The Simple Robotics Toolkit
In this article, we’ll review some of the key features in simple robotics and how to use them.
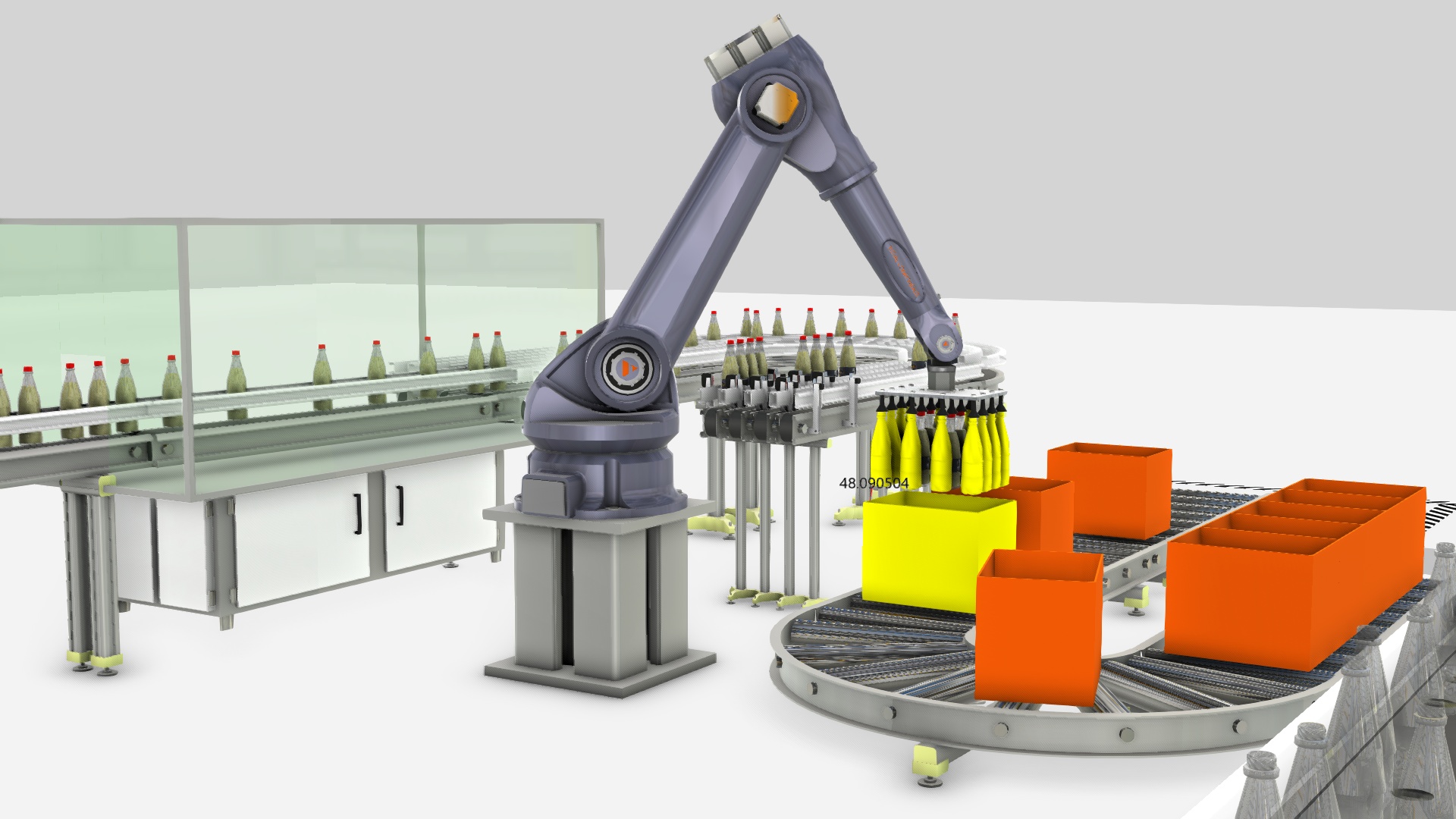
What is Simple Robotics?
