Automation and robotics trends in 2023
In industries around the globe, leaders are deciding how to get the most from limited investment budgets. Never a straightforward task, economic uncertainty, workforce challenges and fast-moving automation and AI trends serve only to complicate decision-making. Is automation the answer? What role should smart manufacturing play, and how can tools like manufacturing simulation software help?
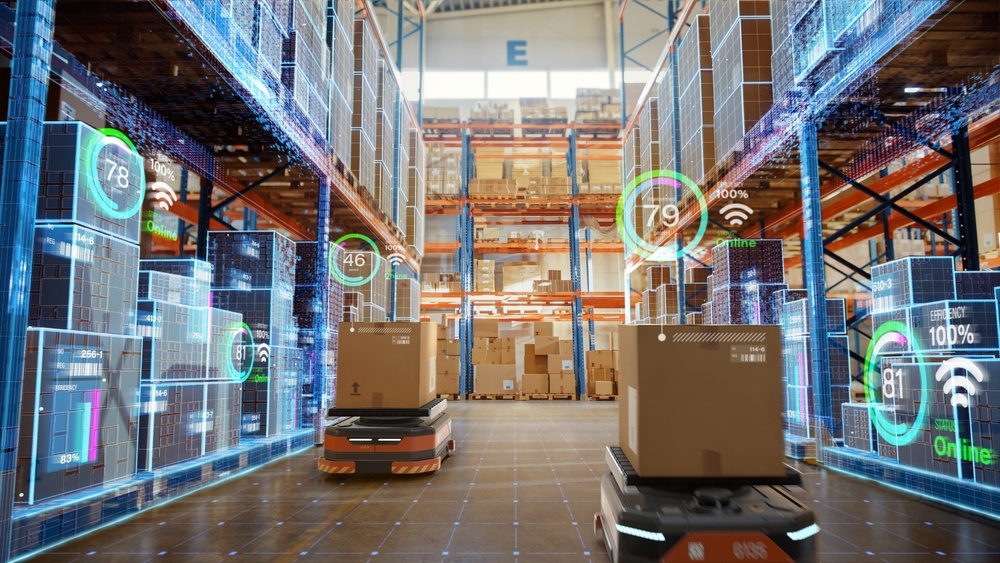
The pandemic and related supply chain issues seem largely in the past, but problems persist. Energy and material costs continue to rise, and in many industries, an ageing workforce is nearing retirement while recruitment remains difficult. Industrial automation is offered as the solution, but are there other manufacturing trends to watch and adopt?
This article aims to help directors, managers and other leaders in industries like manufacturing and logistics understand how technology can help address these challenges. Individual sections cover:
- The State of Robotics and Automation in 2023
- Economic Uncertainty
- Advances in Artificial Intelligence and Machine Learning
- Advances in Smart Manufacturing
- Impact of Robotics and Automation on Employment and the Job Market
- The Future of Robotics and Automation: Opportunities and Challenges
- How Robotics and Automation Will Shape the Future
The state of robotics and automation in 2023
One way of automating a task or process is through robotics. A major advantage of robotics over dedicated or “hard” automation is flexibility. The robot can be assigned to a new task quickly and often at no cost. Conversely, with hard automation even a small change in the product or process can be expensive and difficult to implement.
Since the first industrial robot went to work in 1961, robots have been viewed primarily as material handling or tool manipulation machines. Today though, the definition has expanded to cover both physical and business process robotics.
In the field of physical automation, autonomous mobile robots (AMRs) have joined the four, five and six-axis machines populating factories the world over. These AMRs roam warehouses and distribution centers, moving materials and kits between storage, kitting and packing.
Process robotics refers to robotic process automation (RPA). This is technology used to automate repetitive paperwork and administrative tasks.
Today robotics and automation are in the vanguard of the fourth industrial revolution, or Industry 4.0. Smart sensors, communication technologies, analytics tools, machine learning and artificial intelligence, are enabling data-driven decision-making. In parallel, the European Union (EU) is pushing the idea of Industry 5.0 – a vision of connected smart manufacturing that puts people at the center rather than relegating them to the periphery.
