How Technology Can Help Pharmaceutical Packaging Design
Whether your product is sold on shelves or direct to consumers, packaging design is a big deal. It promotes your product, tells the customers what to expect, and sets you apart from your competitors. Some customers will buy a product just because of the design of the packaging.
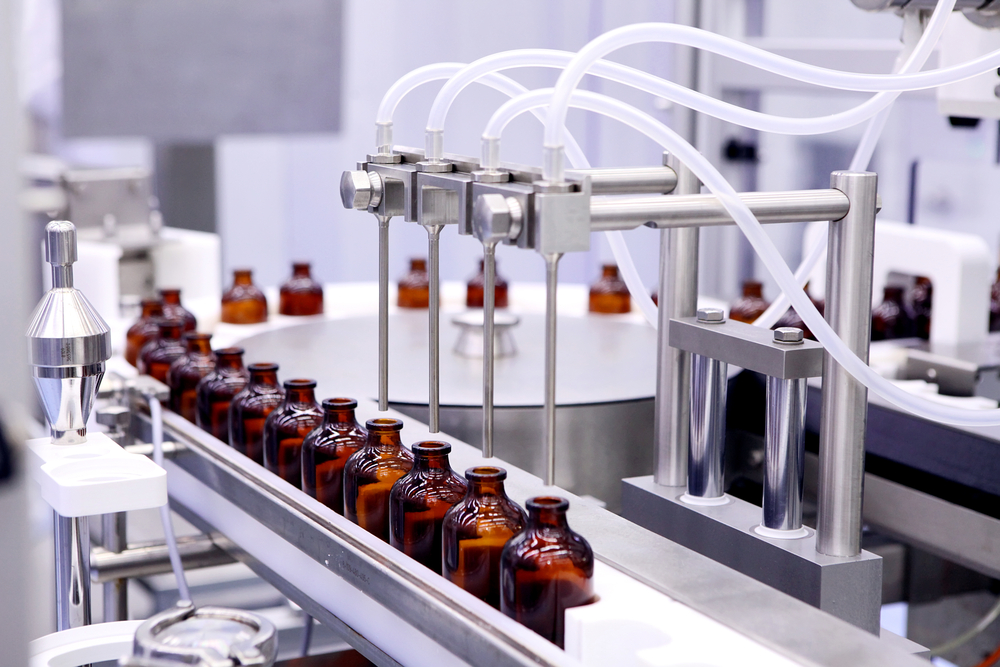
With pharmaceutical packaging specifically, there are some added challenges. There are strict regulations about how the packaging can be presented, making this industry more difficult than others.
The packaging needs to protect the medicine, allow the batch to be traced, offer a child-resistant opening, and do so repeatably. Any quality issues in the packaging could lead to heft fines and massive slowdowns to your operation.
Besides the physical constraints, there’s also a lot of text that needs to be included. A customer needs to understand all the risks, how to take the medicine, and the ingredients. There are even regulations that dictate what kind of adhesives can be used to attach the labels to the container. Whether you manufacture at high volumes or you run small batches, you need to understand the importance of effective pharmaceutical packaging design. More specifically, you should understand how precise manufacturing will help you achieve your goals.
Aiming for sustainability in drug packaging
Although the points we discussed earlier are very important for drug packaging, you don’t need to overlook sustainability. This word refers to using eco-friendly materials and processes, but it also describes a process that saves manufacturers money.
A sustainable plant will waste fewer hours, scrap less material, and create a greener product.
In our recent survey, 26% of manufacturers are motivated to build a new factory or upgrade existing facilities to improve their sustainability practices. This could mean that your competitors are moving towards a more streamlined process.
How is it achieved? The first consideration is where and how you source your raw materials. Swapping to partially recycled (or reclaimed) plastics will typically save you money and create a more sustainable product. Changing your floorplan and equipment layout will also minimize the time and energy spent creating packaging.
A report found that pharma companies create 55% more greenhouse gases than the automotive industry as a whole.
