Introduction to Industry 5.0 and The Role of Manufacturing Simulation
Industry 5.0 addresses the technocentric limitations of Industry 4.0. Manufacturing simulation is essential for implementing the key elements of Industry 5.0: human-centricity, sustainability and resilience.
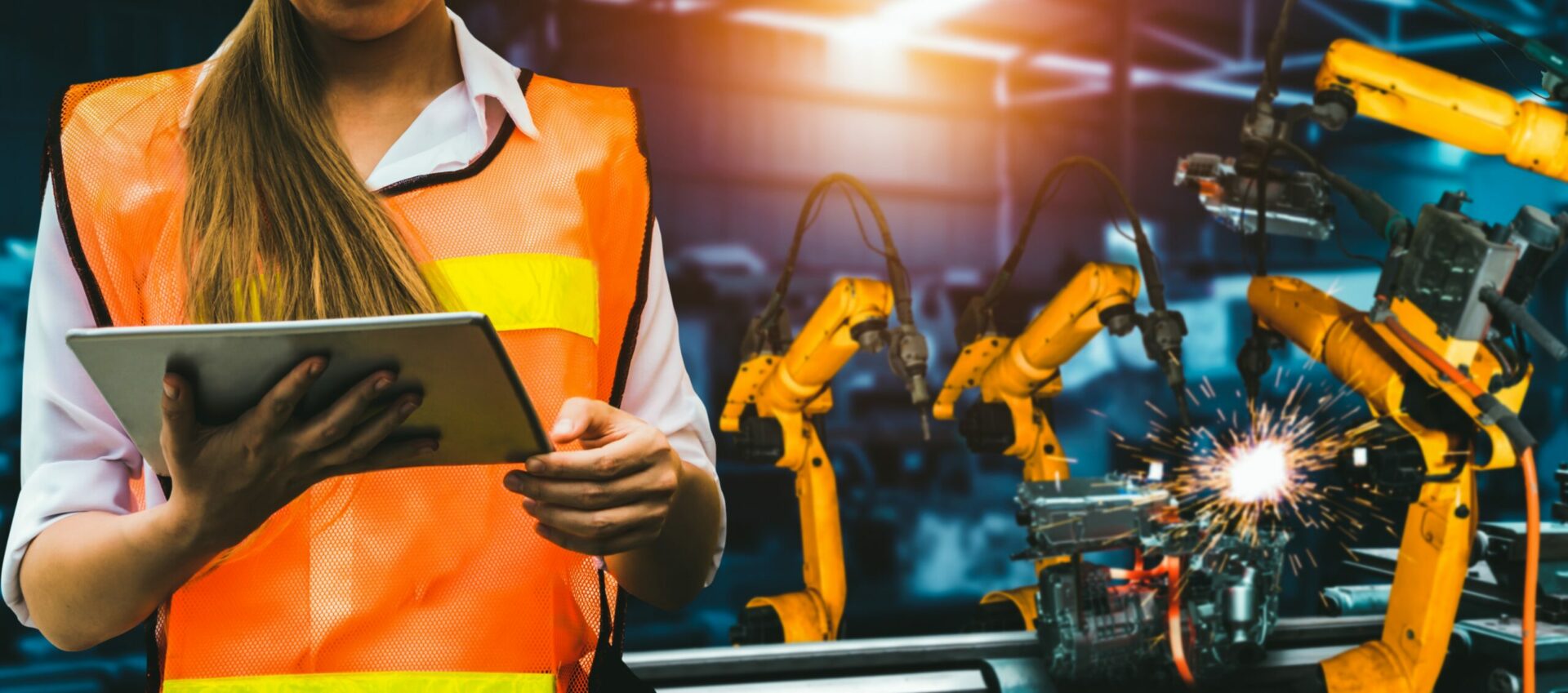
The manufacturing industry has been going through its fourth major transition since artisans gave way to workshops and factories. The first of these revolutions was mechanization and the use of steam power, which later succeeded by the adoption of electricity. Then came computerization, and today that’s being followed by the arrival of cyber-physical systems and advanced analytics, otherwise known as Industry 4.0.
Industry 5.0 however is not a typical succession to 4.0. Neither is it a marketing term conceived by an overworked advertising agency. Industry 5.0 refers to the human side of 4.0 and seeks to address the issues raised by 4.0 adoption.
Download the full report here.