Now, with the outlook for 2023 and beyond unclear, business owners, managers, engineers and technologists are looking to this data for insights into where to put investment funding.
Economic uncertainty defining 2023
Investment in automation is a vote of confidence in the future, but when future demand and growth are hard to predict, as is the case today, industry leaders become more cautious about where to invest. Two recent reports, one from research and business advisory specialists Forrester, and the other a survey commissioned by Visual Components, provide depth and color to this outlook.
Forrester, in their “Predictions 2023: Automation And Robotics” report, say to anticipate, “a modest deceleration of automation progress in 2023 due to uncertain economic conditions.” This is expected to increase focus on projects driven by efficiency and improving resilience, leading to:
- Greater use of data generated by smart manufacturing and machine learning technologies
- The efforts of Centers of Automation Excellence being directed more to efforts that support the entire business rather than subsections
- A shift of budgets towards projects addressing business continuity-type issues (such as skills shortages)
- The continued growth of the physical robot population
Supporting this last point, in their Industrial Robots 2022 review, the International Federation of Robotics (IFR) reported strong growth in robot numbers around the world. Furthermore, the Association for Advancing Automation (A3) reported that 2022 saw strong demand for industrial robots in North America.
The focus of the survey undertaken for Visual Components was to discover how manufacturing businesses are responding to the push towards Industry 5.0. Key findings included:
- People-related costs are rising
- Shortages of technology skills should not be overlooked
- Economic uncertainty is holding back sustainability efforts
Advances in artificial intelligence and machine learning
The deployment of artificial intelligence (AI) and machine learning (ML) are currently two of the biggest trends in robotics and automation. While closely related, the terms are not interchangeable.
AI refers to software that is trained to perform a specific task, rather than programmed. This saves the programmer from having to anticipate every possible set of conditions, possibly saving time, but also greatly extending capabilities.
ML is part of AI. On their web page, “Artificial Intelligence (AI) vs. Machine Learning”, the engineering department at Columbia University describes ML as “… a pathway to artificial intelligence,” going on to say that ML, “…uses algorithms to automatically learn insights and recognize patterns from data, applying that learning to make increasingly better decisions.”
AI and ML have a growing list of applications in robotics and automation. They are used to optimize routing planning, provide decision support, improve safety, optimize material yields and increase factory efficiency.
Examples include:
- Automating detection of defects in images of parts or materials
- Guiding robots performing loading, unloading and assembly tasks
- Improving the ability of AMRs to navigate cluttered and busy surroundings
Advances in smart manufacturing
Industry 4.0 is about manufacturers digitizing processes for increased efficiency, higher quality and lower costs. Industry 5.0 is an initiative from the EU aimed at reminding manufacturers people will remain integral to manufacturing for the foreseeable future.
Without this, current automation trends will result in human workers having less autonomy over their jobs. The danger is that increasing use of sensors and analytics will result in everything being measured, effectively reducing human factory operators to little more than automata.
Research group Forrester proposes manufacturers adopt an “Automation Triangle” that merges the capabilities of hardware and software automation capabilities with human workers’ adaptability, creativity and resilience.
In this concept, repetitive tasks are handled by hardware automation, and software automation performs repetitive data processing and analytical functions. This frees people to supervise the automation and address issues like sustainability.
The approach offers human workers many benefits. Once freed from the unpredictability of current manufacturing activities, uncertainty and stress are reduced substantially. They have more opportunities to exercise their creative skills and significantly greater autonomy over their work. The benefit for employers is a workforce that’s more motivated and engaged.
Impact of robotics and automation on employment and the job market
For several reasons, factories will not become the “lights-out” operations once envisioned as the inevitable conclusion of industrial automation trends. It’s now understood that not every task is suitable for, amenable to, or done better by automation. Plus, despite the advance of AI, creativity, adaptability, and resilience have important roles to play. What’s more, financial constraints will prevent manufacturers from pursuing an “automation at all costs” approach. However, there will be more automation in places where it makes financial sense.
