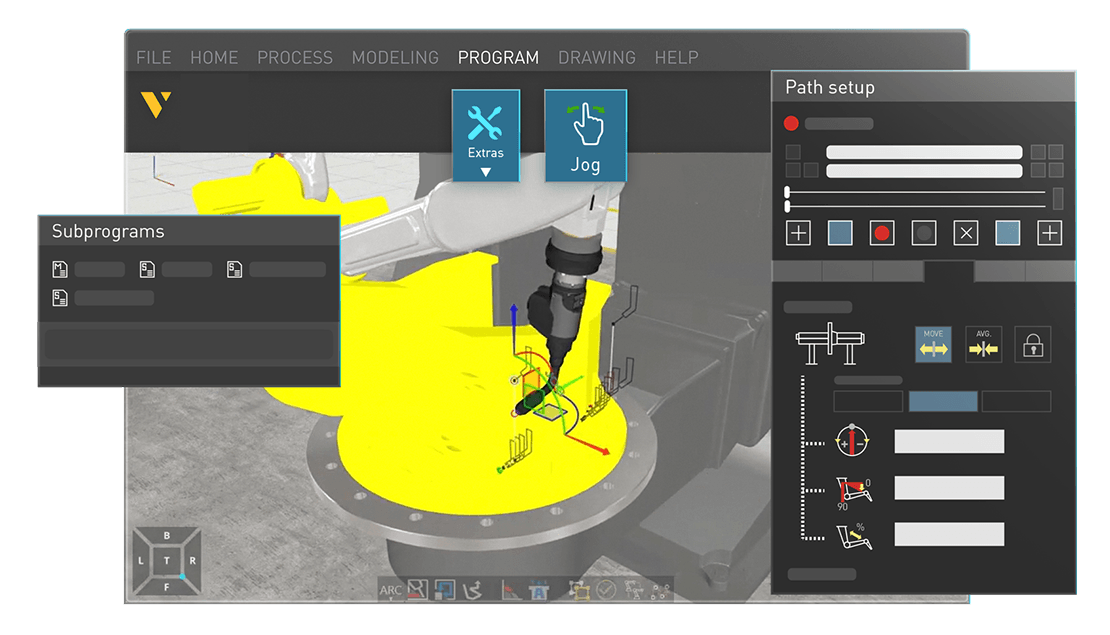
Evolution of robot programming
Robot programming has evolved significantly over the years. Initially, robots were programmed manually by physically moving the robot arm to the desired positions. In the 1980s, CAD technology enabled robot simulation and offline programming, converting CAD data into robot motion programs.
Today, modern robot programming software supports various robots and offers automated programming and collision-solving capabilities, enhancing efficiency and accuracy. Robot cell calibration ensures the virtual model matches the real work cell, achieving a digital twin.
The first industrial robots were programmed using a method known as teaching. In this approach, the robot arm was physically moved to the required position, and the pose—comprising the tool center point’s (TCP) x, y, z coordinates and rotations—was saved. Essentially, this involved recording the position of each joint motor to define the robot’s movements.
Robot simulation began to emerge in the 1980s, leveraging CAD technology to visualize the robot, its movements, and the surrounding workcell or environment. Soon after, techniques were developed to convert position data from CAD programs into robot motion programs, much like generating machining paths for CNC machines. This innovation marked the advent of robot offline programming.
Today, robot offline programming comes in two main forms. Many robot manufacturers offer proprietary programming software alongside their teach pendants. Alternatively, users can choose independent robot offline programming solutions, which are robot brand-agnostic and can support a variety of robots from different manufacturers.
The effectiveness of robot offline programming depends heavily on how accurately the CAD model represents the real workcell. To bridge the gap between the virtual model and the physical setup, users must perform robot cell calibration. This involves measuring key reference points in the workcell, capturing the actual poses of the robot’s tool center point (TCP), and identifying the positions of peripheral equipment. These measurements are fed into the robot offline programming software, which uses calibration programs to align the CAD model with the real-world layout, thereby achieving a digital twin. Measurements can be taken using the robot itself as a measuring tool or with external devices like 3D laser scanners.