Understanding Industry 5.0
Industry 4.0 is a technological revolution that will have far-reaching human impacts. In manufacturing, increasing automation means that many many workers may get displaced, not only on the factory floor but in administrative and even professional functions. Meanwhile, very little has been done to address some of the biggest challenges facing manufacturers, like where to find the next generation of workers, how to move towards a circular economy, and how to become more resilient in the face of unexpected change and supply chain disruption.
Championed by the European Union, Industry 5.0 is an effort to address the human impacts of the fourth Industrial Revolution. It starts from the belief that businesses want to do more than just maximize profit and provides pathways for integrating social and environmental concerns into technological innovation.
Altruism plays a part in this, but there’s also a strong element of self-interest. Young people want to work for socially-aware organizations and people want to buy from companies that behave responsibly. So, by adopting Industry 5.0 principles, organizations wish to safeguard their futures.
The Three Elements of Industry 5.0
Industry 5.0 is intended to promote:
- Human-centricity
- Sustainability
- Resilience
Here’s what each of these means.
Human-Centricity
This proposes that workers be viewed as investments and not costs. Thus, rather than seeking to drive down labor costs, manufacturers should look at how to maximize the return from their employees. This leads to the view that processes should be adapted to suit workers, and workers should be given the tools to help them do their jobs better.
Some of the key components that support the human-centric approach are:
- Exoskeletons
- Augmented reality
- Virtual reality
- Wearables
- Cobots
- Analytics
Furthermore, to maximize the benefits of these new technologies, which include higher productivity, less waste, and lower accidents, workers should be included in their design and deployment. As part of this, it’s believed that there is a clear need for upskilling and reskilling.
Sustainability
Businesses want to reduce their environmental impact by using alternative energy sources to minimize their footprint. At the same time, it is important to lower the operational costs but also attract young talents. Businesses are realizing that it is the right thing to do and they are adding sustainability plans to their strategy.
One reason is to lower operating costs by cutting resource consumption and waste. Another is that it’s because it’s what employees, and younger recruits, in particular, want to see. And a third reason is that it’s the right thing to do.
Industry 5.0 addresses how manufacturers and others can move towards a circular economy where recycling is integral to production and consumption. With an emphasis on this, plus re-use and repurposing, Industry 5.0 encourages adopting artificial intelligence (AI) and additive manufacturing to avoid resource depletion and environmental degradation.
Resilience
From chip shortages and COVID-19 to energy price spikes, recent events have renewed focus on supply chain and other business risks. Resilience in this context refers to manufacturers finding ways to become more flexible, responsive, and adaptable in the face of disruptive events.
Some tools and capabilities that will play a part in this are:
- Deployment of modular factories
- New materials (and the ability to transition seamlessly between sources)
- Remotely-operated factories
- Real-time risk monitoring
- Enhanced cybersecurity
Who is Industry 5.0 For?
Any perception that Industry 5.0, (and also Industry 4.0,) is only for deep-pocketed global manufacturers is incorrect. SMEs are just as capable of adopting these new technologies and perspectives as their larger brethren, and perhaps more so. For many of the trends and technologies discussed above, implementation is as dependent on open minds and a willingness to change as on financial resources, and these are areas where SMEs often excel.
How Simulation Supports an Industry 5.0 Transition
Factories and manufacturing processes are becoming smarter and competitors never stop looking for an “edge.” Against this background, it’s more important than ever to keep changing and improving, but also to do it faster and to avoid mistakes.
Manufacturing simulation plays a key role in all three elements of Industry 5.0. By modeling existing or proposed manufacturing systems, it provides a “virtual sandbox” that enables risk-free exploration of ideas and alternatives. It’s used to gain a deeper understanding of complex operations and relationships, to identify potential problems or conflicts, and to identify opportunities and solve current problems.
Specific ways in which simulation supports an Industry 5.0 transition include:
- Creation of digital twins
- Virtual commissioning
- Modeling supply chain disruptions
- Travel avoidance
- Risk-free experimentation
- Upskilling
A digital twin is a complete and accurate representation of part or all of the production process. Most importantly, by connecting it to sensors installed on the physical system, it maintains fidelity to real-world conditions. With this, it’s possible to evaluate changes and the impact of disruptions and come up with alternative production schedules. It also helps with debugging problems and can avoid the need for technicians to travel to work sites or factories.
Virtual commissioning uses a digital twin to accelerate the implementation of new equipment and processes. Putting this together before the equipment build is finished accelerates programming and debugging and allows an earlier start to operator training.
A Tool for Industry 5.0
By focusing on human and other non-profit-related issues, Industry 5.0 addresses the technocentric limitations of Industry 4.0. Adoption will however depend on the ability to model existing systems for optimization and to explore alternatives before equipment is implemented. Simulation is the tool that provides this “virtual sandbox.” Visual Components is a leader in 3D manufacturing simulation.