This will affect the mix of skills needed in future manufacturing facilities. These can be grouped under the headings of:
- Integration costs
- Technical challenges
- Skills shortages
- Security concerns
Integration costs
Industrial automation must be up-and-running in the least time possible. Three tools for making this happen are manufacturing simulation, robot simulation software, and digital twins. Used separately or preferably together, these enable the identification of optimal approaches by allowing the evaluation of more options. In addition, a digital twin facilitates virtual commissioning, which detects integration problems early while there’s still time and budget to remedy them.
From a workforce perspective, manufacturers will need people with the skills to use these tools. Alternatively, they will have to contract with partners that can use them and address integration issues on their behalf.
Technical challenges
One of manufacturers’ biggest challenges in adopting smart manufacturing technologies is choosing the right solutions. Two issues here are, first, defining the opportunity or problem correctly, and second, determining what form the automation should take. Manufacturing simulation is a powerful tool for exploring alternatives and determining which offers the optimal solution. Process modeling can, for example, be used to simulate operation of resources like AMRs.
Skills shortages
Many manufacturers face an ageing workforce and challenges in attracting new recruits. Automation and robots offer solutions in several ways.
Robots can perform repetitive tasks like welding, which is one example of a trade suffering high rates of retirement.
RPA and AI can take on repetitive and analytical tasks, likely performing with higher consistency than human workers can provide
The high technology environment created by using advanced tools like AI and robot simulation software will provide a powerful draw to younger and highly educated technical professionals.
Security concerns
Business leaders are well aware of the need to protect their data, and this will only become more important as manufacturers become increasingly digitized. IT functions will continue creating separate Operational Technology (OT) networks, but the increased demand for technical specialists may prove a constraint to how fast they can move.
Cloud computing creates additional vulnerabilities: awareness is high, but safeguarding measures are needed nevertheless. One exception relates to applications where AI must quickly decide or respond. In these cases, more computing will be done at the edge than in the cloud so as to avoid latency issues.
The future of robotics and automation: opportunities and challenges
It’s clear robotics and automation technology are growth enablers. However, manufacturers must be willing and able to adapt to an environment that continues to evolve rapidly. The principal issues to address are:
- Investing in R&D
- Upgrading infrastructure
- Providing training and education
- Implementing strong security measures
R&D investment
Businesses should seek innovative ways in which to benefit from AI and other smart manufacturing trends. This will be done in a controlled and targeted manner to minimize the amount of risk taken on. Tools such as digital twins and manufacturing simulation will support these endeavors, permitting experimentation in a virtual rather than physical space.
Infrastructure upgrades
If one thing is clear from current automation trends, it’s the ever-growing role of data. Data underpins digital manufacturing, and factory systems and networks must be configured for the volumes and speeds required. If one example illustrates this trend, it’s the rollout of true digital twins. These require high-speed bi-directional data transfer to keep the physical and the virtual in sync.
Providing training and education
Already severe, skills shortages are only going to worsen. Unless manufacturers are willing to pay premium rates or delay implementation, they should explore opportunities to develop their own talent internally. Note that this applies as much to traditional trades like welding as to emerging industrial automation skills. Many educational programs, like those teaching the basics of robot programming, are available online at little or no cost.
Implementing strong security measures
Manufacturers deploying Industry 4.0 technologies are well advised to pay close attention to cybersecurity, especially if using cloud services for data storage and analytics. This will require hiring or developing people with the appropriate skills and expertise, and not doing so is to invite some form of attack.
How robotics and automation will shape the future
Manufacturers the world over have little choice but to invest in advanced technologies like robotics and automation. Unlike in earlier years though, this increasingly means using AI and ML to analyze data, identify patterns and trends and support physical automation hardware.
Success will depend on deploying technology where it can have maximum benefit, which means taking a careful look at opportunities and options. As noted previously, manufacturing simulation is a powerful tool for supporting this effort. Rather than relegate people to the role of machine minders, it will be important to integrate them into the system of hardware and software automation.
This expansion of Industry 4.0 thinking may be new to some readers; others will already be questioning the role of human workers in the factory of the future. For both constituencies, we recommend our eBook on the subject of Industry 5.0. Download your copy today.