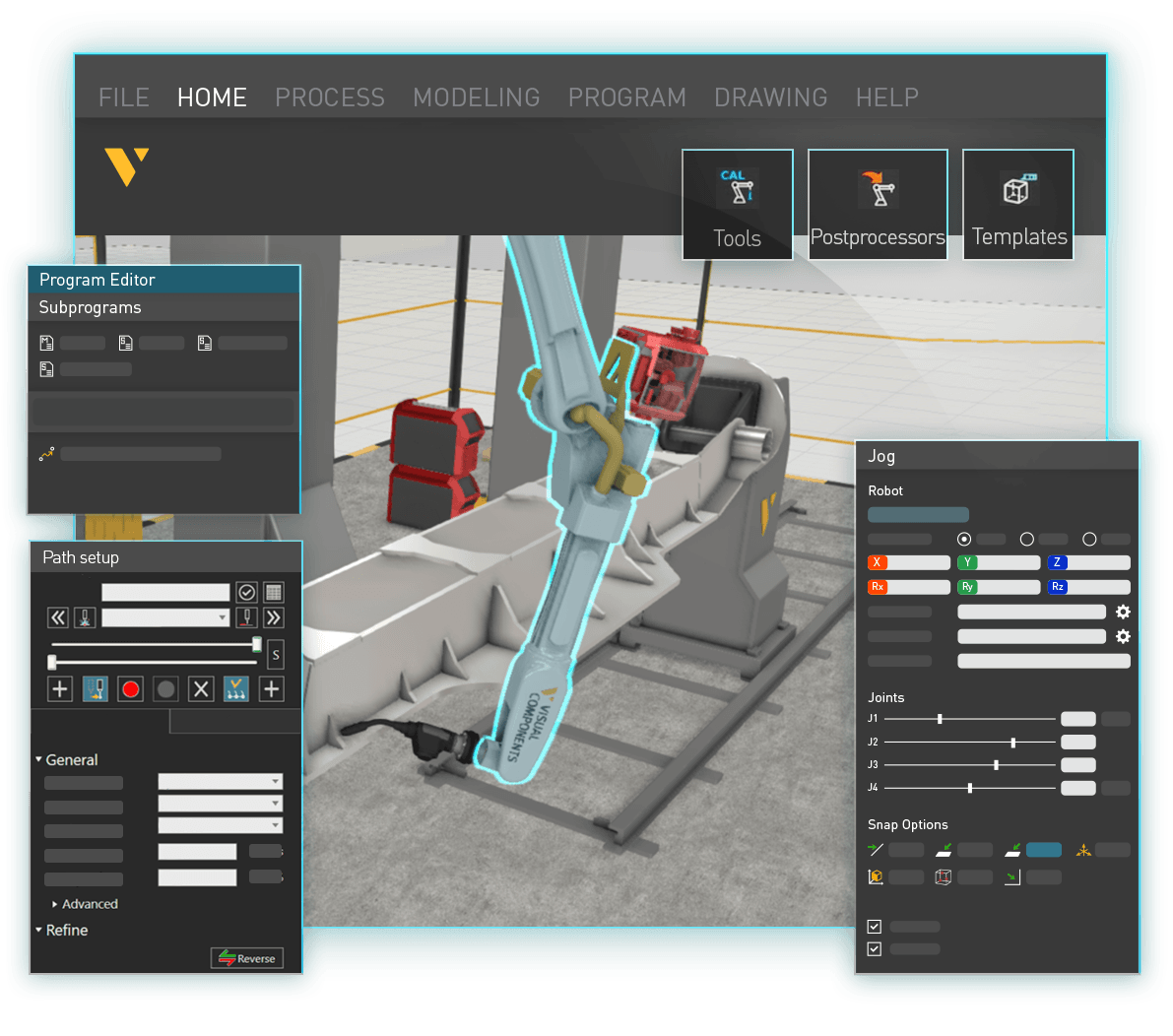
Robot programming with Visual Components
Robot programming should not be complex, repetitive or time-consuming. Robot programming software should enhance production flexibility and adaptability and enable repeatable quality with accuracy.
Visual Components offers the fastest and easiest offline programming software, supporting all levels of automation. From one-click programming to fully automated model-based definition (MBD), it is compatible with all major industrial robot brands, processes and complexities. This helps you maximize quality, robot utilization rate and production output.
Robot programming options
Online programming
Pros:
- “Free”, no software investment required
Cons:
- Production and robot downtime
- Complex, time-consuming
- Unique programming language
- Quality inconsistency
- Safety and accessibility
Offline programming solves many of the challenges associated with teach pendant programming. It eliminates production stoppages, is convenient, safe, fast and is compatible with different robot brands. It can start from product design using CAD files, ensuring greater flexibility and efficiency.
Machine vision-based programming
Pros:
- Real-time information exchange
- No position or fixture requirements
Cons:
- Robot programming is still required
- Inaccuracy and unreliability in uncontrolled environments
- Can only start after some parts are manufactured
- Limited to simple parts
Offline programming offers a more reliable and versatile solution, delivering precise and consistent results without stopping production. It is not restricted to simple parts and can start from the product design stage using CAD files, offering greater flexibility and efficiency.