Another way is through reworking your process flow. Perhaps there’s a way to change your process and increase your yield, subsequently decreasing your waste.
Using technology to assist in pharmaceutical packaging
When it comes to sustainability, technology can play a pivotal role. Think back to how injection molders changed the whole industry. Today, we are seeing similar strides on smaller scales.
The equipment on your floor definitely uses a lot of advanced technology. It’s commonplace for pharma packaging plants to have programmed robotics and conveyors to optimize their processes.
Moreover, technology is becoming smarter, more flexible, and more affordable. Looking for new technology is a quick way to gain an advantage over your competitors.
Manufacturing mistakes can be costly
Pharmaceutical packaging plants rely on quick process times and high yields. You might be making millions of units a year and can’t afford anything slowing you down.
Manufacturing mistakes are one way to devastate your operation. A UK-based study found that nearly 97% of companies interviewed made one or more mistakes in their most recent project. For some, this mistake might only mean a little bit of downtime. For others, it could mean scrapping an entire batch or day’s worth of product. 2% of the interviewed companies said their cost to correct the issue was upwards of $1 million.
Mistakes often scale with the size of the company. As your business grows, so do the potential dangers of a mishap. This becomes even more dangerous as your margins shrink. A company can easily be leveled due to an unforeseen mistake.
These mistakes are costly and need to be avoided. That can be done partially through an improved process, restructuring, and plant-level changes. It can be done more effectively through technological advances and simulation software.
How simulation software helps
Simulation software is the newest era of technology that plants across the globe are using. It entails using a 3D model and manipulating the model in a digital space before anything is physically built.
A simple example would be to create a 3D model of your newest pill bottle. The designer can look at specifications, check physical properties, and ensure the bottle will meet all the criteria. This is all done before the prototype is made.
Perhaps the designer will note some oversights or simple mistakes. They can fix the issues before the product gets created. Doing so can save an incalculable amount of money and time as your operation keeps maturing.
On a grander scale, your entire warehouse can be simulated. All the equipment, interfaces, and even the lifecycle of your product can be mapped out virtually. You can simulate the raw material moving between workstations, plan operator paths, and calculate time savings.
More importantly, you can do this as much as you like and make as many changes as you’d like on the screen. A lot of companies will use a simulation to evaluate different layouts before finding the one that yields the most sustainable results.
If you were to do the same process physically, you could be wasting years and millions of dollars. It wouldn’t make sense to keep rearranging your plant until you get the best setup. With a simulated model, you can do this without touching anything in your factory.
Optimizing results with Visual Components
At Visual Components, our goal is to create simulated environments that actually help. With just one of our clients, we helped their pharmaceutical company achieve a 35% increase in efficiency for each of their two production lines.
We create fully simulated environments. Our team will include robotics, controllers, material flow, virtual reality, and complete visualization in a single model. With over 2,600 ready-made components in our digital library, we can expedite a lot of the upfront work.
We will ensure the simulated environment matches your plant perfectly and includes all the parameters needed for success. In addition, we will do the simulation in-house and prove out any concepts you’re working on.
As you know, there’s a lot of science that goes into packaging. We will help you meet the stringent requirements of this industry while improving your efficiency and sustainability.
Our team at Visual Components has specific expertise in the world of pharmaceutical packaging design. We understand a lot of the constraints and will help you optimize your facility in order to get the best results and take a larger market share.
