Production reshoring in 2023: the reasons, challenges, and opportunities
Production Reshoring is a continuing upward trend in the manufacturing industry. Even though it may seem an appealing strategy for some countries, it does come with added costs and challenges. At the same time, it also opens opportunities for improvement if the right technology is used for planning and execution.
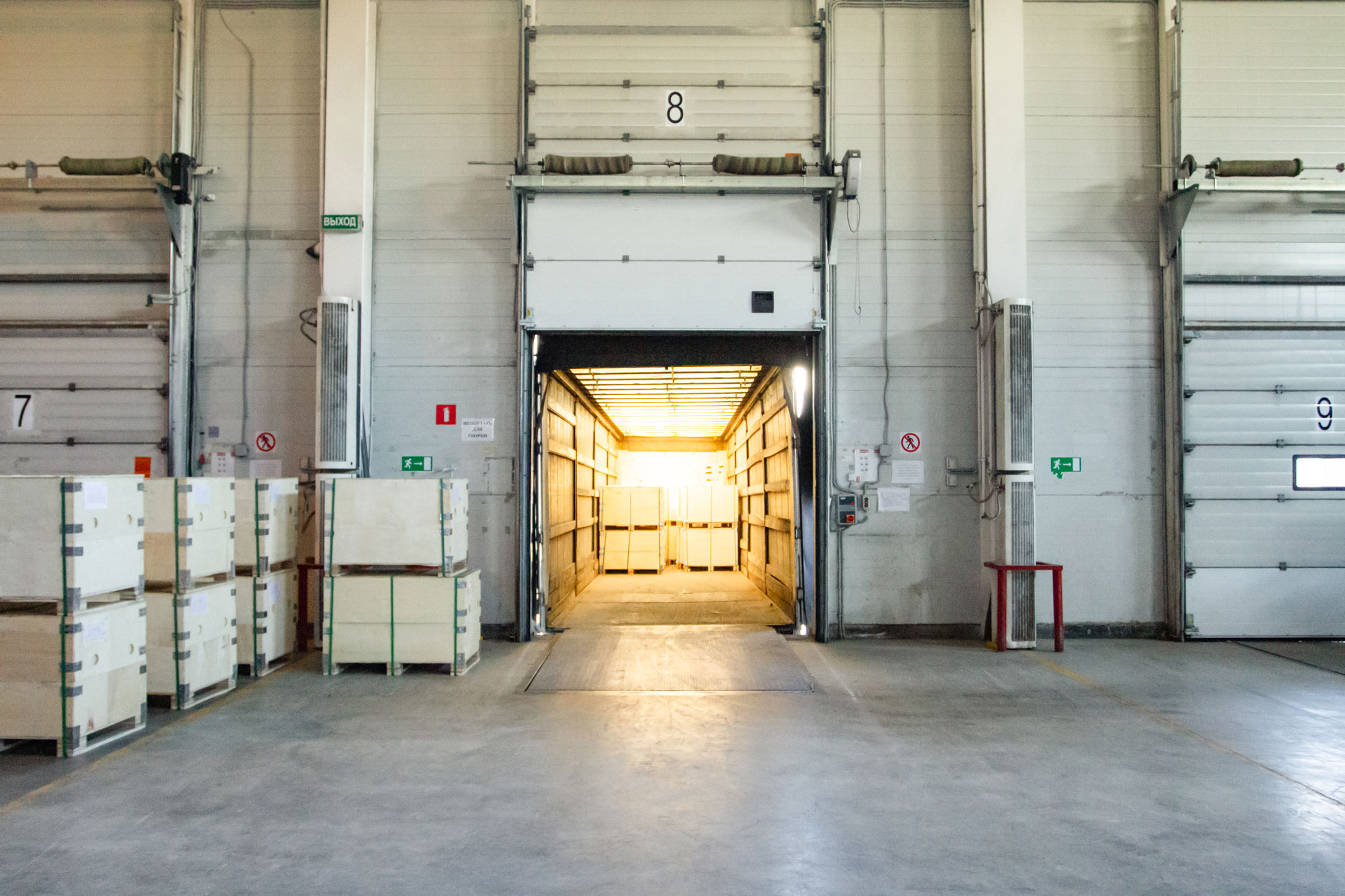
Offshoring – moving manufacturing to lower-cost countries – has lost its luster. Once seen as a way of building a stronger competitive position, today it seems to be a vulnerability and a constraint. The result is growing interest in reshoring, and manufacturing simulation is playing a central role in helping manufacturers do that successfully. Here’s why there’s growing interest in reshoring, and why simulation should be part of the activity.
