Packaging perfection: navigating variations in furniture packaging with Visual Components
The furniture industry has shifted from handcrafted pieces to mass-produced, self-assembly models made from materials like MDF or chipboard. This change has complicated packaging due to the need for high-volume production and diverse product sizes. When a client asked Wächter Packautomatik to efficiently package various furniture at high speeds, the company used Visual Components to demonstrate and streamline their solutions.
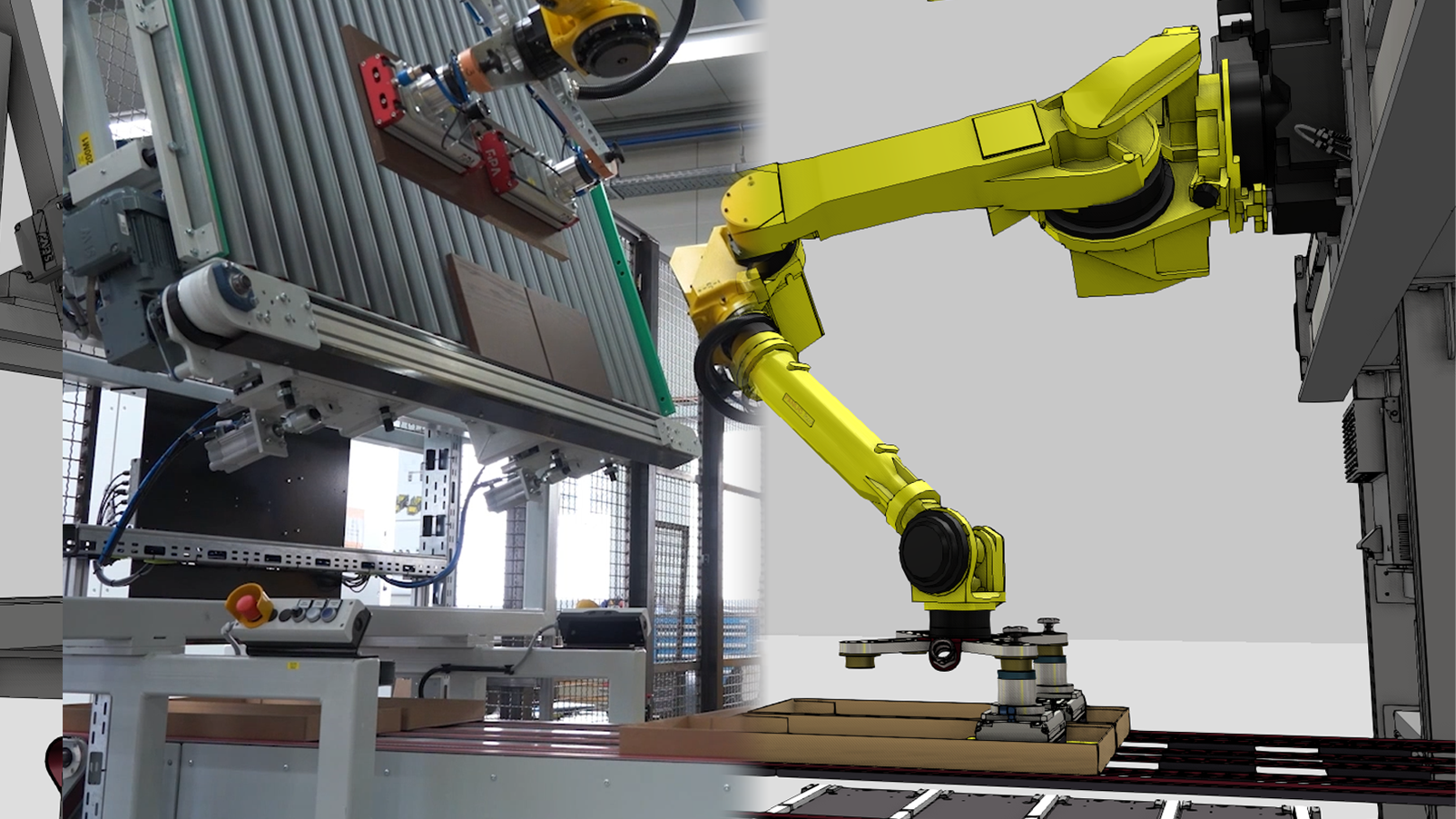
The challenge of high production numbers and product variants
In modern furniture production, where very large quantities are manufactured, the efficiency of packaging systems at the end of the production line is crucial. A prime example of such capability is demonstrated by Wächter Packautomatik, a specialist in this area. Their advanced packaging system is not only adept at handling high volumes, with the capacity to package about 20 cabinets per minute, but it also showcases remarkable versatility.
