Digital Twins and Virtual Commissioning in the Manufacturing Industry (Updated for 2023)
In this article, we’ll highlight some of the terms and technologies we often get asked about, their applications, and why we think they’re important.
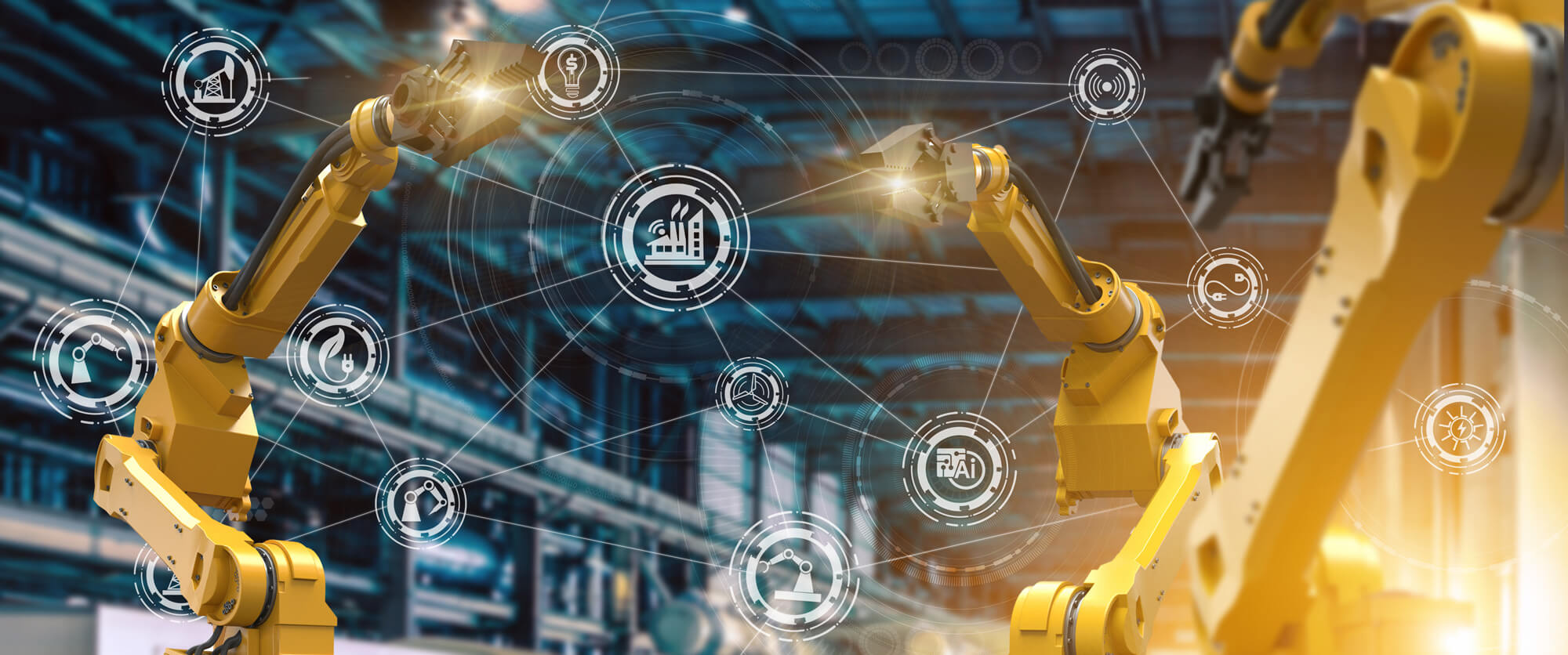
To drive down costs, improve quality and develop sophisticated new products, manufacturers are investing in ever more complex automation. As a tool for improving the reliability of this equipment and enhancing process control, they also want to take advantage of Industry 4.0 technologies like IoT sensors and digital twins.
For the companies that build and integrate this automation, the challenge is a little different. Their goal is to pass the final acceptance tests as quickly as possible, delivering advanced automation that generates the highest possible ROI for their clients. Virtual commissioning provides a way of doing this.
What’s the connection between a digital twin and virtual commissioning? There’s a clear overlap in that both entail building complex simulations of physical systems. There are also some differences, and it’s feasible, although perhaps not desirable, to have one without the other. This article takes a dive into the overlaps and differences to help readers understand which they should prioritize.
Recapping Industry 4.0
The phrase has been in use for some years but a brief recap will set the scene for a discussion of digital twins and virtual commissioning.