What’s driving reshoring?
Three separate yet linked factors are motivating manufacturers to move production closer to home: costs, supply chain constraints, and Environmental, Social, and Governance (ESG) concerns.
Considering costs first, the equation has changed dramatically in recent years. Labor is becoming more expensive in Asia and elsewhere, resulting in smaller savings. In many regions, labor turnover is higher than expected, with the resulting churn driving up training expenses and quality costs. What’s more, experience shows that maintaining expected quality standards takes more time and effort than was anticipated, and warranty costs can be higher.
The pandemic and chip shortage shone a spotlight on supply chain issues, although challenges had been surfacing for some time. Extended lead times create a lack of flexibility, which is a growing problem in many industries, especially given consumers increased desire for personalization.
Consumers are also taking more interest in sustainability and the social costs of producing the goods they buy. With substantial CO2 emissions, shipping is hardly a “green” activity. Plus, there are rising concerns about production methods, environmental damage where minerals are extracted and processed, and employment practices.
In the US, ThomasNet found a strong interest in reshoring production. Close to two-thirds of manufacturers surveyed in 2020 reported they were considering reshoring as a response to Covid-19 and two-thirds of those cited the impact of supply chain disruptions as a factor. In parallel, a 2021 survey by the Reshoring Initiative found reshoring activity jumped 17.6% between 2019 and 2020.
Every business and industry faces different challenges. Those who source from overseas, however, are facing challenges that should prompt them to explore the feasibility of manufacturing domestically.
The opportunity within reshoring
If reshoring is a way to address cost and consumer concerns regarding where and how products are manufactured, surely, it’s also an opportunity to implement processes to resolve them. Rather than recreating an existing operation, why not re-imagine how things are done and find innovative ways to meet cost, quality, sustainability, and personalization goals?
To be sure, with any change there’s a risk of underachievement or even failure. This usually stems from overlooking aspects of the project, underestimating the work involved, or not taking the time to explore alternatives thoroughly. (And sometimes all three!)
What’s needed is a tool for maximizing ROI from a reshoring initiative. That tool is manufacturing simulation.
Build a virtual operation or factory
Visual Components 3D manufacturing simulation software is a tool for building digital replicas of existing or proposed manufacturing operations. Once constructed, the model executes production schedules as they would run in the physical world (which is one technique for validating model accuracy.) The model can then be used to run what-if scenarios. These can take any form of interest, such as dealing with a machine breakdown, exploring the impact of new product variants, or evaluating possible responses to shifts in customer demand.
Manufacturing simulation is a powerful tool for gaining deeper insights into workflows within a factory. It highlights bottlenecks and helps explore ways of improving throughput, reducing transport distances, or balancing lines.
When planning a new facility, simulation is a tool for ensuring every option is explored and ROI is maximized. Used as a virtual sandbox, it reduces risk while letting the manufacturing engineering team explore innovative ideas that might otherwise not receive proper consideration. Here is an example of how manufacturing simulation can be used as an opportunity to identify the most optimal investments in a production system.
Visualize the digital twin for improvements
Establishing communication links between a simulation and the physical factory turns the model into a digital twin. Data transfer ensures the model duplicates reality, with equipment in the model running at the same speeds, suffering the same downtime, and achieving the same yields as that out on the factory floor bringing the inefficiencies into the spotlight. This makes it an even more powerful tool for improving understanding of what’s happening now and exploring improvement ideas.
Companies that are re-shoring can use digital twins to lock in sustainability and efficiency gains. They do this by experimenting with production flows and assessing the impact of new technologies like autonomous mobile robots in packaging and warehousing areas, all within the same model.
The sustainability challenge
For manufacturers, sustainability means getting more from less, and simulation can help with meeting customer expectations and conforming to regulatory requirements. It can help identify and then address resource-intensive operations and reduce waste throughout the production process. Focus areas could include the re-use of raw materials, forklift, and AGV movements, reducing equipment downtime and associated impacts, and reducing spending on production planning and plan execution.
Simulation helps find opportunities and reduces risk in reshoring
Given current political and economic realities, reshoring seems set to continue for the foreseeable future. Companies looking at bringing production back to their countries of origin like the US must however be aware of the complexity of the process and how long it can take.