Given the diverse range of furniture variants, the packaging process must transcend individual formats to encompass all cabinet sizes, from the smallest to the largest. And the lines must not only pack the cabinets, but they must also perform the folding and closing of the cartons and the palletizing of the finished packages.
In addition, packaging lines need to take up as little space as possible. The systems must operate with maximum automation, both during operation and when changing formats. And finally, they must be planned to be fail-safe and equipped with redundant process options.
A flexible packaging solution using 15 industrial robots
An international furniture manufacturer offering furniture for self-assembly at home asked Wächter Packautomatik for a solution to pack large production volumes of furniture. A team from sales, mechanical and electrical design, and automation at Wächter Packautomatik offered a packaging solution using industrial robots because they knew from experience that only robots provide the necessary flexibility and high availability.
The team developed a concept consisting of 15 robots divided into 7 individual cells. The packaging line is supplemented by two carton folders at the start, which fold a tray from a flat carton blank, and two lidding machines at the end of the line, which seal the filled cartons. The finished product is then stacked on pallets.
A packaging cell with two robots was first set up as a prototype to test the processes and functions in real life. After this prototype passed all tests and fully met the customer’s expectations, the planning of the entire line was started based on the experience gained.
A digital test is faster than a physical test
A particular challenge in this project was the large variety of product variations. If all variants had been tested using the real robot cell, it would have been very tedious and time-consuming. Therefore, a solution for factory planning and simulation was required, which would allow the modeling and analysis of a digital twin of the packaging plant. A digital twin behaves like a real plant; it can save a lot of time and costs in development, optimization, and commissioning.
Wladimir Krieger, Robotics Engineer, working in the automation department at Wächter Packautomatik and being responsible for the software-related commissioning and optimization of machines and robots, chose Visual Components.
How the cabinets get into the cartons
The cabinets to be packed, consisting of walls, doors, and shelves, are stacked on pallets and fed to the robotic cells from two sides via a complex, fully automated conveyor system. The pallet positions are located on the left and right of the packaging line. Two robots remove the required number of products and place them on an alignment table above the cartons. Then they are picked up by another robot and inserted into the folded cardboard case.
With this setup and two cardboard cases filled side by side in parallel, the system can pack 20 boxes per minute, from small shelves to large cabinets. One side of the packaging module can be prepared for the following format without interrupting the ongoing packaging process on the opposite side. Format changes as well as filming, labeling, and removal of the remaining parts can thus be done without time pressure.
Visual Components facilitated a very high level of automation
Wladimir Krieger from Wächter Packautomatik describes the reasons why he finds this project so outstanding:
Our packaging plant achieves a level of flexibility and automation that has never been seen before on the market. Visual Components’ software simplified the feasibility analysis and accelerated the modeling processes. Thanks to modeling, we were able to try out numerous settings directly on the digital model. And as a sort of bonus, we were able to train the operators even before the real plant was completed, which accelerated commissioning.
Wladimir Krieger, Robotics Engineer, Wächter Packautomatik
Due to the large number of variants and the high throughput with the corresponding short cycle time, Wächter Packautomatik had to develop a new type of concept for the packaging machine. Visual Components was initially used to communicate and explain the new concept to the customer. Later, in parallel with first prototypes, Visual Components made it possible to reliably plan material flow, robot movements, and cycle times with very little effort.
Convincing results – for Wächter Packautomatik and their customer
For Wächter Packautomatik and its customers, the digital twin built with Visual Components is of great benefit, because the individual processes and their interrelationships can be very easily clarified and presented understandably. With just a few mouse clicks, the product to be packaged, and the corresponding robot cell can be switched to another variant. This saves a lot of time when testing, optimizing, and demonstrating the individual packaging processes, and the digital twin also saves valuable resources.
Wladimir Krieger from Wächter Packautomatik emphasizes the advantages of the digital twin:
Unlike with previous projects, the processes no longer had to be tested at the physical system. Instead, even the most complex processes were displayed reliably and quickly in digital form. We also simulated the machine settings for the different formats with Visual Components.
Wladimir Krieger, Robotics Engineer, Wächter Packautomatik
Mr. Krieger is also responsible for on-site customer training: “Another advantage is the training of the operating personnel on the digital model. The machine operators knew the settings of the system at an early stage and could start directly. This was possible thanks to the model in Visual Components.”
Wächter Packautomatik will continue using Visual Components as an important tool in the areas of process planning, validation and visualization. Due to the growing demands of the market, packaging plants will become even more complex in the future. Visual Components will make it much easier to map this complexity in engineering and present it to customers.
About Wächter Packautomatik
Wächter Packautomatik manufactures packaging machines for the food, flooring, and furniture industries and numerous special solutions in Bad Wünnenberg-Haaren, North Rhine-Westphalia, Germany.
