Developing Industrial Processes Through 3D Simulation
Ongoing industrial transformation requires companies to invest in digitalization and increase the degree of automation of processes. 3D simulation makes the development of production and logistics processes much more efficient and reduces development costs.
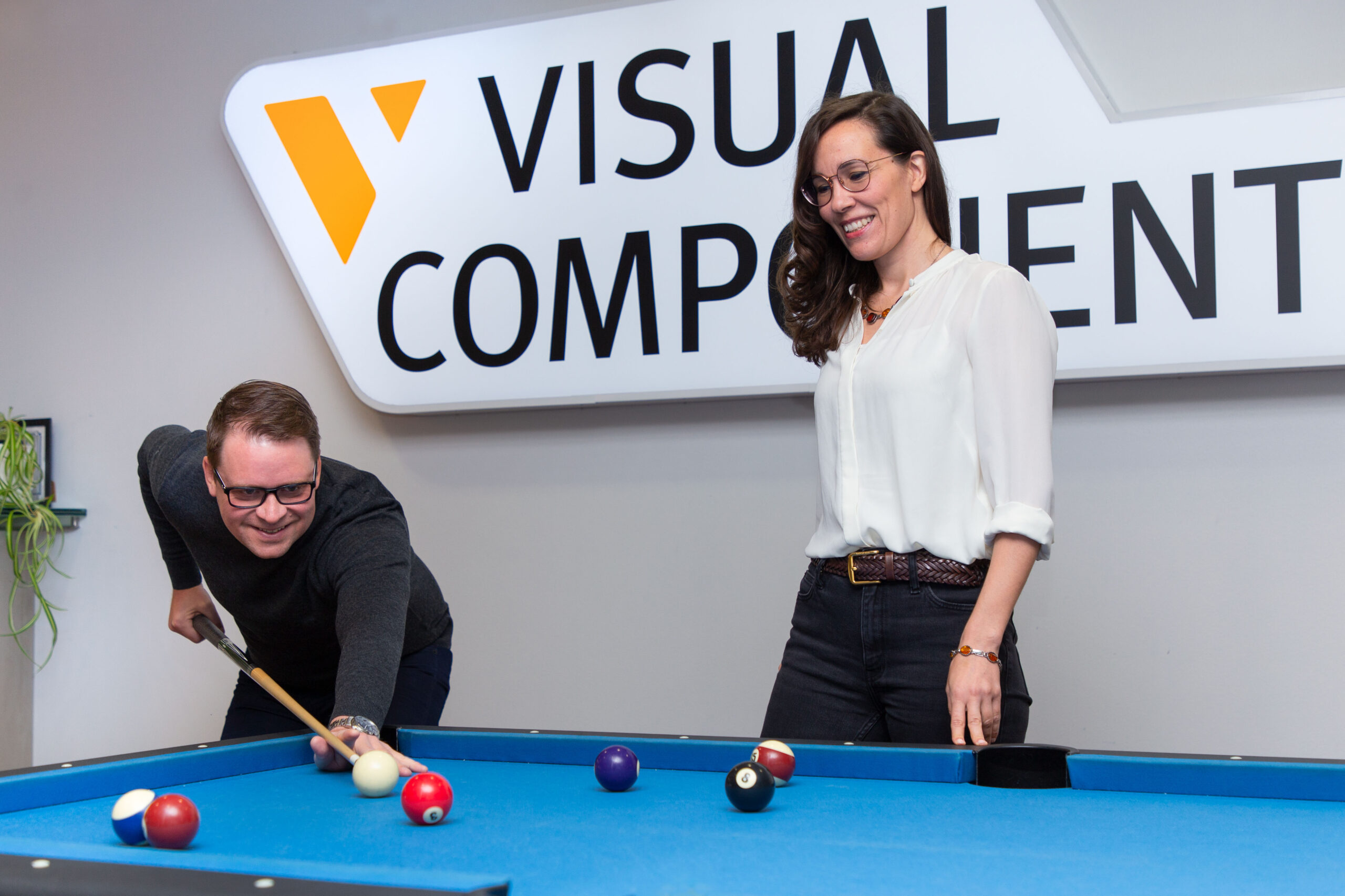
Ongoing industrial change requires more significant investments in sustainable development and improved occupational safety and health in the manufacturing industry. At the same time, global competition is fiercer, and employee availability is decreasing due to an aging population. Therefore, industrial processes need to run with fewer employees and be more efficient and eco-friendlier.
According to Mikko Urho, CEO of Visual Components, industrial companies need to increase their use of digitalization and process automation. 3D simulation helps plan production updates flexibly and with reasonable costs. They serve equally to visualize a change in a single production line and to modernize the entire production process.
“Design based on 3D simulations is an integral part of production automation and the use of robotics. They help test, optimize, and develop production lines to be as efficient as possible. Digital simulation models improve production efficiency and accelerate decision-making processes,” Urho says.
3D simulation is now also within reach for smaller businesses
Illustrative simulations make it significantly easier to understand process flows, facilitating cooperation between designers, decision-makers, and line employees during the development process. As a result, the effectiveness of processes is easier to evaluate, and any problems which may arise can be dealt with during the design phase.
“Simulation helps solve even highly complicated challenges quickly and cost-effectively. Testing and ensuring the effectiveness of an application using a digital model saves money, reduces waste, and improves workplace safety,” Urho says.
Visual Components is one of the pioneers in 3D manufacturing simulation, having provided 3D visualizations for the industrial sector since 1999. Its customers include medium-sized and large enterprises such as Kone, Wärtsilä, Fastems and Etteplan.
Technological development and lower prices have made 3D simulation much more attainable for smaller companies.