Industry 4.0, the fourth industrial revolution, refers to the emergence of cyber-physical systems to bring about a step-change in manufacturing capabilities akin to the earlier revolutions of steam, electricity, and computerization.
In practical terms, Industry 4.0 is about combining advanced sensor technologies with internet connectivity and artificial intelligence to create “smart” manufacturing systems. These are machines, processes, cells and lines that can report on their condition, react to trends and optimize their performance with minimal human intervention, or even none at all.
The complexity of these Industry 4.0 systems means new processes are needed to facilitate their implementation and oversee their operation. Two of these processes are the digital twin and virtual commissioning.
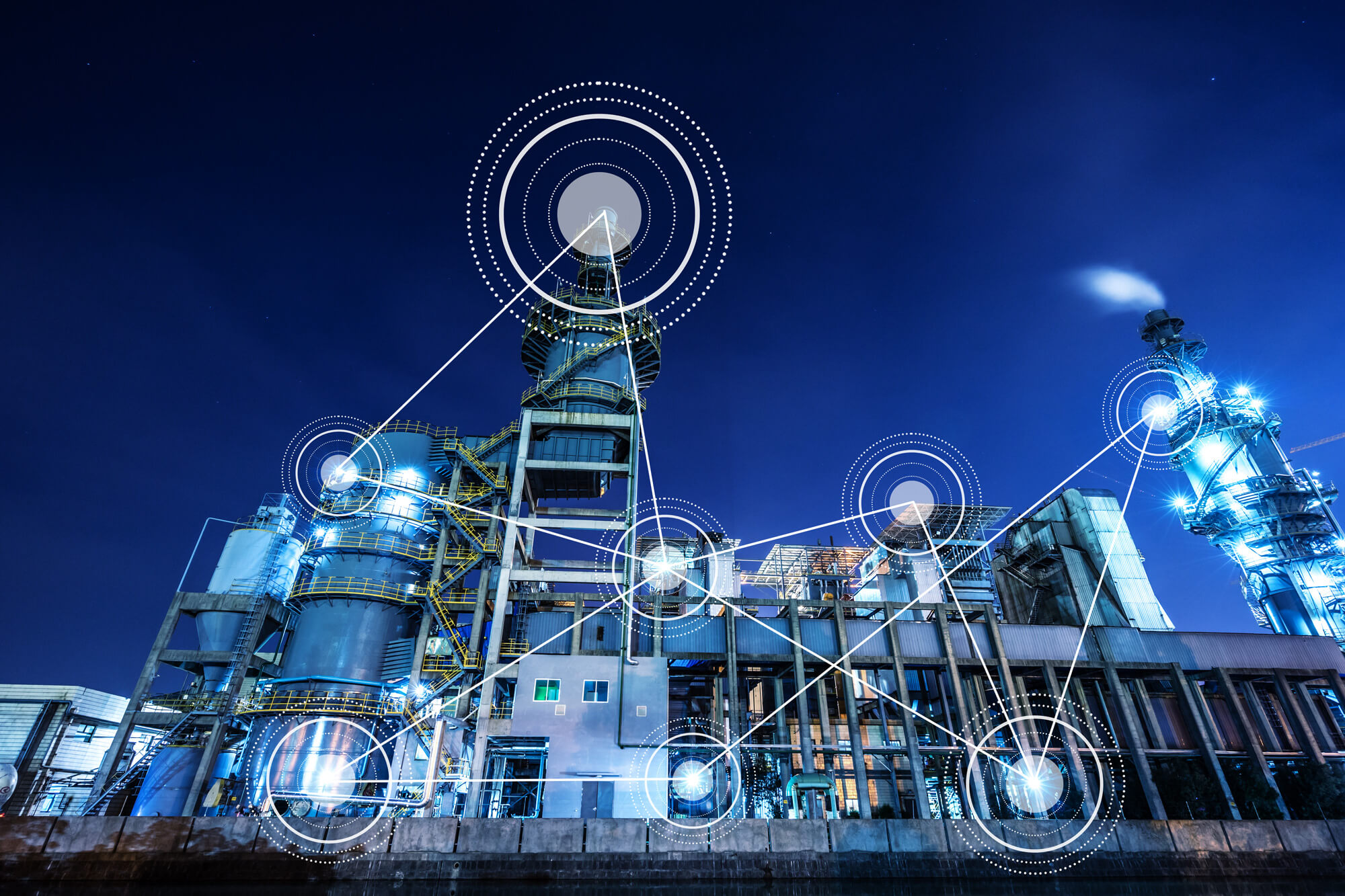
What is a Digital Twin?