Mr. Krieger works in the automation department at Wächter Packautomatik and is responsible for the software-related commissioning and optimization of machines and robots as well as customer training. He also provides internal support for quotations, feasibility studies, and project planning of robot systems.
About Visual Components
Founded by a team of simulation experts and amassing over 20 years in business, Visual Components is one of the pioneers of the 3D manufacturing simulation industry. The organization is a trusted technology partner to a number of leading brands, offering machine builders, system integrators, and manufacturers a simple, quick, and cost-effective solution to design and simulate production processes and offline robot programming (OLP) technology for fast, accurate, and error-free programming of industrial robots.
Want to learn more about the benefits of our solutions for your business? Contact us today!
Further reading
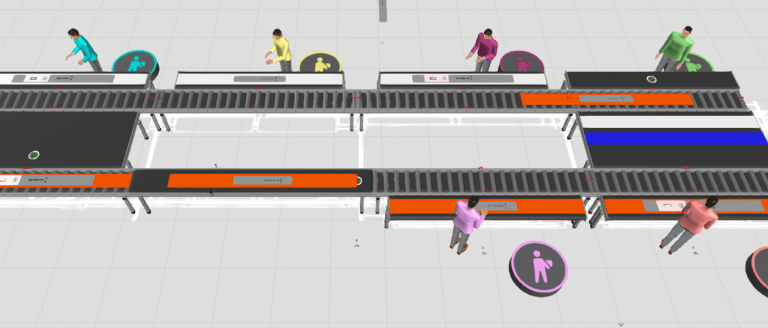
Elevating assembly planning for elevator button panels at KONE with 3D simulation
Planning a new assembly line for two product variants, KONE’s Northern Italy site needed to ensure smooth flow and minimal risk of defects. With Visual Components, they simulated and tested...
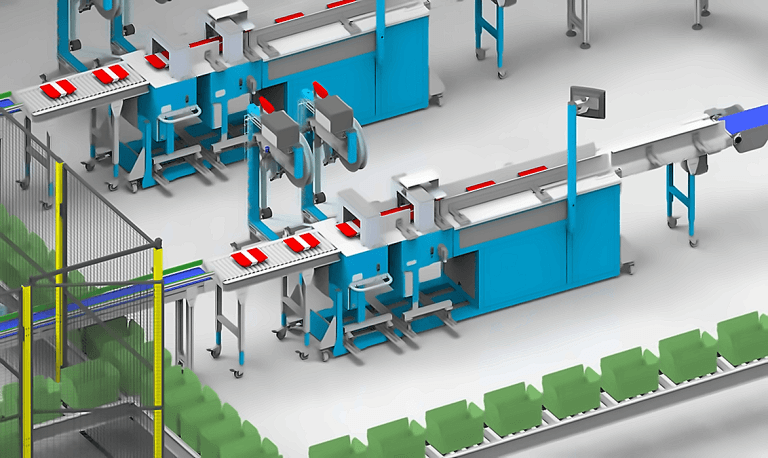
How Hollander Techniek designed an automated custom meal packaging system with Visual Components
When Uitgekookt set out to automate its meal packaging process, they needed a system that could handle custom orders with speed and precision. Hollander Techniek used Visual Components to design...
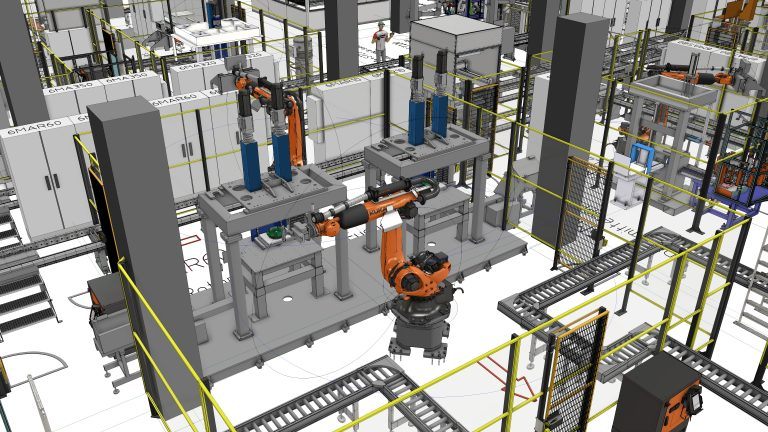
How EMIL SCHMID MASCHINENBAU designed a high-speed battery assembly plant with Visual Components
Facing the challenge of designing a fully automated battery assembly plant for a customer, EMIL SCHMID MASCHINENBAU turned to Visual Components. With 3D simulation and an extensive library of factory...