“Compared to the solutions of many of our competitors, our concept is easy to use, allowing our applications to be used more broadly across customer organizations. Our software supports various simulation solutions, and we have access to an extensive component library. Open interfaces ensure easy connectivity between our software and customer companies’ other solutions,” Urho says.
A multicultural and open working community where each employee is respected
During its over 20 years of operations, Visual Components has grown into an international company with subsidiaries in Germany and North America, a sales office in Sweden, and 40 global partner companies. Recording net sales of EUR 12.7 million last year, Visual Components’ software products are still developed and coded in Finland.
“Our personnel has increased by 25 per cent in a year, and we now have 83 employees. We will continue our strong growth and aim to employ more than 90 people by the end of this year. We especially require software developers skilled in 3D simulation, simulation experts and various other specialists. Talented people at various stages of their career interest us, ranging from experienced software developers to recently graduated professionals of the future,” says Laura Typpö, Head of People at Visual Components.
At Visual Components, employees represent more than 20 nationalities, which is why the organization’s official working language is English. According to Typpö, the corporate culture underlines multiculturalism, openness and showing respect to one another. The organization has a low hierarchy, its operations are transparent, and all employees can have their say in the company’s development.
“Our international success is based on our mission and vision, developed and shared by all our employees. It’s our way of celebrating our successes together. Each employee must feel proud of what we do,” Typpö says.
HR management is one of the cornerstones of Visual Components’ operations. The company invests in fulfilling each employee’s potential, listening to employees’ needs and wishes, and giving positive feedback.
“Our company is changing fast, driven by our growth. We are especially appreciated by people who want to have an impact and work in a working environment that is moving forward,” Typpö says.
Further reading
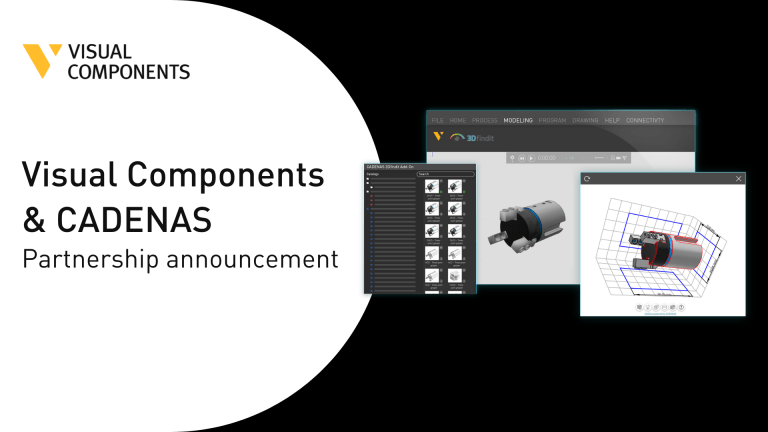
Visual Components partners with CADENAS to deliver millions of vendor-verified CAD models for 3D manufacturing simulation
Seamless access to verified CAD models At Visual Components, we strive to improve how our users plan, simulate,...
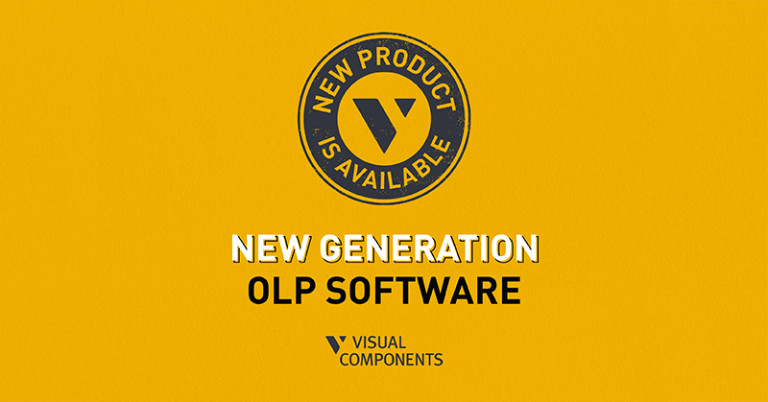
Introducing Visual Components Robotics OLP
We're excited to announce a significant upgrade for Visual Components. We've transitioned to a robust solution that serves both manufacturing simulation and robot offline programming. This new offering, named 'Visual...
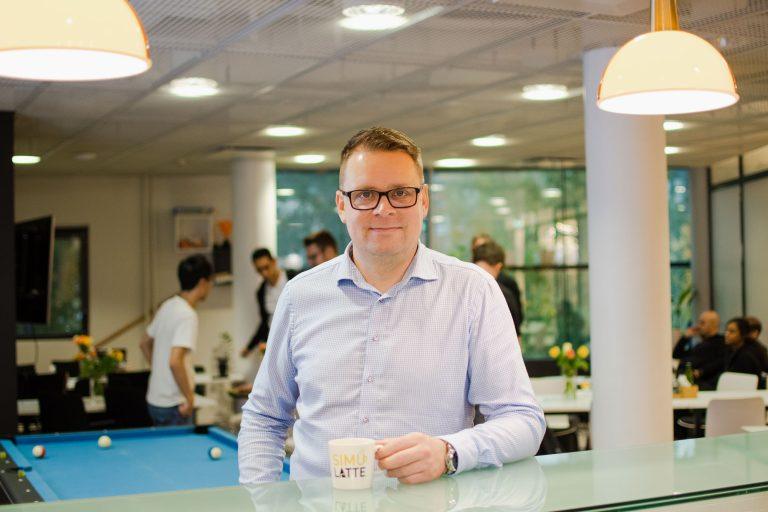
Visual Components accelerates growth strategy with acquisition of Delfoi’s robotics division
One-stop-shop for digital transformation of production systems becomes a reality.