Robot offline programming
Pros:
- No production stoppage
- Convenient, safe, fast
- Third-party OLP software supports different robot brands, offering greater flexibility
- Can start from product design already with CAD files
Cons:
- CAD file required
- Manufacturer-specific OLP software only support their own robots, limiting compatibility
What are common offline programming applications?
Access and orientation are particular challenges that robot offline programming helps with. For example, complex weld beads can require large numbers of points.
Applications like bead blasting and deburring often need long, complicated paths that require a lot of points.
As with welding, orientation is important in painting applications. Unified paint thickness and standoff distance are equally important, plus ensuring all areas can be reached and painted optimally.
Grasping and insertion-type moves need precise control over gripper orientation, which is achieved at a higher level with robot offline programming.
Plasma or laser or waterjet cutting may work for standard parts. But for complex geometries, robots are needed with accurate cutting patterns that can be generated with offline programming.
Many assembly operations require the deposition of long, complex adhesive beads: robot offline programming helps create the tool paths rapidly with consistent quality.
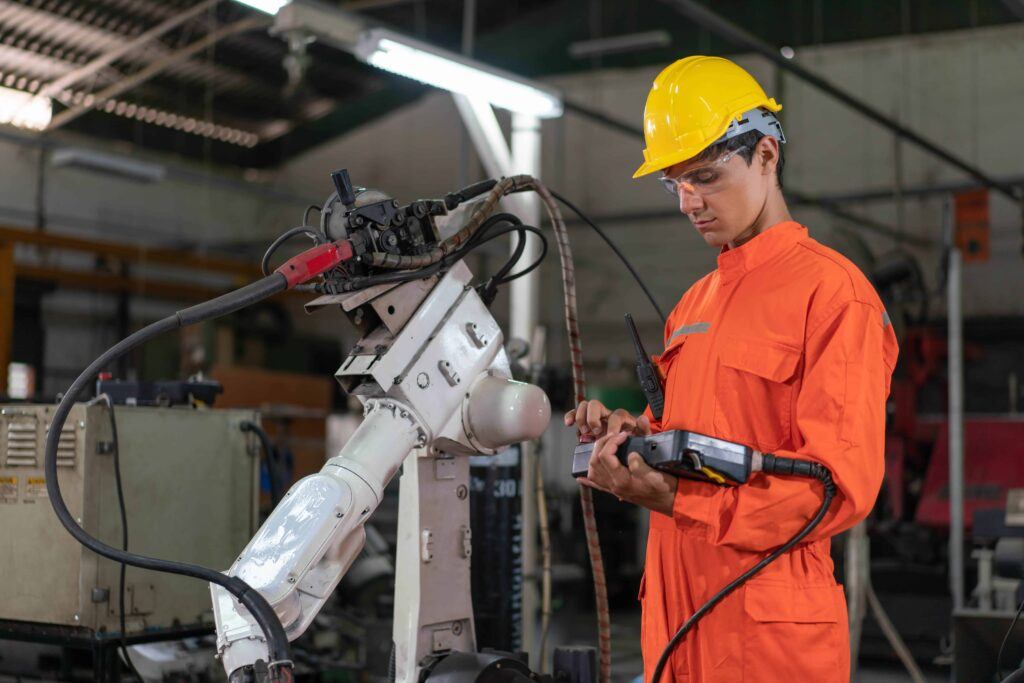
For robot programmers
Save time on manual robot programming and rework so you can focus on more important priorities.
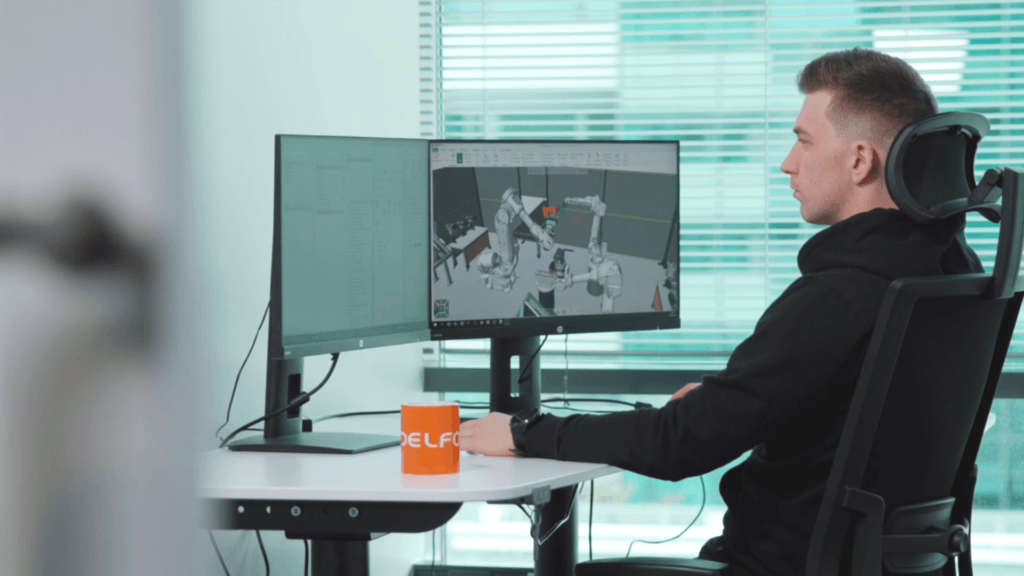
For manufacturing engineers
Easily collaborate and validate design and fixture feasibility before production.