Manufacturing simulation and Offline Robot Programming are powerful solutions for analyzing production processes and exploring improvements in a risk-free way. Used as part of a re-shoring project, these solutions will smooth the transition to localized production while providing tangible benefits in terms of sustainability, agility, and cost optimization. They also help with avoiding delays and compressing the project timescale.
To learn more about simulation and offline robot programming and what it could do for your manufacturing business, contact Visual Components to arrange a discussion.
Further reading
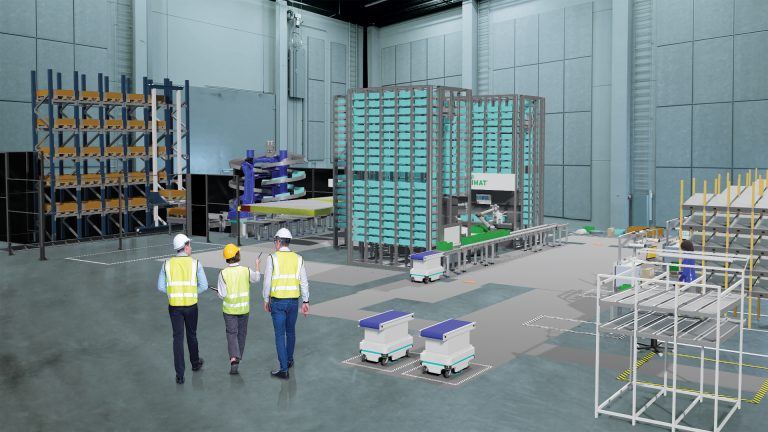
The future of automated manufacturing (and why humans still matter)
Automation in manufacturing has been evolving for decades, but its true impact isn’t in replacing people, it’s about making them more capable. We spoke with Mika Anttila, one of Visual...
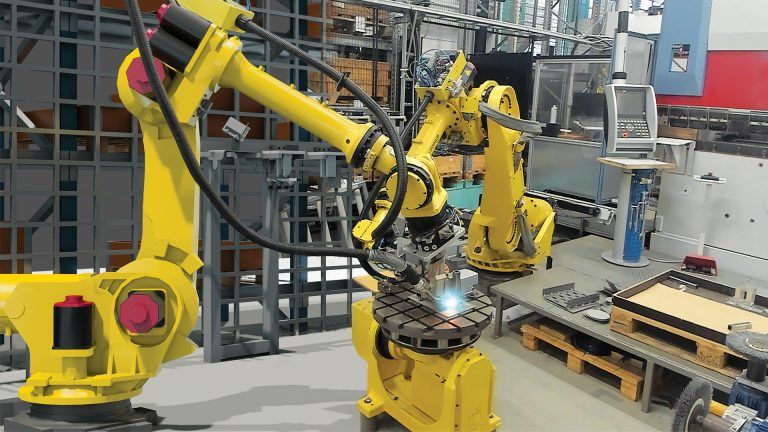
Understanding digital twins in manufacturing
Digital twins go far beyond static models or simulations. They bridge the gap between virtual and physical systems, offering real-time insights and control. But with so many definitions floating around,...
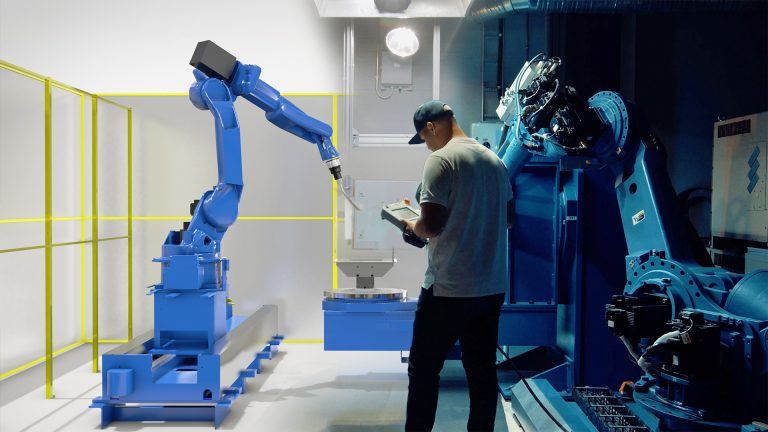
Tackling the manufacturing skills shortage with simulation and robot offline programming
The manufacturing industry is grappling with a significant skills shortage, exacerbated by the pandemic and an aging workforce. According to The Manufacturing Institute, 78% of companies are concerned about this...