Further reading
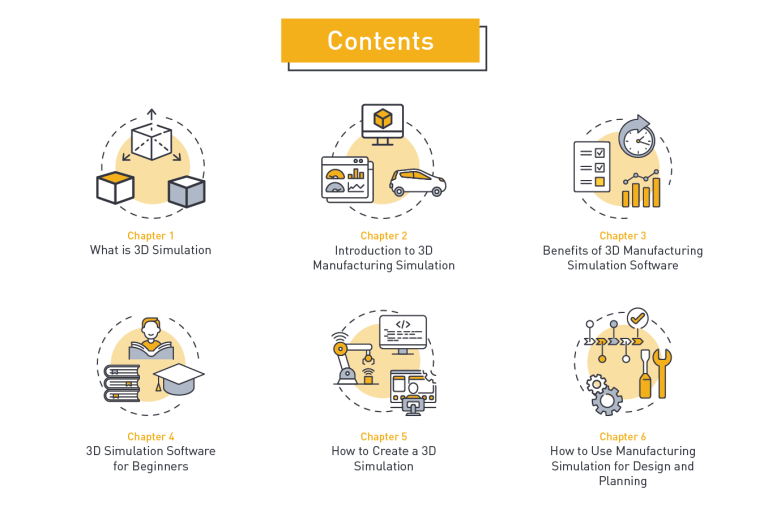
3D Manufacturing Simulation Software: The Ultimate Guide (Videos Included)
This is your complete guide to 3D manufacturing simulation. Find how to get started with 3D simulation, the biggest benefits of simulation, how to ramp up your skills and much...
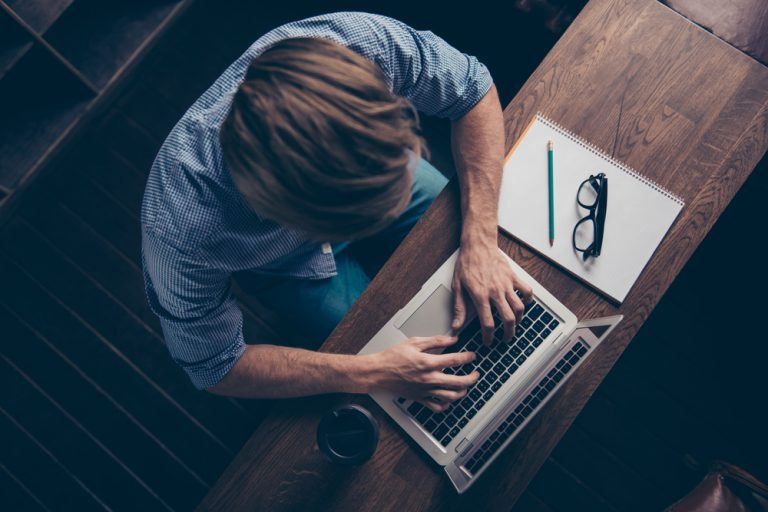
Robert’s Path to Working Life After Learning Visual Components at the University
Learning simulation software can help you become more competitive in your job search once you graduate. Here's how learning Visual Components helped Robert land a job.
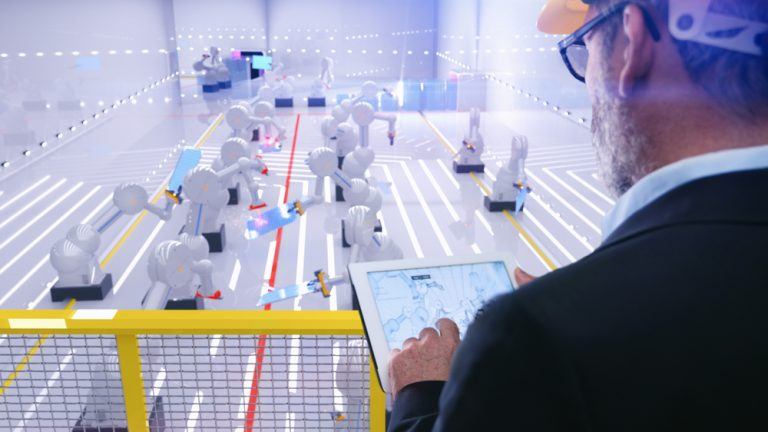
Robot Simulation Software: Everything You Need to Know
How is robot simulation software used to program robots virtually? What are the top 7 reasons to use robot simulation software? Find the all the answers and learn more in...