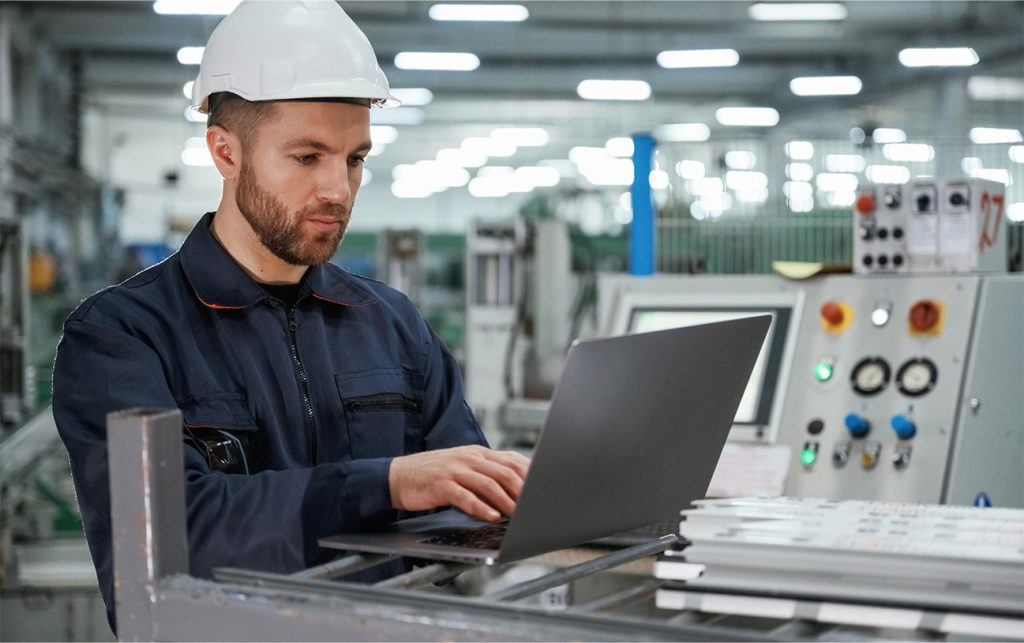
For production managers
Save 10x programming time without stopping production. Maximize quality, robot utilization rate and production output.
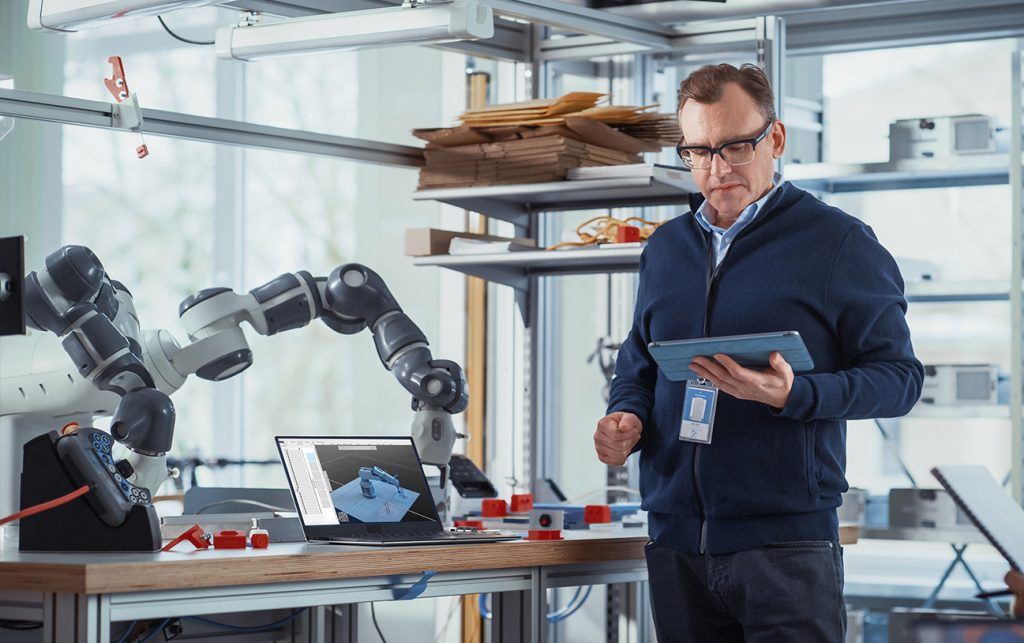
For robotics managers
Maximize quality, robot utilization rate and productivity to shorten robot investment payback period.