“Simple Robotics” is a set of features included in all Visual Components 4.0 products. In short, these features allow users to virtually teach a robot and validate the work cell; no programming required, and no prior knowledge of robotics needed. With the Simple Robotics toolkit, it’s easy to plan, design, test, and simulate robot work cells for a variety of industrial applications. In this article, we’ll review some of the key features in Simple Robotics and how to use them.
Key features in the Simple Robotics toolkit
The Simple Robotics toolkit includes features that allow users to intuitively teach tasks to a robot and validate the design of the robot work cell. Here’s a short overview of the main features:
- Jogging allows users to interact with a robot, meaning the robot can be moved, guided, and controlled in the 3D world. This allows you to see how far the robot can reach and how the robot joints move. Users can move the robot by jogging individual joints or translating and rotating the robot in different coordinate systems, including robot tool coordinates, world coordinates, and part coordinate systems
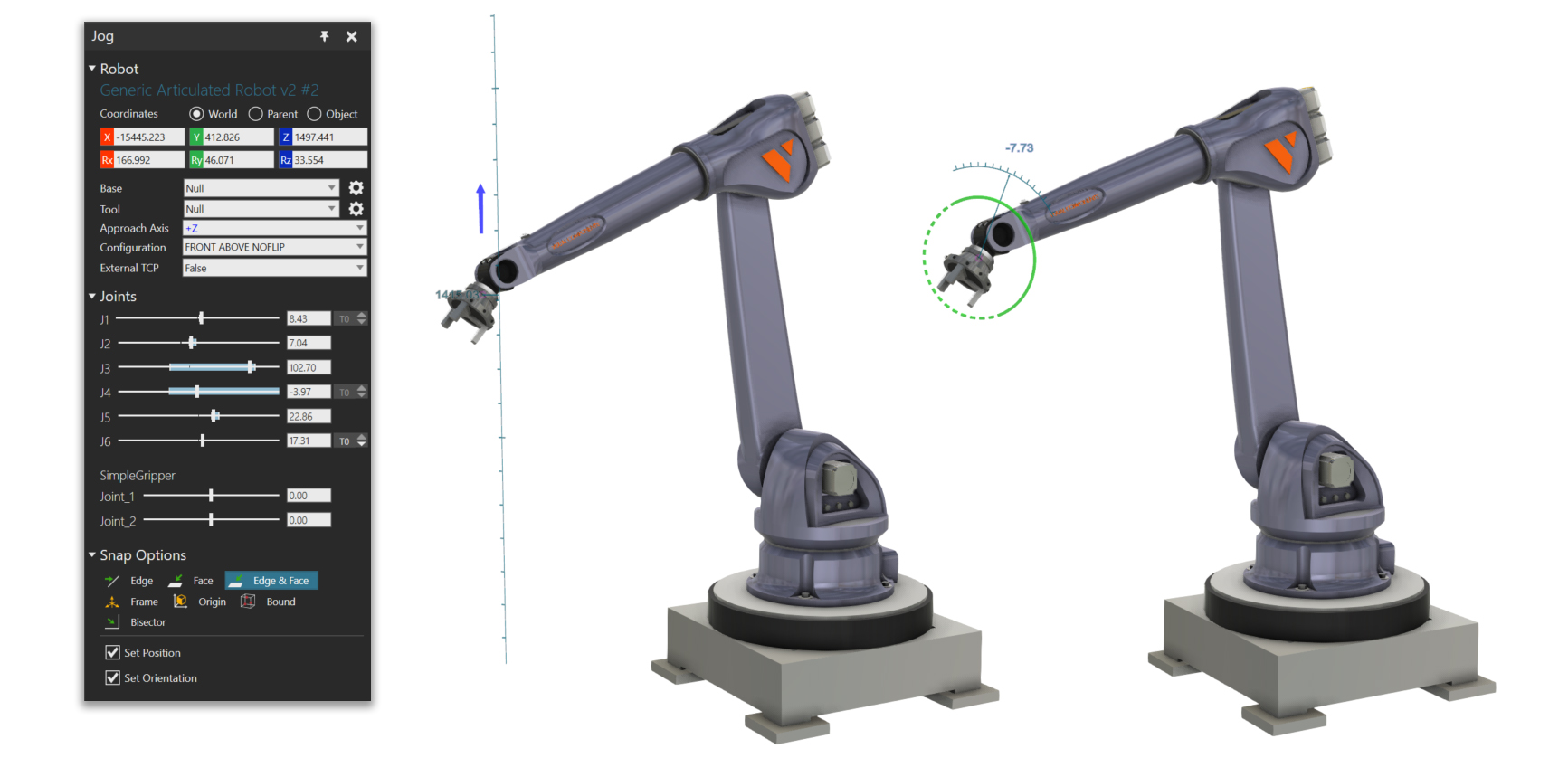
- Reachability analysis helps users to verify the robot is capable of reaching and interacting with objects in its work cell. It also helps to visualize the work cell space. This helps users to make important design decisions such as whether to extend the reach of a robot, rearrange equipment in the cell, add additional robots, or change the size or position of the robot.
