Going beyond the Robot
Why should you go beyond the robot to optimize your factory processes?
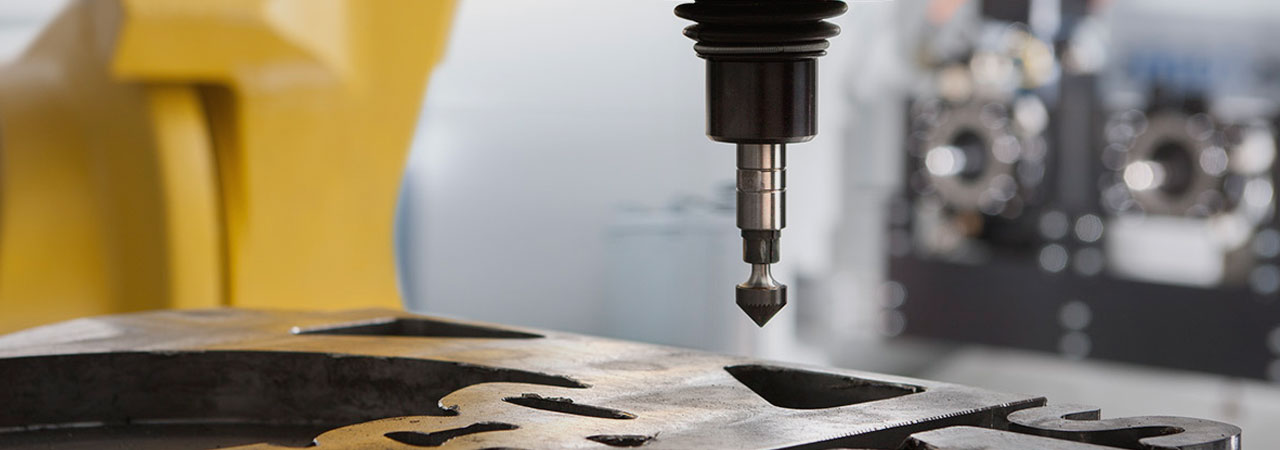
How can robot manufacturers go beyond the robot?
Traditionally, robot manufacturers have developed independent software solutions to simulate the motion of their robot models. These proprietary solutions are typically limited to emulating the motion paths of their standard robot models. The robot simulators execute the motions of the robot based on their individual post processors in their native robot programming language.
There are, however, other dynamics, disciplines and conditions to consider when developing a complete robotic system. Things to consider include application programming, equipment interfacing, material flow, resource planning and programmable logic controller (PLC) validation. In other words, in order to optimize your factory processes, you must go beyond the robot.
3D simulation for a complete robotic solution
An integral part of a complete robotic solution is providing statistics and analysis relative to production optimization to evaluate best-case scenarios. The ideal simulation model must also provide validation and verification of equipment reachability, collision or near miss detection and data records of full analysis and statistical values.
For example, a total robotic solution should address the material or product flow to and from the robot cells. What is the optimized footprint for manufacturing and/or the maximum production rates expected or anticipated? Is there room for process improvement? Can manufacturing be improved to increase production or reduce cost?
The missing link in the complete solution has been the validation of the I/O programs. Using 3D simulation, the verification of all control signals can be viewed, functionally mimicked and finalized within the same simulation to meet the demands of the launch schedules with easy reference for maintenance/repair. You can virtually imitate the I/O signals from a virtual or real robot and identify issues or conditions well ahead of the actual launch of production.
Furthermore, the ideal model for a 3D Simulation tool should not only provide performance for all types of simulation and have an open and flexible API, it must also serve a market that spans from small shops to major OEMs, and address the needs and requirements from sales, marketing and engineering. It must be easy and usable for everyone.
One solution, one platform
Granted, there are many 3D Simulation providers. Some address the individual requirements of the manufacturing process, including robotics, material flow, resource/process planning or PLC validation. Others provide all of these features. However, these are often multiple product and multiple platform solutions, forcing the buyer to make costly investments and pay maintenance costs.
In order to optimize your costs and work flow, you should find a one solution, one platform product. For example, Visual Components delivers an easy-to-use solution set that can be used to manage OLP, factory flow, resource and process planning, and virtual commissioning using real data. It is already being used in some format by some of the largest robot manufacturers in the world such as KUKA, Universal Robots, Stäubli, Mitsubishi and Epson.