A simple answer is that it’s a virtual recreation of a physical system. It’s a computer model that looks, acts, and behaves just like the physical system it replicates. Furthermore, there can be a connection between the two for an exchange of data so the virtual system can synchronize with the real system.
Many of the early digital twins were pioneered in the product as opposed to the manufacturing realm. Turbine engines, nuclear power plants, and wind turbines are three examples of products that can have digital twins.
A digital twin is far more than just a CAD model, although that’s usually the starting point. It must also include some form of multi-physics simulation that lets it function just like the real system. This will include replicating speeds, loads, temperatures, pressures, inertia, and even the external forces acting on the system.
In manufacturing a digital twin can replicate an individual machine, a cell, a complete line, or even, as Time reports in “How Digital Twins Are Transforming Manufacturing, Medicine and More”, a complete factory, which is something BMW is doing. Examples of how a digital twin might be used at the machine level include:
- Evaluating spindle performance
- Monitoring thermal changes
- Simulating loading and unloading
Cells using multiple robots are developed with sophisticated CAD models and robot simulation software. Some people might consider these digital twins although a truly twinned cell would have an extensive array of sensors and instrumentation, plus a way of exchanging data with the virtual replica.
Other areas where digital twins offer major benefits are packaging and warehousing. These complex operations often incorporate conveyors and increasingly, mobile autonomous robots with sinuous material flows and multiple storages and kitting locations. A digital twin of such an operation can help with identifying and evaluating improvements in flow and handling to increase velocity and reduce costs.
Once validated against the real system, applications of the digital twin can include:
- Service life and maintenance predictions
- Operator and maintenance training
- Evaluating possible new operating scenarios
- Replaying past events as a way of understanding what went wrong
Notably, in all these activities the digital twin avoids the need to take the machine or system out of service. Instead, it can continue running and/or producing while they take place in parallel.
Commissioning Complex Manufacturing Equipment
Every major manufacturing equipment project includes a step called “Commissioning.” Another important step is Factory Acceptance Test (FAT) where performance to specification is demonstrated. FAT can be included in commissioning, or commissioning may start after FAT. It’s often where operator and maintenance technician training begins, and it’s also the part of the project that gives machine builders and automation integrators the most heartache.
The problem is, commissioning is where the control systems are linked to the mechanical systems. This involves complex sequences of signals that must flow logically and meet strict timing requirements. Almost inevitably, it takes time to resolve the problems that arise in making these systems “talk” to one another, and this leads to project delays.
Furthermore, training itself can take longer than expected and can surface previously hidden problems that must be resolved before the FAT. The result: more delays.
Understanding Virtual Commissioning
A paper published in the July 2014 “Journal of Computational Design and Engineering” is thought to have the first reference to virtual commissioning. “Survey on the virtual commissioning of manufacturing systems” reviewed the then state-of-the-art in “the physical model construction of a virtual device, and the logical model construction of a virtual device” and recommended the direction further research should take.
In the years since that paper was published, the meaning of “Virtual Commissioning” has become better understood. Today it’s seen as simulating the control logic and signals that will enable a specific piece of automation to work in order to replicate operation and so complete the system controls.
An advantage of virtual over physical commissioning is that it can begin earlier in the project as it doesn’t need the mechanical system. It does however require that all the operating logic be understood, including cycle times, part rates, feeds, gripper operation, speeds and loading and unloading. It also requires a simulation of the control logic, including all the PLC signals with their timing and sensor and actuator responses. Given these prerequisites though, virtual commissioning is entirely feasible.
Benefits of Virtual Commissioning
Virtual commissioning is of great interest to machine builders and integrators because it can dramatically shorten the overall project. Rather than following on from physical build, it can start while construction is underway. Making commissioning a parallel rather than a series activity saves time between build and FAT, benefiting client and integrator alike.
Virtual commissioning also reduces risk, both technical and project. Problems in system logic or timing are discovered earlier. Changes can often be made quickly with minimal impact on project duration.
An earlier start on training is another benefit. Operators and maintenance personnel can begin receiving instruction before the system is physically complete. This brings forward the date at which the new line or machinery can “go live”.
Virtual Commissioning, Digital Twins and the IoT
This article has sought to clarify the areas of overlap and the differences between virtual commissioning and digital twins. Both use virtual representations of physical systems to save time, enable better training, and identify improvement opportunities, among other benefits. However, the digital twin requires a physical equivalent with IoT technology for data transfer. Virtual commissioning does not.
