Welding innovation and tradition: how Berlin Gardens forges ahead with Visual Components Robotics OLP
Berlin Gardens, renowned for its high-quality outdoor furniture, encountered operational hurdles in their manufacturing processes, particularly in welding automation, especially as demand for their furniture continued to grow. The integration of Visual Components Robotics OLP marked a pivotal moment, as it helped program robots for complex tasks, notably welding aluminum fixtures to the bottom of their furniture, with consistent speed and quality.
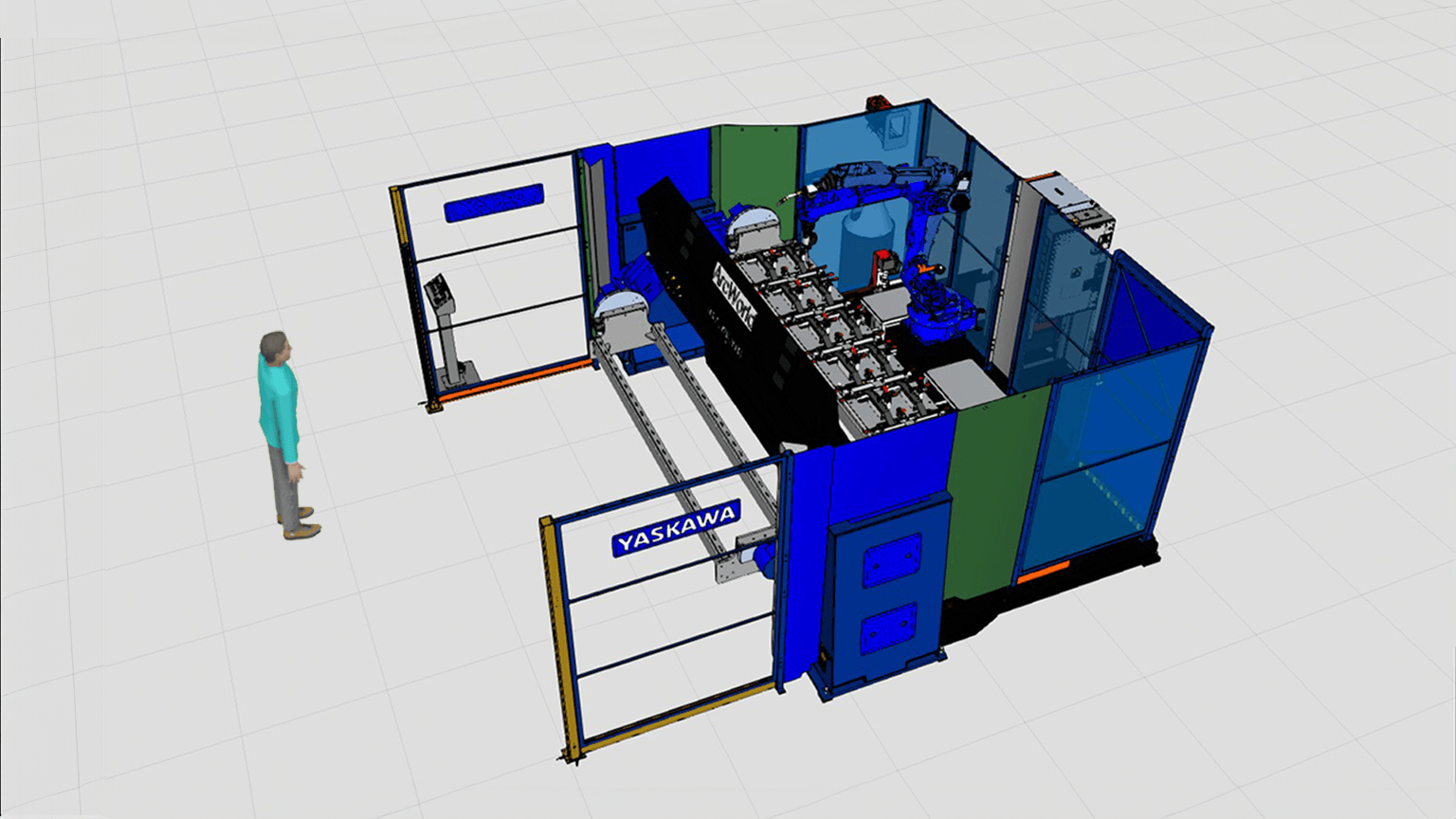
From humble beginnings to a key player in the outdoor furniture industry
Berlin Gardens, established in 1988 in the heart of Amish Country, Ohio, began as a humble greenhouse, selling plants and flowers to the local community. This early period instilled a deep understanding of craftsmanship and community values, which would later become the bedrock of their business philosophy.
The transition to manufacturing outdoor furniture marked a significant shift in their business model. Their focus on easily shippable, stylish furniture designs quickly set them apart in the market. Under the leadership of Sam Yoder since 2008, the company has expanded its workforce to 250. The company has evolved to specialize in manufacturing high-quality outdoor poly furniture and backyard structures, employing state-of-the-art machinery alongside time-honored crafting techniques.
Understanding the competitive landscape
In the last 15 years, the poly furniture industry has transformed significantly. What was once a novel concept has now become a competitive and bustling market segment. Berlin Gardens has not only kept pace with this change but has also established itself as a key player.
