Mastering complex welding: Bunorm Maschinenbau’s quality and efficiency boost with Visual Components OLP
Bunorm Maschinenbau, a full-service supplier known for complex welding solutions, is committed to maintaining a high level of modernization and flexibility of their infrastructure. With their wide-ranging capabilities, the focus on boosting production efficiency and quality is paramount. By leveraging Visual Components OLP, the company is able to program and optimize complex parts before production, leading to faster programming and improved weld quality, even for smaller batch sizes.
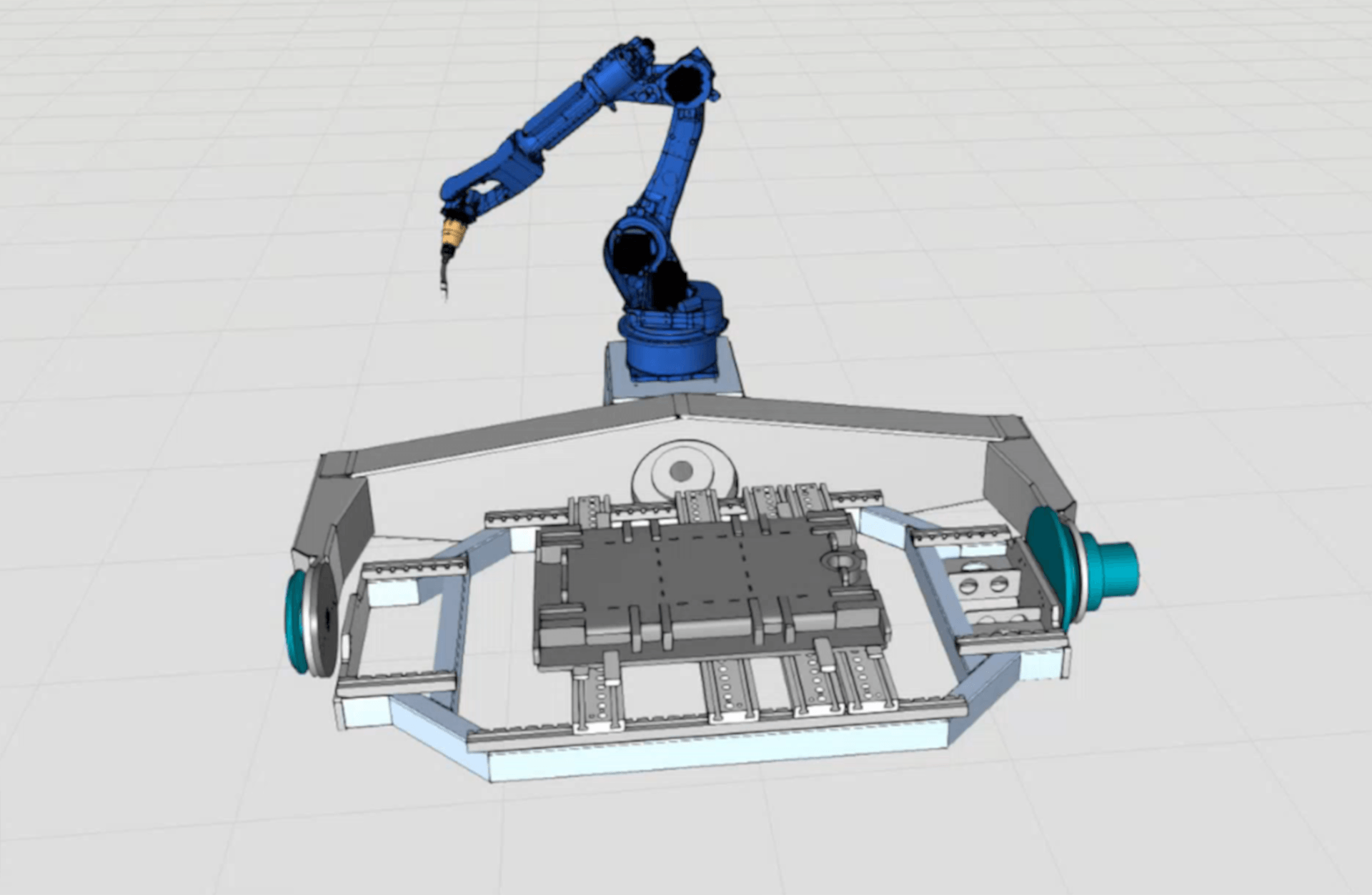
From simple welding constructions to complex welding solutions
Bunorm Maschinenbau, a Swiss company founded in 1965, started with basic welding constructions before transitioning to machine engineering. Today, the company specializes in machining and special purpose machinery construction, with a particular focus on complex and large welded constructions with mechanical processing. They offer the production of small and large individual parts, small series, complete assemblies, and systems.
