Fill Case Study
See how Fill is using Visual Components 3D simulation to optimize resources and reduce costs.
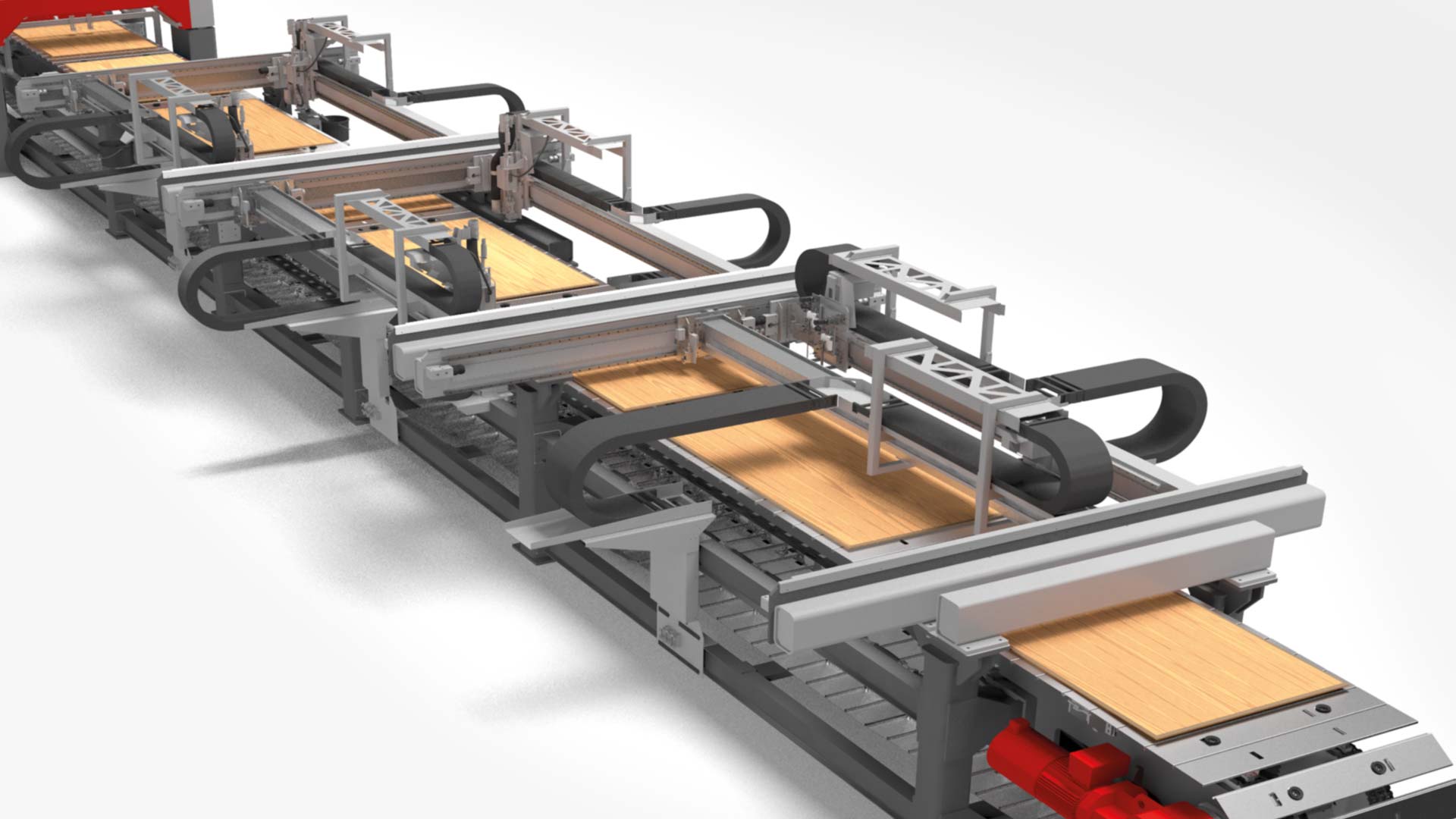
Visualization as a key selling point
Fill GmbH is a global mechanical engineering and factory construction company from Austria. Since 2009, Fill has used Visual Components’ 3D simulation software to support its sales, production planning and engineering.