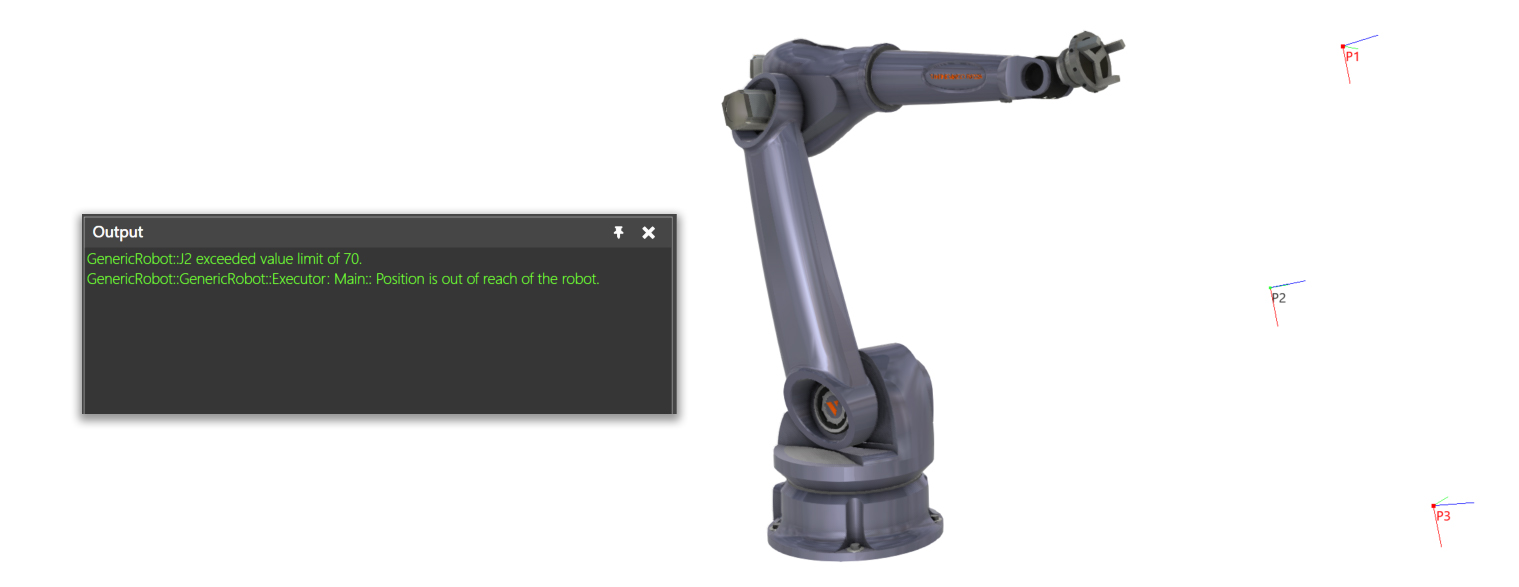
- Collision detection allows users to visualize potential collisions between the robot and other objects in its work cell. It works by simulating the robot paths and notifying users of the location and proximity of detected collisions and near misses. You can validate safety zones for the cell, workspace, and tool of a robot. In addition, you can identify potential hazards with robot motions by sweeping geometry and comparing it with the path of other resources like workers and vehicles. Collision detection is an important step in the verification of the robot program and a task that’s generally much safer and faster to be performed offline.