Another way to look at this is that the use cases are different. In manufacturing a digital twin is a tool for monitoring, predicting, and improving the performance of an existing system. Thus it’s something to be used by manufacturers.
In contrast, virtual commissioning is of greatest value to those building and integrating complex new manufacturing equipment.
Interestingly, manufacturing simulation supports both virtual commissioning and digital twin technology. This comes about through the ability to model how workflows through a system. Such a model is a vital input to both the digital twin and the virtual commissioning exercise.
To learn more about how simulation benefits both machine builders/integrators and manufacturers, contact Visual Components.
Further reading
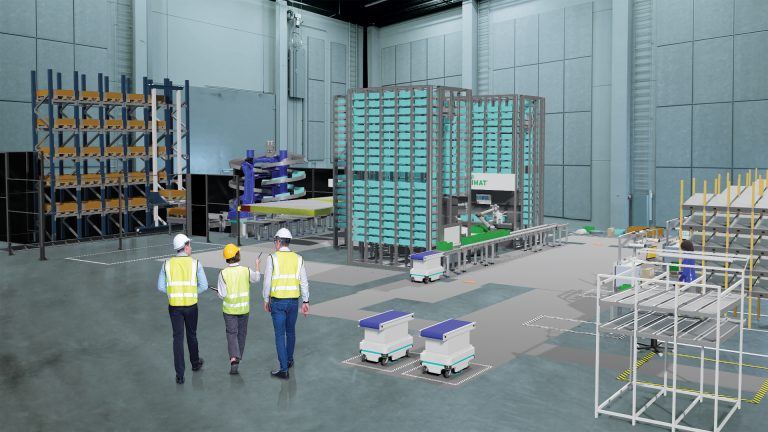
The future of automated manufacturing (and why humans still matter)
Automation in manufacturing has been evolving for decades, but its true impact isn’t in replacing people, it’s about making them more capable. We spoke with Mika Anttila, one of Visual...
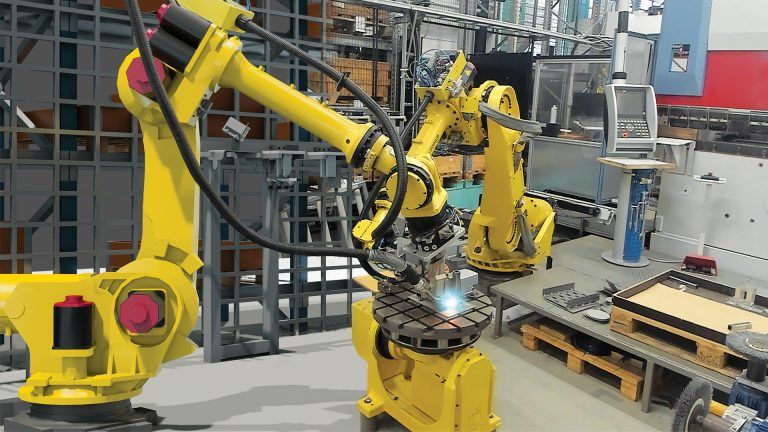
Understanding digital twins in manufacturing
Digital twins go far beyond static models or simulations. They bridge the gap between virtual and physical systems, offering real-time insights and control. But with so many definitions floating around,...
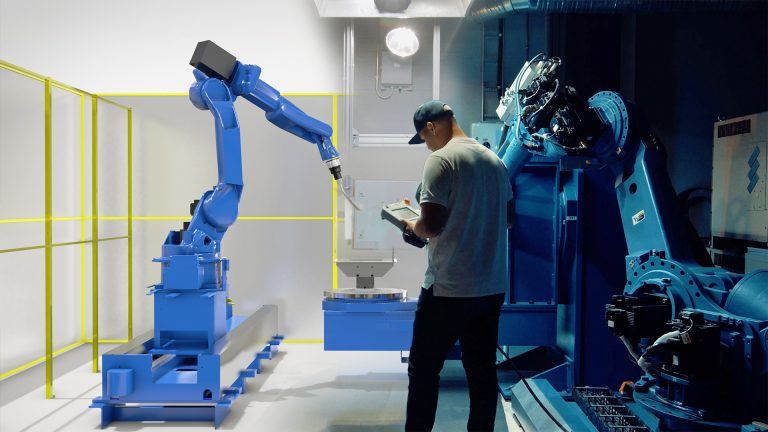
Tackling the manufacturing skills shortage with simulation and robot offline programming
The manufacturing industry is grappling with a significant skills shortage, exacerbated by the pandemic and an aging workforce. According to The Manufacturing Institute, 78% of companies are concerned about this...