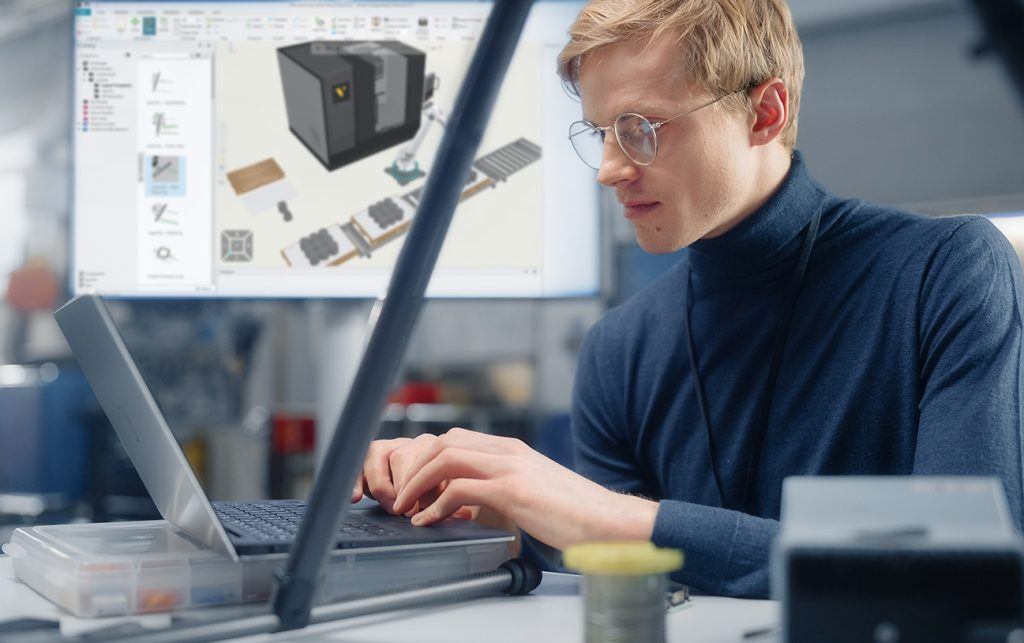
For system integrators
Easily create a digital twin to optimize proposals for accuracy before delivery. Stay competitive by delivering quality and achieving customer satisfaction.
FAQ
Robot offline programming (OLP) is a method of generating robot programs in computer software (virtual environment) based on 3D CAD data. Once the robot program is generated and verified in the software, it can be downloaded to the physical robot.
The effectiveness of OLP depends on how accurately the CAD model represents the work cell. To capture the real layout of the cell, not just what’s represented in CAD, users must perform a process known as robot cell calibration. This involves:
- Measuring a set of reference points within the cell.
- Recording the actual position of the robot’s Tool Center Point (TCP) and the locations of periphery equipment in OLP.
- Running specific calibration programs to align the model with the actual cell, perfecting the digital twin.
Measurements can be taken with the robot itself or with external devices such as 3D laser scanners.
This stems from the assumption that high production volumes are needed to benefit from OLP. The reality is a slightly different story. OLP is especially beneficial when the production runs are short, setups or changeovers are frequent, and there’s a lot of variety in the tasks. Small and mid-sized manufacturers can greatly benefit from OLP if they are running small-batch production.
Like any software, OLP requires some training and has a learning curve. Plus, there are probably some OLP products that are not particularly user-friendly. The best products though are intuitive, logical, and easy to use, letting novice users quickly become proficient. Furthermore, don’t underestimate the complexity of programming by robot teach pendant. Different robot brands have different commands and then additionally the systems can change from older to newer robot models. This makes it even more complicated to use manual programming.
An OLP software is an additional purchase. However, it only needs buying once and can support whatever brands of robot a facility uses. (This also helps a facility avoid being locked into a single robot vendor.) OLP users report improved ROI from their robot cells, as downtime is reduced, and robot utilization increased. There’s evidence it can cut robot downtime due to programming by as much as 90% and can pay for itself on a single project.