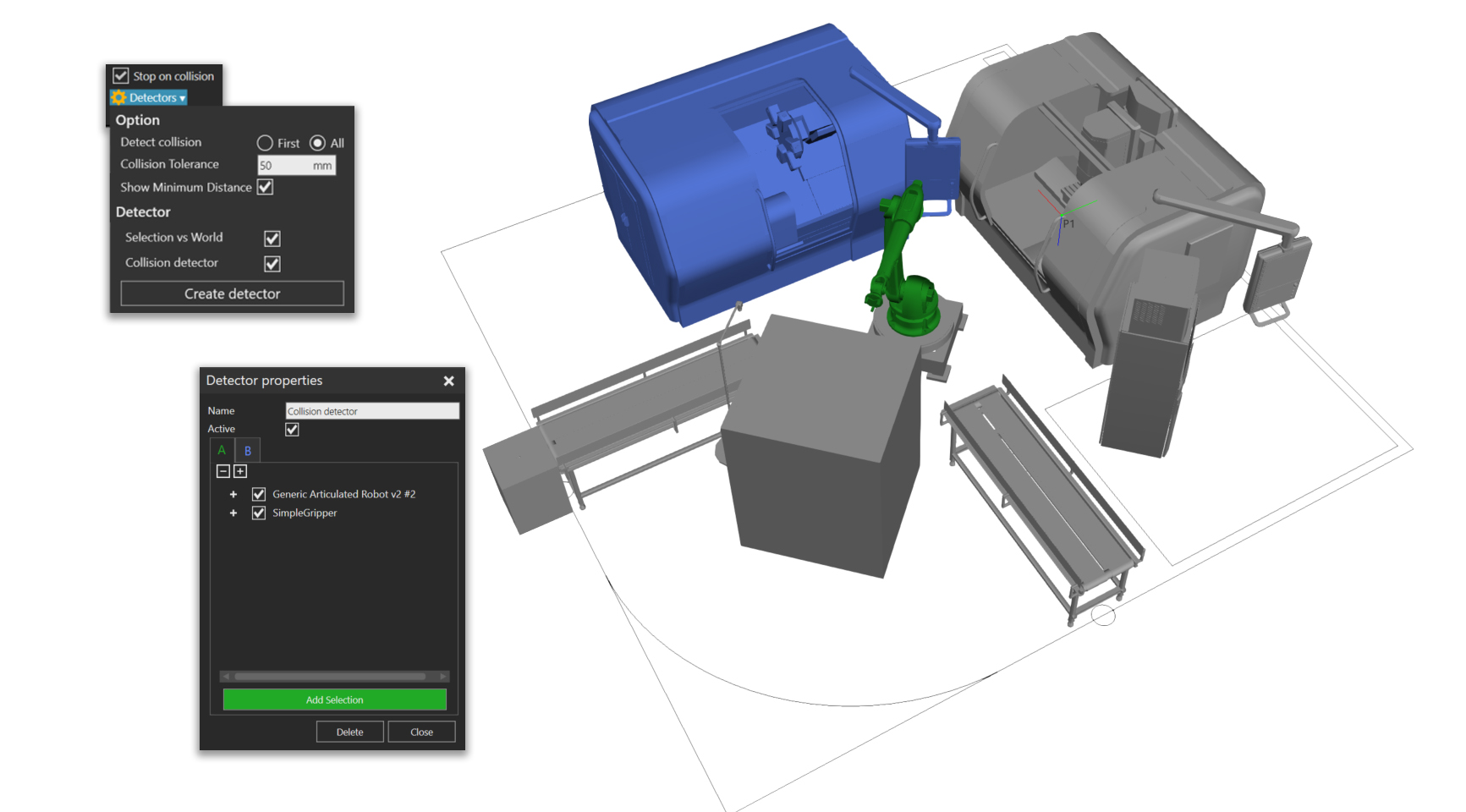
- Program editing allows users to define sequences of instructions for a robot and then simulate that program. You can define robot logic, such as order of the steps, type of movements, wait and triggering signals, and subroutines. You can also test inputs and outputs, optimize the logic and execution of tasks, synchronize robot motions, and validate motion paths.