Four years ago, Bunorm Maschinenbau joined the Swiss Factory Group to strengthen their presence in the Swiss market. The company employs about 100 people across two locations with a total production area of 10,500 sq. m. (113,021 sq. ft.). As a comprehensive welding solution provider, they are committed to the consistent modernization of their machine park.
The challenge: programming diverse complex welds efficiently with quality
With the significant flexibility of their machinery, Bunorm Maschinenbau can handle machine parts ranging from 100 mm to 18,000 mm. However, the necessity to alternate between different products and adjust to fluctuating demand patterns can result in inefficiencies, extended lead times, and heightened operational costs. These are typical production challenges encountered by manufacturing companies in a high-mix, low-volume environment. To ensure high efficiency and quality in their production process, Bunorm Maschinenbau aimed to enhance their robot programming efficiency and transition beyond manual programming.
D’Angelo Michael, Strategic Welding Solutions Manager at Bunorm Maschinenbau, has been with the company for over a decade. Starting as an apprentice tasked with welding on the production line, he has now become an international welding specialist and the head of non-destructive testing. With 10 years of robot programming experience, he is also in charge of managing Yaskawa welding robots and programming for special projects, such as aviation.
Complex welding capabilities enabled by offline programming
Offline programming (OLP) allows complex individual parts, as well as series parts, to be programmed and optimized in advance on the software outside of the production.
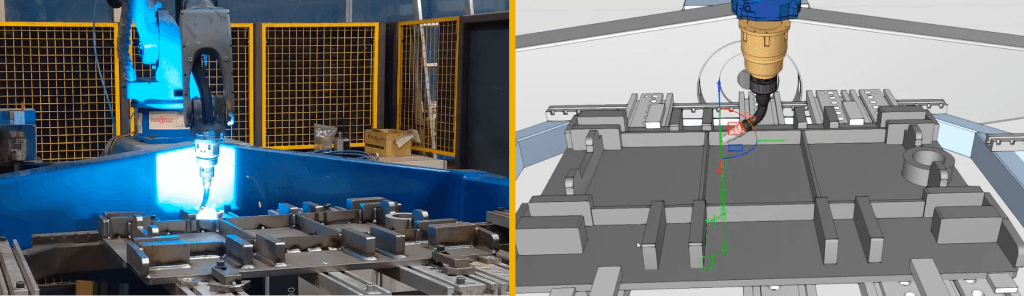
The company can weld constructions up to 20 tons and machine constructions up to 60 tons. They have two welding robots from Yaskawa, both programmed with Visual Components OLP. The first robot Yaskawa YRC1000 can weld workpieces up to 7 m (22 ft) in length, 1.5 m (4.9 ft) in width, and up to 3.5 tons. The second robot Yaskawa DX200 can handle workpieces up to 2.5 m (8.2 ft) in length and 1.5 m (4.9 ft) in width, up to one ton of weight.
OLP can be a valuable tool in projects that involve not only extensive robotic welding, but also partial robotic welding. One example is the production of a machine designed to seal tunnels with foil to prevent water ingress. A major part of this machine was robotically welded with the robot programmed using OLP.
With Visual Components OLP, multi-layer welding seams can be programmed easily, making it possible to handle complex welding tasks. The software also simplifies troubleshooting robot program for reachability and collision issues.
Visual Components has a huge library. The list of post-processors you’re seeing on my screen right now is just what you get for free (included in the license). I believe they have even more based on what I know, but I’m just a customer. I think Visual Components is compatible with every robot brand.
D’Angelo Michael, Strategic Welding Solutions Manager at Bunorm Maschinenbau
Improving weld quality and production efficiency
Offline programming makes it possible to implement measuring operations very easily, leading to an increase in weld quality. The software enables efficient operation of the welding robot and minimizes downtime.
Even for small batch sizes, such as 15 identical pieces, offline programming proves to be more efficient than manual programming. With online programming, it would take at least two days to program the robot for such a task using the teach pendant. With offline programming, the same program can be completed in half a day, reducing programming time by 75%.
What I will show you is how I post-process the program… you can see that with these 3 statements, I just created 41 lines of program. I could have written 41 lines of code on the controller, but this is my way of showing you how efficient Visual Components OLP is.
Without Visual Components OLP, we wouldn’t consider it to be efficient enough with the robot if we were to program it by hand on the controller.
D’Angelo Michael, Strategic Welding Solutions Manager at Bunorm Maschinenbau
Getting started with offline programming
If you are a manufacturing production manager considering the adoption of OLP software, D’Angelo recommends testing the software if possible. Visual Components provides the opportunity for potential users to evaluate our software, request a personalized web demo here to get started. He also highlights the excellent support provided by Visual Components, citing his own experience of learning to use the software.
“Vidisha, an engineer from Finland, flew to Switzerland. She measured the machine and the whole jig from the robot. She created the cell for me and simultaneously taught me how to use it during her visit. These three days provided a good enough foundation for me to further improve my skills. Whenever I had a question, I could always reach out to Vidisha via call or email, and she responded very quickly. The support from Visual Components is really, really great.”