Before adopting Visual Components, the company went through an extensive review of 69 different simulation tools, ultimately choosing Visual Components due to its proven track record and excellent partner support.
Our customers’ first impressions of the simulations have always been above all positive.
Alois Wiesinger, M.Sc. (Tech.), Product Developer at Fill
3D Simulation – the implementation phase
During the nine-month implementation phase the project team created the first simulations and the parallel models for a standardized component library. While standard industrial components such as conveyors and robots could be taken from Visual Components’ component library, numerous special components were modelled individually by the partner DUALIS.
Already the first 3D simulations received a great response from Fill’s customers.
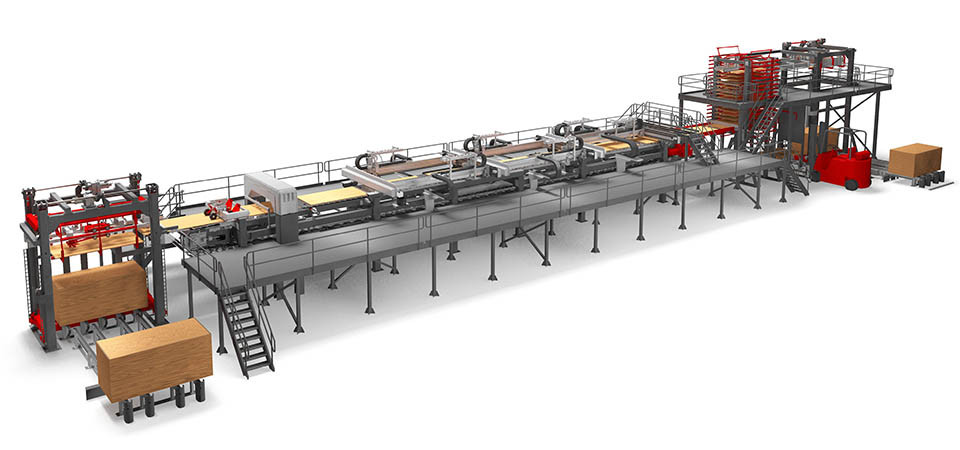
Simulation enables system optimization
Simulation benefits not only sales and marketing, but also the actual factory design. Simulation helps in optimization and especially in avoiding errors in advance.
A practical example comes from the wood processing industry. Initial calculations indicated an output of 500 planks per hour for the production line. However, the simulation showed that the output would actually be as few as 400 planks per hour as flaws in the drive reduced the feed rate.
Using simulation, the central bottleneck was identified. The project planners then optimized processes and increased the performance of some resources. In the end, an output of 500 planks per hour was achieved.
“It was only through the simulation and its realistic modelling of dynamic interactions that we were able to discover the weak points of the system at an early stage and ultimately meet the requirements to the complete satisfaction of all concerned.” says Alois Wiesinger.
As the example indicates, simulation can be an invaluable asset in reaching the goals for any production line.
It was only through the simulation and its realistic modelling of dynamic interactions that we were able to discover the weak points of the system at an early stage and ultimately meet the requirements to the complete satisfaction of all concerned.