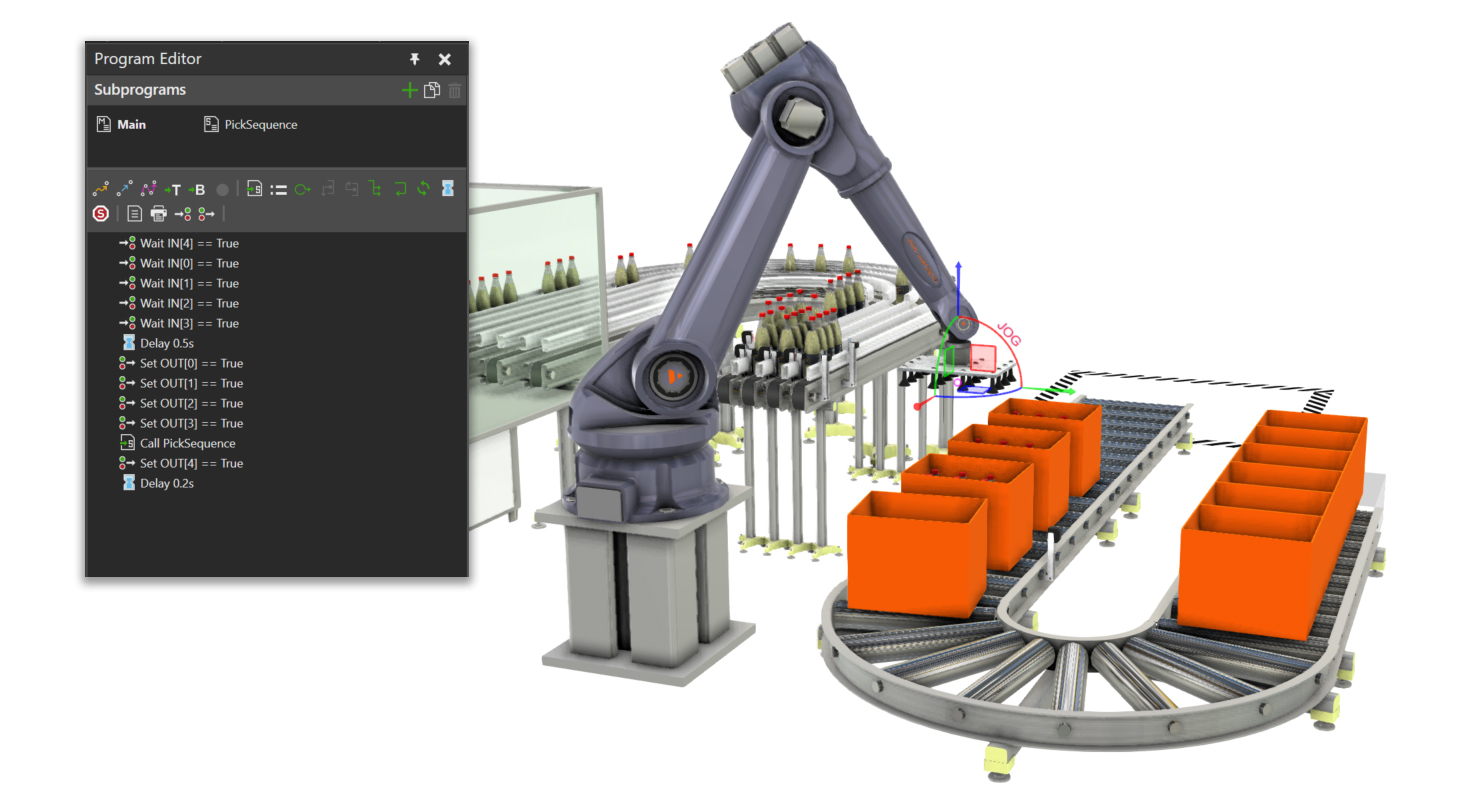
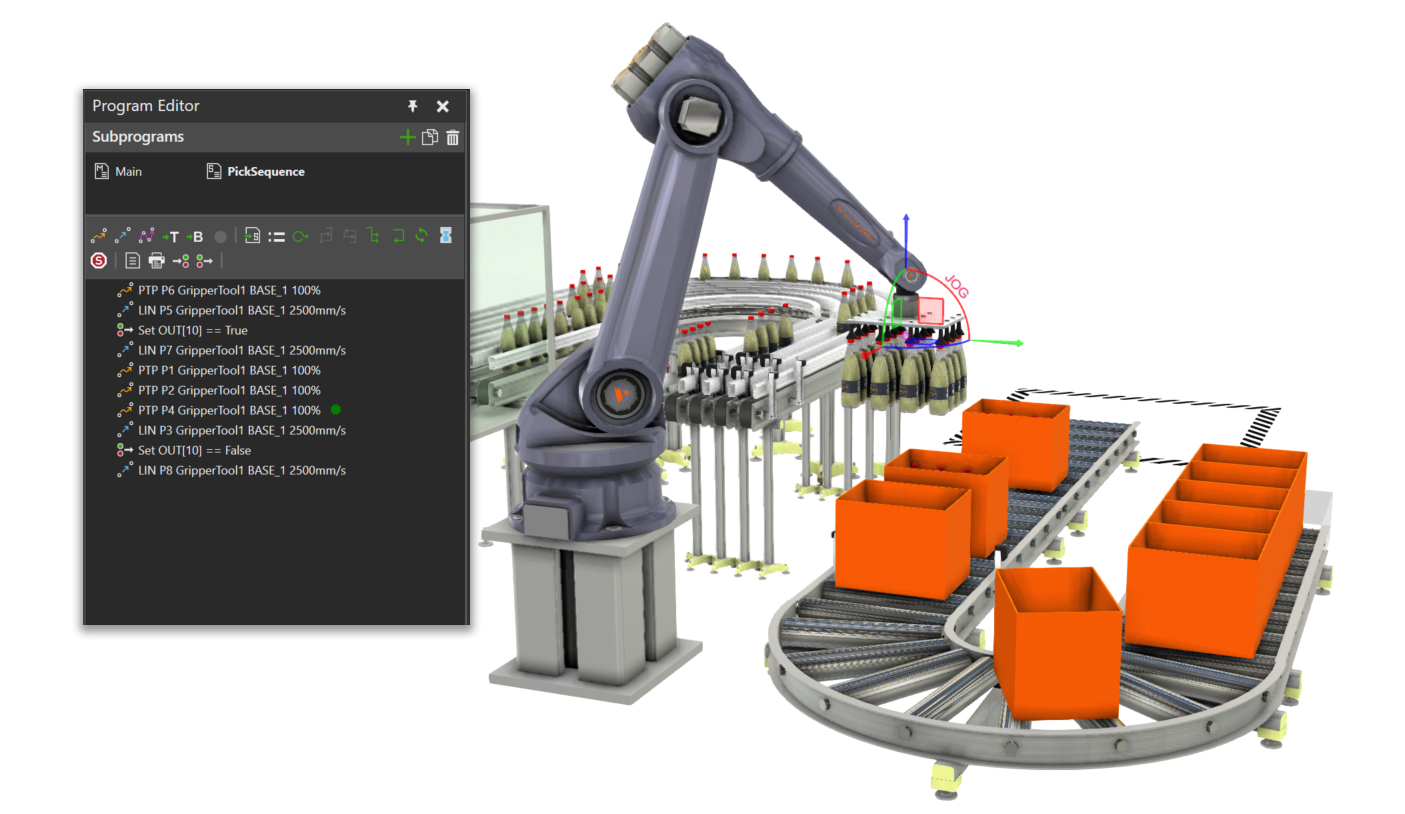
- Control flow allows you to use conditional IF statements, loops, and variables in a robot program.
- An IF statement defines a condition for executing one of two scopes, THEN and ELSE. The condition can refer to robot properties and inputs as well as local variables of the statement’s sequence. For example, you can quickly teach a robot to perform a different sequence of instructions based on input from sensors and counters for palletizing parts.
- A WHILE statement defines a condition for executing a scope of instructions in a loop. As long as the condition is true, the loop repeats itself until the condition is false. For example, you can make a robot do something until a request comes from another client.