D’Angelo Michael, Strategic Welding Solutions Manager at Bunorm Maschinenbau
Bunorm Maschinenbau’s case study showcases how a parts supplier can utilize offline programming to address complex welding projects, achieving substantial gains in efficiency and quality, even within a high-mix, low-volume production setting. With a commitment to innovation and a focus on efficiency and quality, Bunorm Maschinenbau continues to strengthen its standing as a leader in the manufacturing and assembly of complex and large parts in the Swiss market.
About Visual Components
Founded by a team of simulation experts and amassing over 20 years in business, Visual Components is one of the pioneers of the 3D manufacturing simulation industry. The organization is a trusted technology partner to a number of leading brands, offering machine builders, system integrators, and manufacturers a simple, quick, and cost-effective solution to design and simulate production processes and offline robot programming (OLP) technology for fast, accurate, and error-free programming of industrial robots.
Want to learn more about the benefits of our solutions for your business? Contact us today!
Further reading
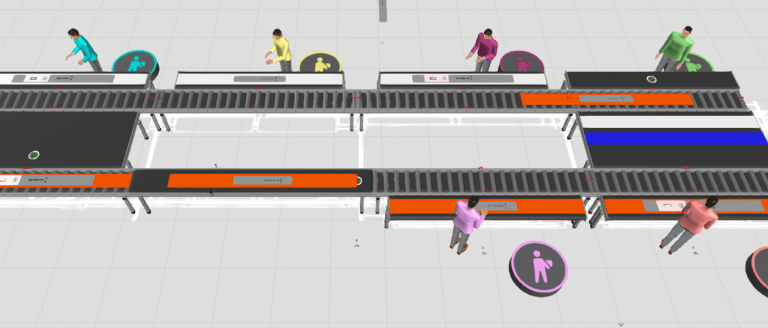
Elevating assembly planning for elevator button panels at KONE with 3D simulation
Planning a new assembly line for two product variants, KONE’s Northern Italy site needed to ensure smooth flow and minimal risk of defects. With Visual Components, they simulated and tested...
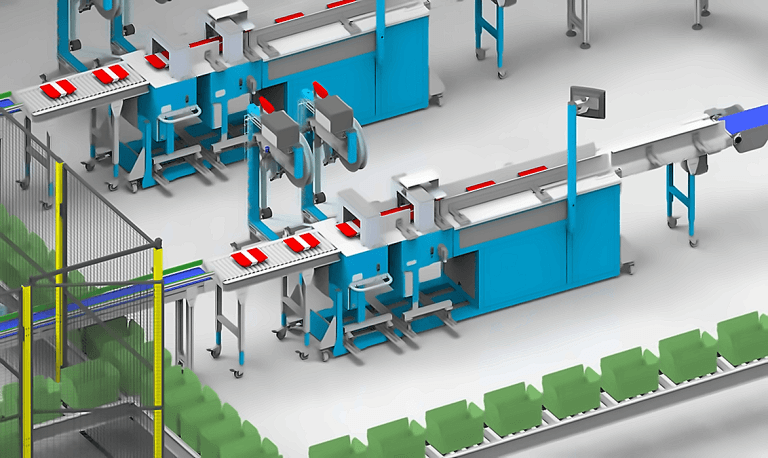
How Hollander Techniek designed an automated custom meal packaging system with Visual Components
When Uitgekookt set out to automate its meal packaging process, they needed a system that could handle custom orders with speed and precision. Hollander Techniek used Visual Components to design...
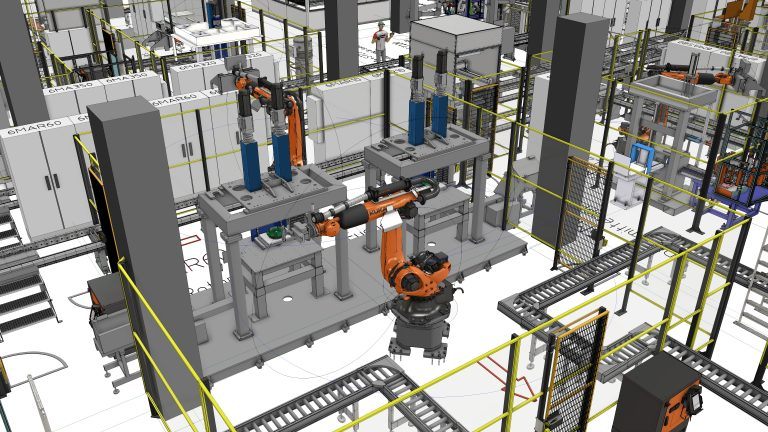
How EMIL SCHMID MASCHINENBAU designed a high-speed battery assembly plant with Visual Components
Facing the challenge of designing a fully automated battery assembly plant for a customer, EMIL SCHMID MASCHINENBAU turned to Visual Components. With 3D simulation and an extensive library of factory...