Users of OLP software report multiple benefits:
No robot downtime
Programming time can be reduced up to 80% and robot utilization increased by as much as 95%, boosting programmer productivity and cutting cell downtime.
Quick set-up time
Less time is needed to launch a new product into production – programming happens concurrently rather than sequentially.
Enhanced workplace safety
Reduced risk of accidents and injuries.
Higher and repeatable quality
Robot programs are better optimized, (shorter cycle times, higher accuracy and consistency,) resulting in higher and repeatable production quality.
Robot brand and process agnostic
Regardless of robot brands or types of processes, advanced OLP software can cover all applications.
Avoid rework and delays
Last-minute fixture and tooling modifications are avoided.
OLP software speeds up program creation, reducing the time required for programming, but it does not eliminate the need for skilled programmers. Path planning and optimization, collision avoidance, and so on are all best done by an experienced programmer. However, OLP software can make them more productive, giving them time to work on more complex programming tasks and innovate in a safer work environment.
Yes, OLP can reduce on-site robot programming by generating accurate robot programs to minimize touch-ups. For example, programs generated in Visual Components OLP software are error-free. In most cases, touching up on-site is not necessary at all, provided some form of seam search functionality is used.
OLP can help detect common robot problems taking place during program execution. For example, using the collision detection and path check tools in Visual Components OLP software, you can easily troubleshoot and fix reachability, joint limits, singularity and collision issues efficiently from your workstation.
When considering OLP software, evaluate whether the software covers all robot brands, processes, and complexities for your current and future needs. After evaluating the technical capabilities, it is also important to consider whether you will receive the technical support you need to ensure implementation and commissioning success. Finally, request a demo to see and try it for yourself.