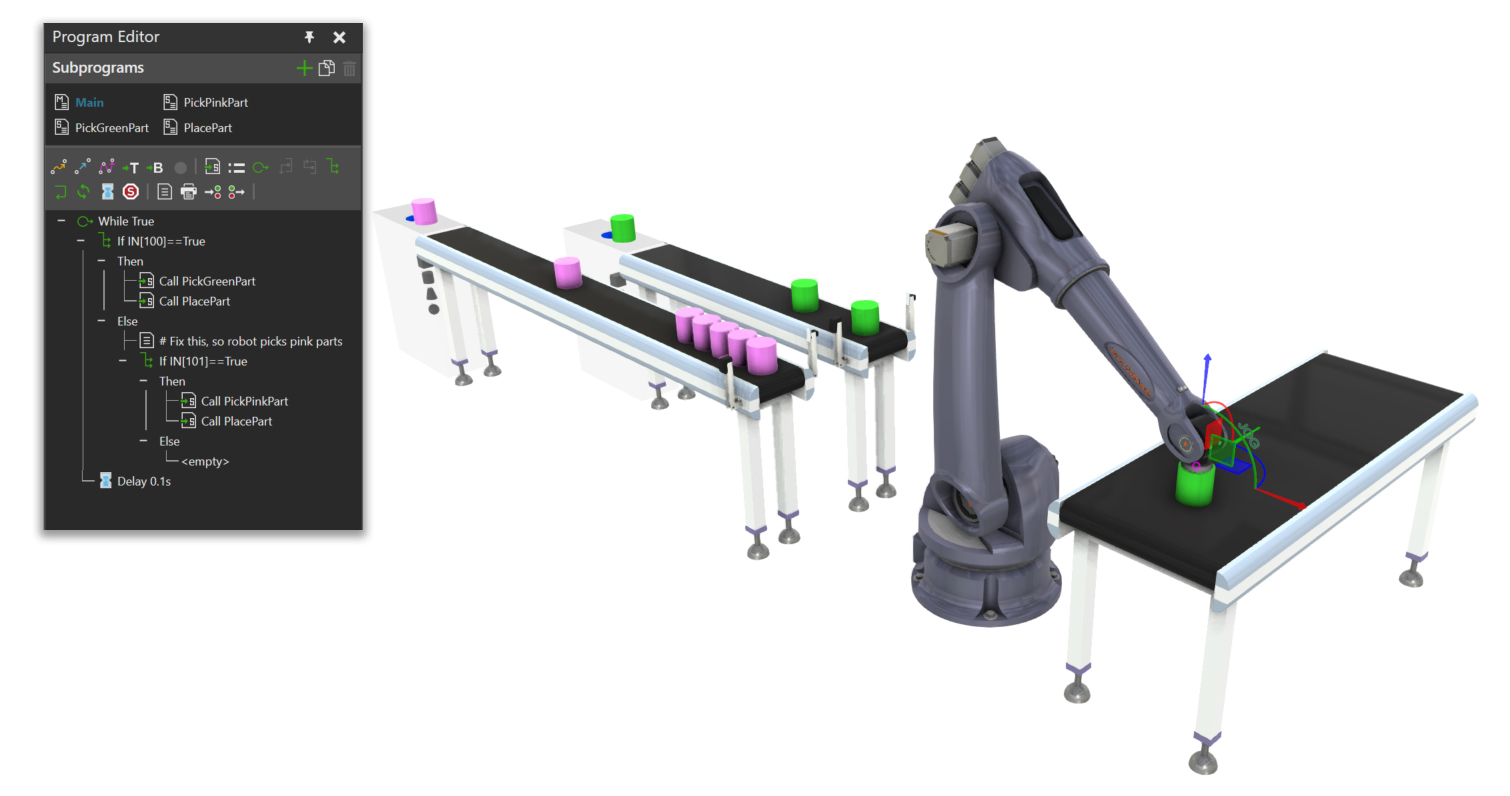
Design better robot work cells with Visual Components
In this article, we gave you a brief introduction to the Simple Robotics toolkit in Visual Components 4.0. With the Simple Robotics toolkit, users can virtually teach robots and validate the design of the work cell. Simulating the workflow yields production statistics, such as cycle times, production rates, and process bottlenecks; giving designers and planners valuable information that they can use to optimize the design of the robot cell.