Alois Wiesinger, M.Sc. (Tech.), Product Developer at Fill
Further reading
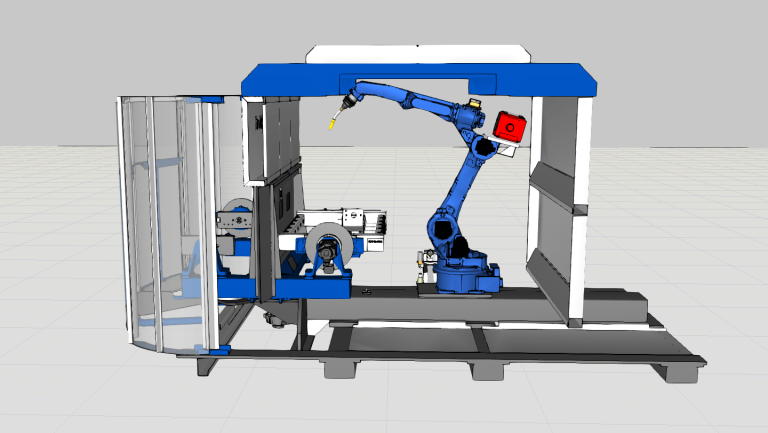
Maximizing efficiency and ROI from day 1: Duun Industrier pre-programs a welding robot cell with Visual Components OLP
Duun Industrier, a leading Norwegian heavy machinery manufacturer, installed the Nordics’ largest robotic welding station in 2013. Utilizing Visual Components for robot programming since 2014, they commissioned a new robot...
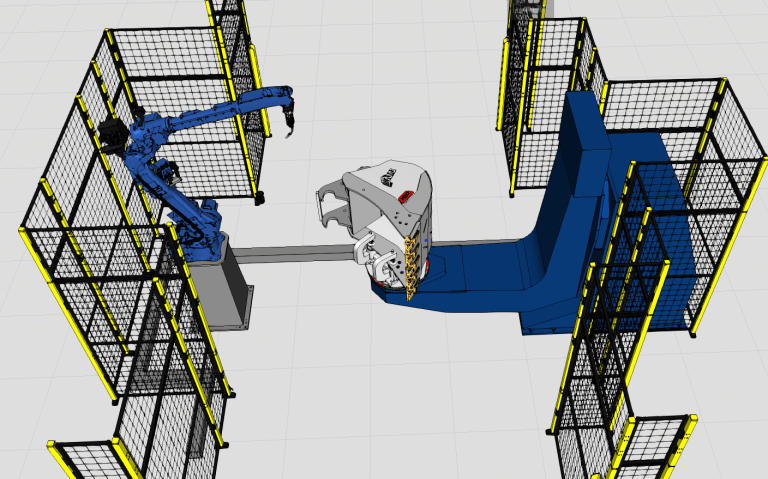
Combatting the welder shortage: how AMI Attachments enhances production efficiency with Visual Components OLP
AMI Attachments, a leading North American manufacturer of heavy equipment attachments, sought to improve product throughput and meet evolving market demands while navigating a welder shortage. By implementing Visual Components...
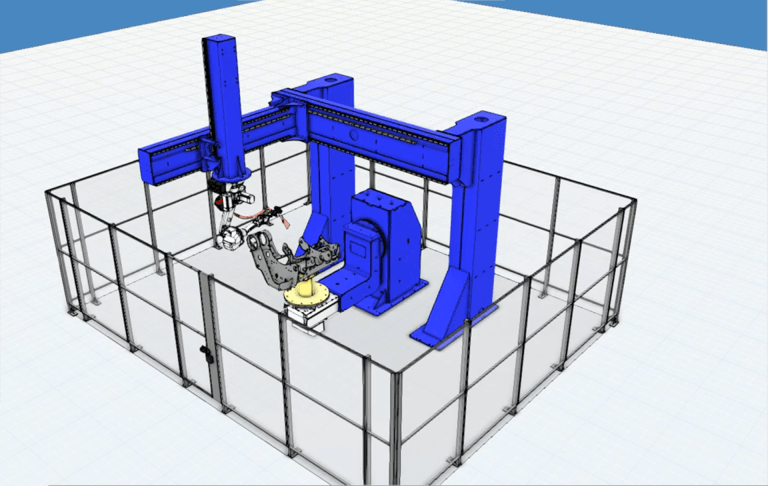
Ponsse is driving forest machine innovation and improving productivity with Visual Components Robotics OLP
Ponsse Plc., a global leader in forest machine manufacturing, has transformed its production process by leveraging Visual Components Robotics OLP.