Further reading
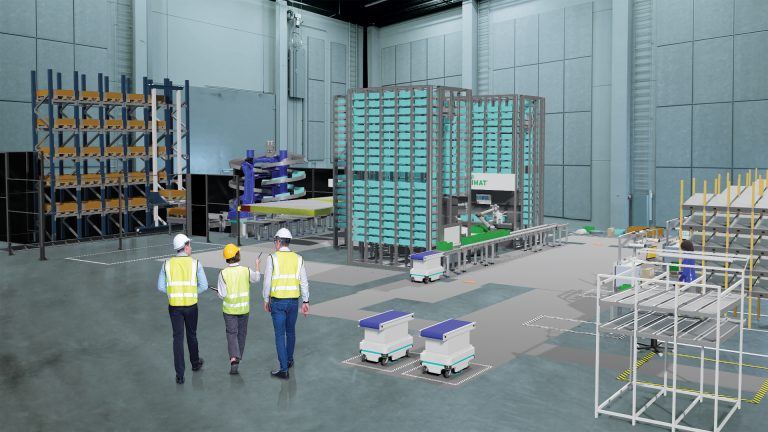
The future of automated manufacturing (and why humans still matter)
Automation in manufacturing has been evolving for decades, but its true impact isn’t in replacing people, it’s about making them more capable. We spoke with Mika Anttila, one of Visual...
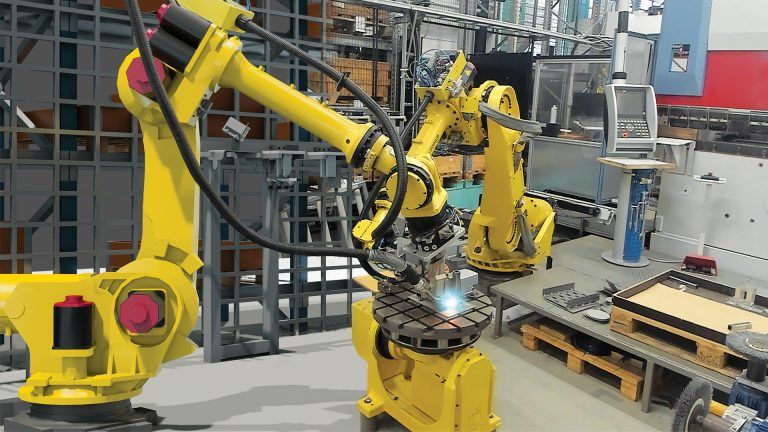
Understanding digital twins in manufacturing
Digital twins go far beyond static models or simulations. They bridge the gap between virtual and physical systems, offering real-time insights and control. But with so many definitions floating around,...
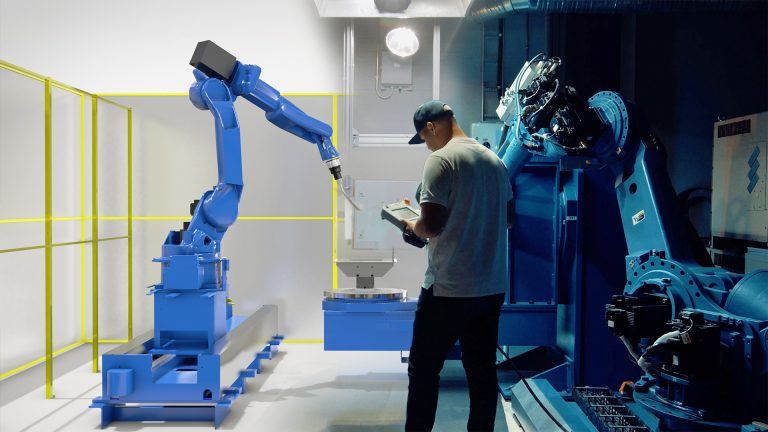
Tackling the manufacturing skills shortage with simulation and robot offline programming
The manufacturing industry is grappling with a significant skills shortage, exacerbated by the pandemic and an aging workforce. According to The Manufacturing Institute, 78% of companies are concerned about this...