Further reading
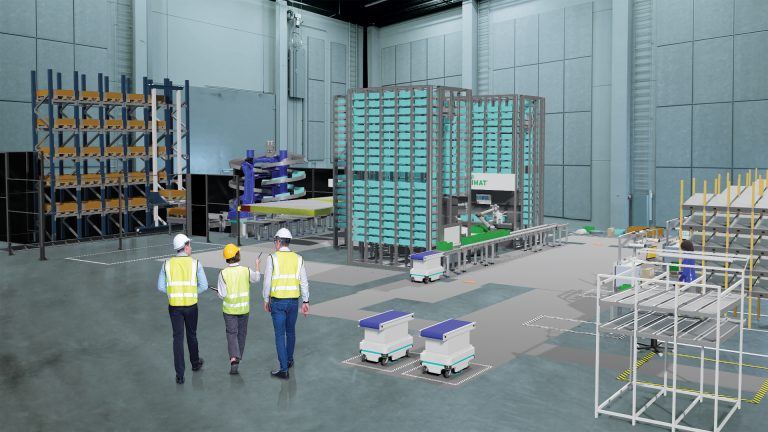
The future of automated manufacturing (and why humans still matter)
Automation in manufacturing has been evolving for decades, but its true impact isn’t in replacing people, it’s about making them more capable. We spoke with Mika Anttila, one of Visual...
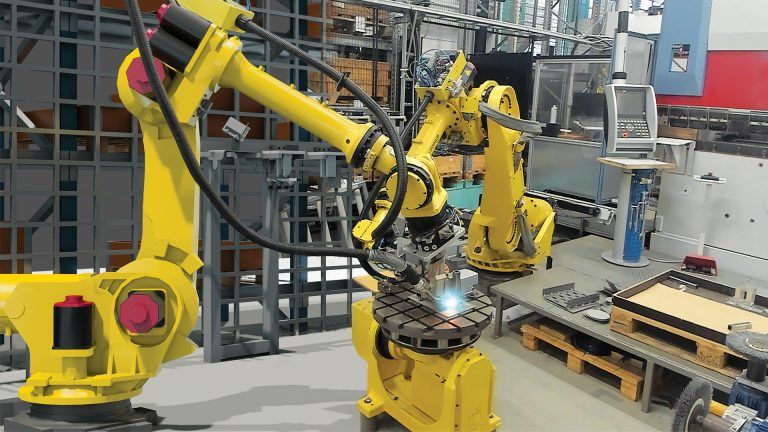
Understanding digital twins in manufacturing
Digital twins go far beyond static models or simulations. They bridge the gap between virtual and physical systems, offering real-time insights and control. But with so many definitions floating around,...
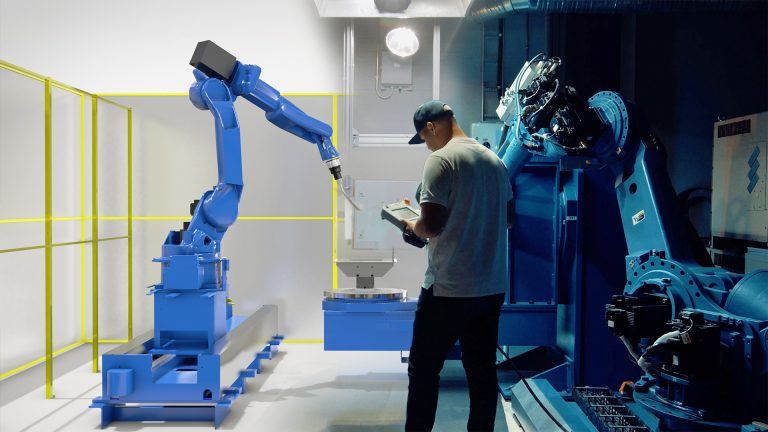
Tackling the manufacturing skills shortage with simulation and robot offline programming
The manufacturing industry is grappling with a significant skills shortage, exacerbated by the pandemic and an aging workforce. According to The Manufacturing Institute, 78% of companies are concerned about this...