At Visual Components, we wanted to learn more about this shift to Industry 5.0, so we worked with market research firm OnePoll to gather the views of 360 manufacturing decision-makers in the UK, the US, and Europe (Germany and France). Participants were asked about their current issues, their progress on cost savings, adopting efficient and resilient processes, and the current status of their companies in terms of sustainability.
Curious about the results? You can find our full report here.
Further reading
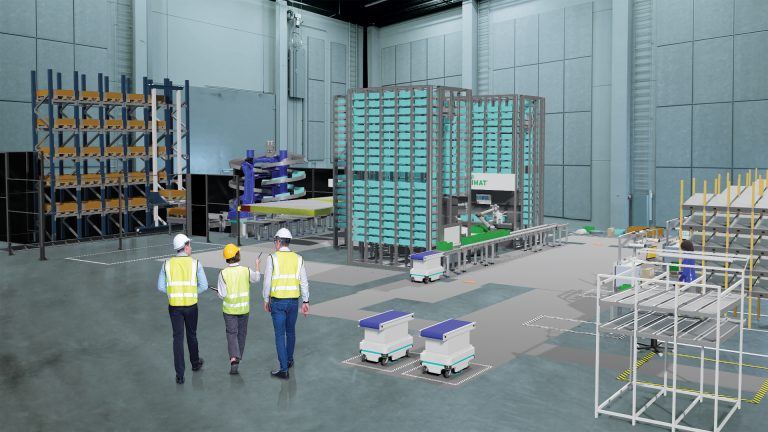
The future of automated manufacturing (and why humans still matter)
Automation in manufacturing has been evolving for decades, but its true impact isn’t in replacing people, it’s about making them more capable. We spoke with Mika Anttila, one of Visual...
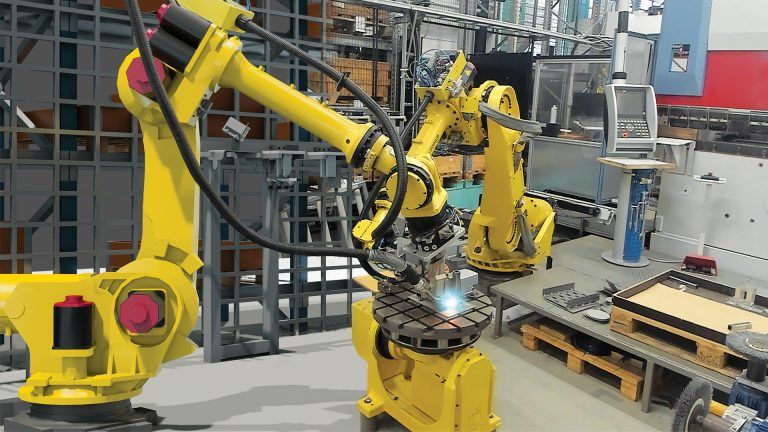
Understanding digital twins in manufacturing
Digital twins go far beyond static models or simulations. They bridge the gap between virtual and physical systems, offering real-time insights and control. But with so many definitions floating around,...
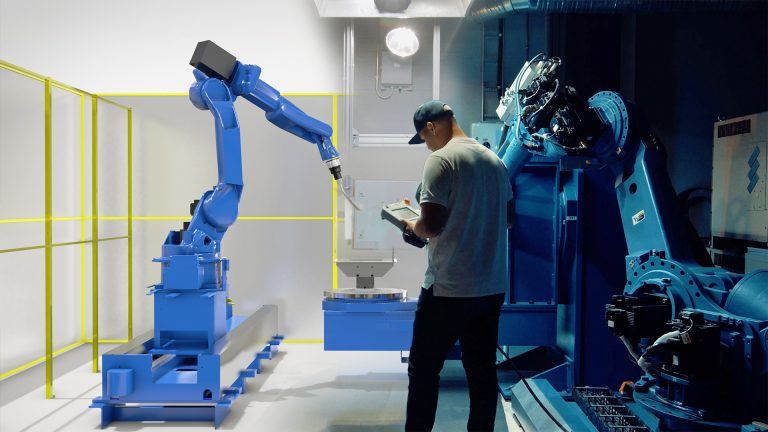
Tackling the manufacturing skills shortage with simulation and robot offline programming
The manufacturing industry is grappling with a significant skills shortage, exacerbated by the pandemic and an aging workforce. According to The Manufacturing Institute, 78% of companies are concerned about this...