How are our customers using Visual Components for robot programming?
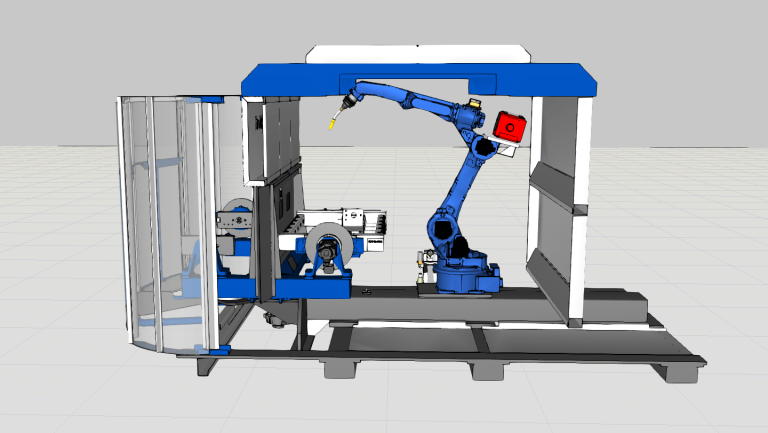
Maximizing efficiency and ROI from day 1: Duun Industrier pre-programs a welding robot cell with Visual Components OLP
Duun Industrier, a leading Norwegian heavy machinery manufacturer, installed the Nordics’ largest robotic welding station in 2013. Utilizing Visual Components for robot programming since 2014, they commissioned a new robot…
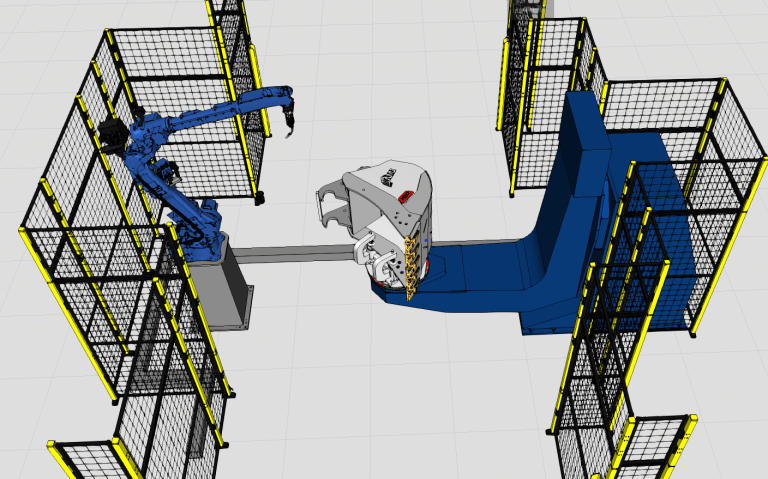
Combatting the welder shortage: how AMI Attachments enhances production efficiency with Visual Components OLP
AMI Attachments, a leading North American manufacturer of heavy equipment attachments, sought to improve product throughput and meet evolving market demands while navigating a welder shortage. By implementing Visual Components…
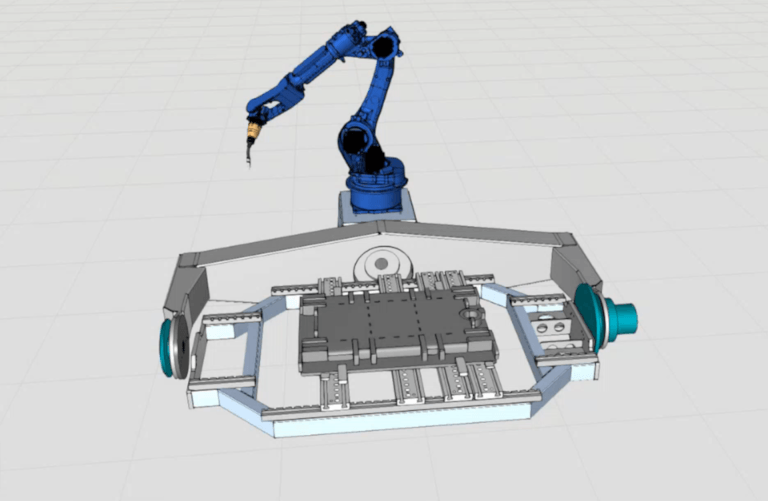
Mastering complex welding: Bunorm Maschinenbau’s quality and efficiency boost with Visual Components OLP
Bunorm Maschinenbau, a full-service supplier known for complex welding solutions, is committed to maintaining a high level of modernization and flexibility of their infrastructure. With their wide-ranging capabilities, the focus…
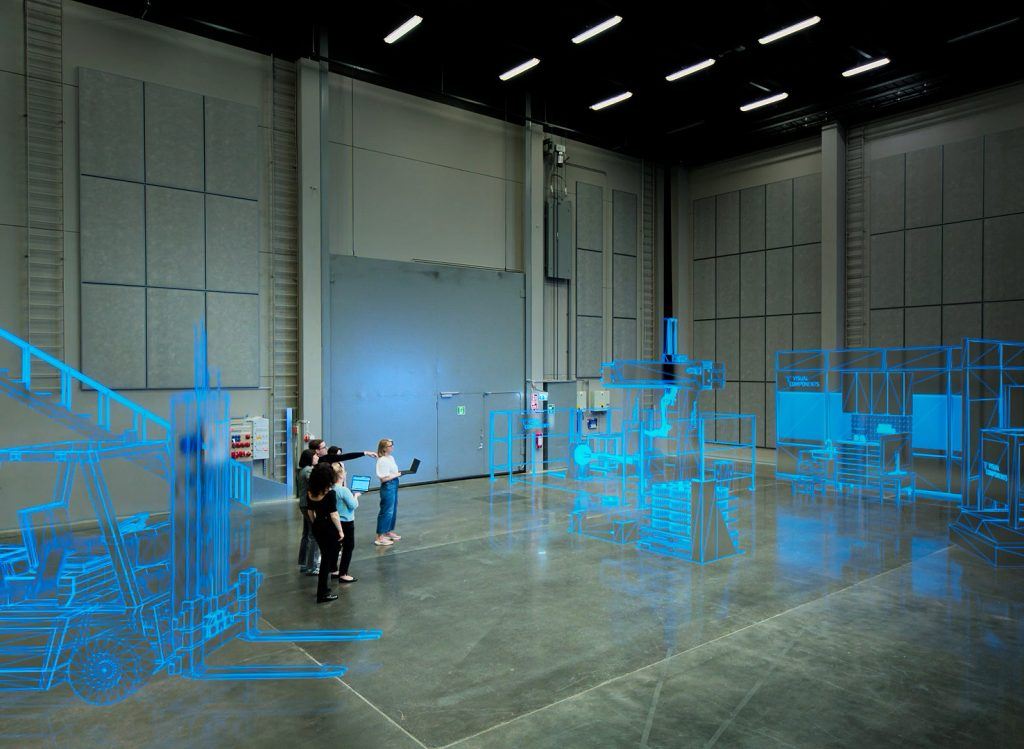
What is the future of robot programming?
The future of robot programming is being shaped by several key developments that enhance automation, efficiency and collaboration. This evolution marks a significant transition from manual and isolated processes to more integrated and intelligent systems.
These automation and AI advancements will significantly improve efficiency, with AI playing a crucial role in helping robot programmers create and optimize robot programs more efficiently.
This will promote collaboration between different teams, ensuring that robot programming is aligned with overall design and manufacturing goals. CAD models can include weld models from the outset, streamlining the entire process.