Visual Components 3D manufacturing simulation software helps manufacturers and system integrators to design better robot work cells. With more than 1,200 robot models from 30+ major robot manufacturers available in our public eCatalog, Visual Components users have access to an extensive and constantly growing library of ready-made components.
If you’re interested in learning about how you can use Visual Components to simulate your robot applications, get in touch with us to schedule a free, personalized web demonstration.
Further reading
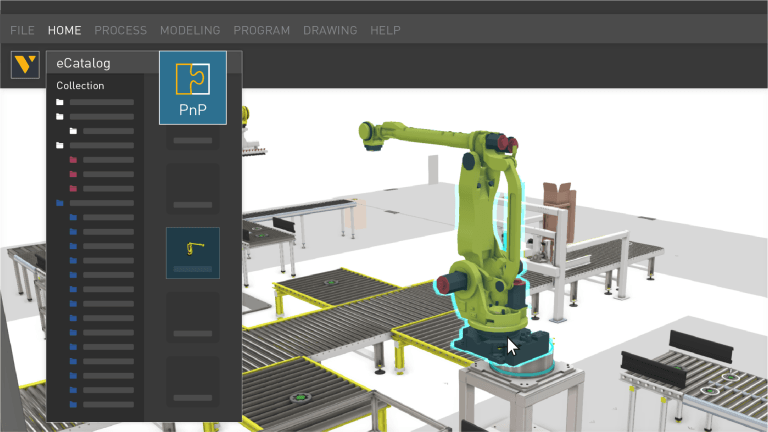
Leveraging simulation for factory layout design
Explore how discrete event simulation and digital twin technology play crucial roles during the ideation and planning phases of factory layout design. Our software simplifies the design process, providing accurate...
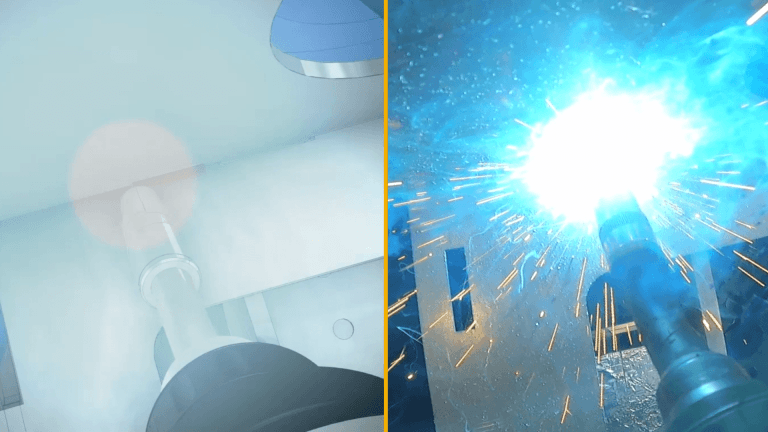
Robot offline programming (OLP): the complete guide (with examples)
This is your complete and comprehensive guide to offline robot programming (OLP). After introducing the topic, it addresses common misconceptions, the problems it resolves, benefits, and real-life example of its...
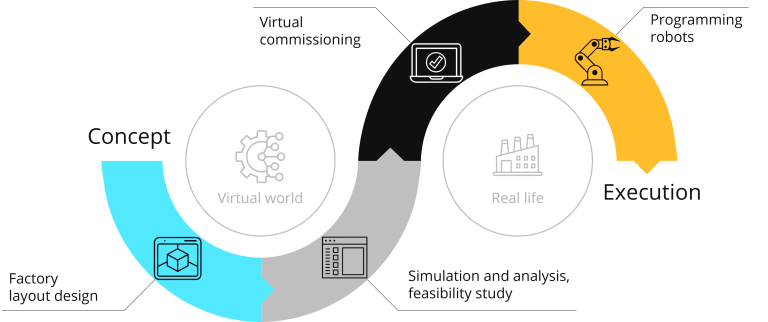
Manufacturing simulation: bring your projects from concept to reality
Manufacturers that commit to the digital transformation inherent in Industry 4.0 will reap the rewards of higher production efficiencies and faster project execution. Together, these will drive growth and profitability...