Master robot programming in Visual Components
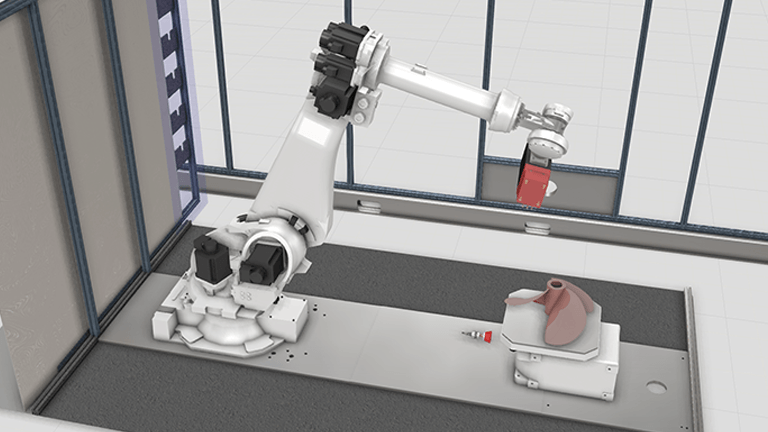
Introduction to Robotics OLP
An overview of different robotic processes in Visual Components Robotics OLP, from welding, processing to spraying.
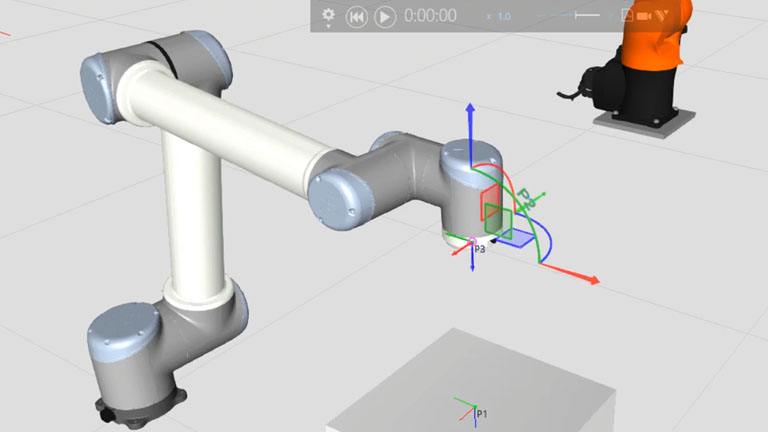
Introduction to robot teaching
Learn how to use an articulated robot, including exchanging robots, testing programs, adding a suction gripper, and configuring signals for part manipulation.

Basics of robotics
An overview of robotics in Visual Components and includes topics such as point-to-point motion, linear motion, robot base frames, robot tool frames, robot configurations and robot turns.
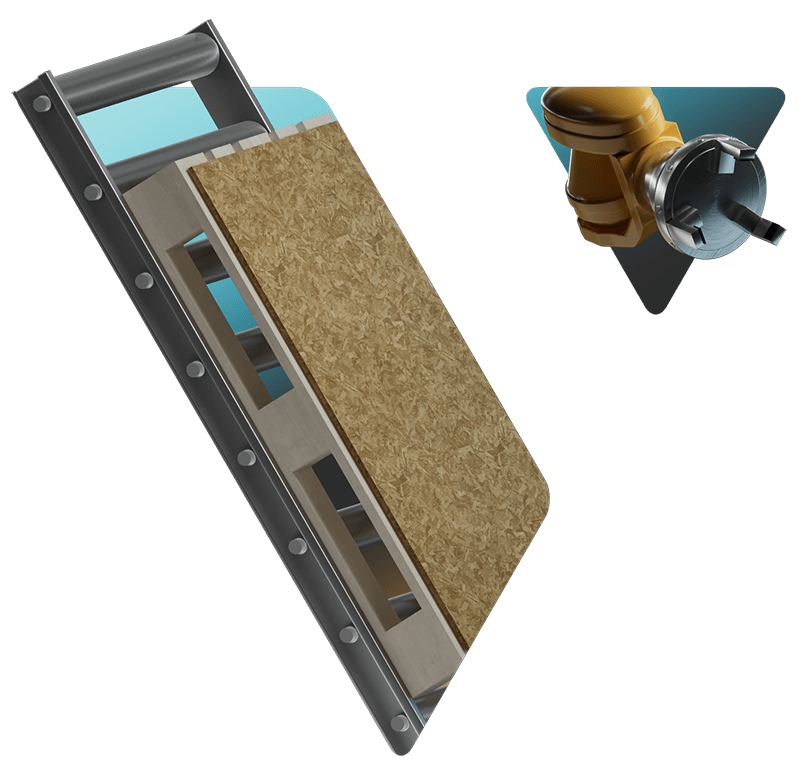