The company’s unique approach focuses less on external competition and more on internal customer service – prioritizing the well-being and satisfaction of its employees. This philosophy underlines their belief in doing business with integrity, including fulfilling promises such as on-time shipping, which in turn enhances external customer service. Sam Yoder’s vision incorporates a Lean Manufacturing approach, constantly refining processes to balance the pursuit of quality with the need for speedy fabrication.
In line with this pursuit of quality with the need for speedy fabrication, the integration of Visual Components Robotics OLP in Berlin Gardens’ welding of aluminum fixtures marked a significant step in the right direction.
Derrick Yoder, the Aluminum Production Manager at Berlin Gardens, oversaw the transition to more efficient and precise automation in processes like arc welding. The crucial first step in this transition was the initial setup and calibration of the robots, expertly handled by specialists from Mach Machines, Partners of Visual Components based in Ohio, USA. This essential groundwork, complemented by Mach Machines’ comprehensive training on the software, provided Berlin Gardens with a robust base for future utilization of Visual Components Robotics OLP in other processes.
Following this foundational setup, the focus shifted to the advanced functionalities of Visual Components Robotics OLP. The main robot programmer at Berlin Gardens, an Amish worker, found the software exceptionally user-friendly and efficient. With just a couple of clicks, he could program multiple robot paths for the Yaskawa robot cell, all on a single platform. Not only that but the knowledge could be stored in the software for future robot programmers to reuse or optimize.
The biggest difference was the amount of points programmed by simply selecting a joint in the software. And it’s not all simple movements. We have different fixtures where it takes a bit of maneuvering to place the welds, but the software handles them just fine with accuracy. When programming point to point with the pendant before everything was very repetitive – spending hours manually moving the robot. Even then it’s hard to stay consistent with different moves with the robot which can cause inefficiencies on wasted movements. With the software everything can be controlled with the same movements each time.
Derrick Yoder, Aluminum Production Manager at Berlin Gardens
The move from traditional, manual programming to an automated system not only streamlined operations but also represented a significant leap in the company’s technological capabilities and digital transformation. Visual Components Robotics OLP found its critical application in programming welds for aluminum fixtures, essential components of the company’s outdoor furniture. This software enabled the programming of complex weld paths and optimized robot movements, leading to significant efficiency improvements.
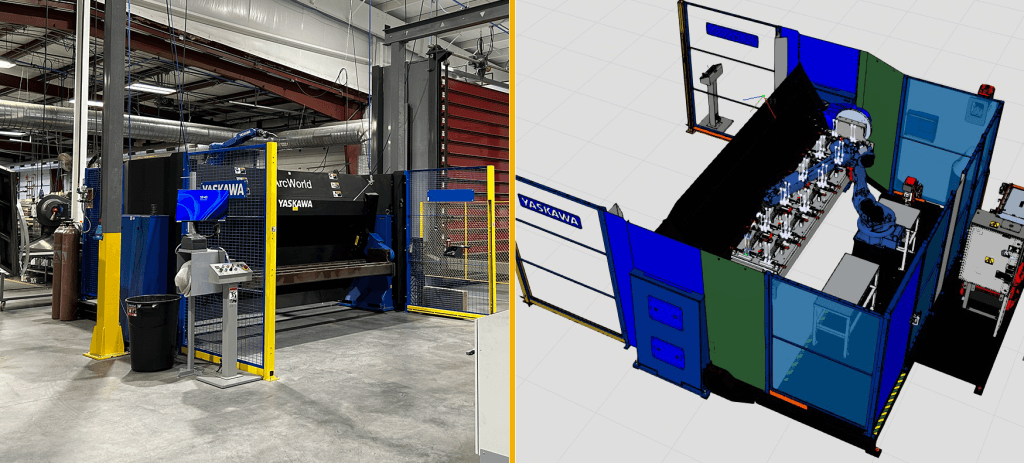
The shift from manually programming each point with a pendant to selecting joints through the software reduced repetitive tasks, ensuring consistency and accuracy. This change was not just about saving time; it was about enhancing the quality of each piece of furniture produced, maintaining Berlin Gardens’ reputation for excellence. The feedback from the team has been overwhelmingly positive. Employees have noted the dramatic reduction in programming time and the enhanced consistency in the quality of robotic welds, leading to a more efficient production line and improved job satisfaction.
Quantifying the impact
The impact of Visual Components Robotics OLP on Berlin Gardens’ operations can be quantified by remarkable efficiency gains and cost savings. Programming processes that once took days now take mere minutes. For example, programming a complex fixture that previously required a full 13 hours to get into production can now be completed in under 3 hours. An 80% reduction in programming time! This drastic reduction in programming time has not only led to significant labor savings but has also enhanced the overall operational agility of the company. Looking ahead, Berlin Gardens is enthusiastic about further utilizing Visual Components Robotics OLP in its operations. The company is exploring potential expansions in areas where automation can enhance efficiency even further.
Just for example one of our fixtures would have taken a full 13 hours of programming to be ready for fabrication but with the software we can be up and running within 3 hours. That gives you a small glimpse into the labor saved not to mention the efficiency of how the program then runs.
Derrick Yoder, Aluminum Production Manager at Berlin Gardens
Berlin Gardens’ case study is a compelling example of how a company can successfully integrate modern technology into traditional craftsmanship. By embracing technological innovation and maintaining core values, Berlin Gardens has not only enhanced its operational efficiency but has also solidified its position as a leader in the outdoor furniture industry.
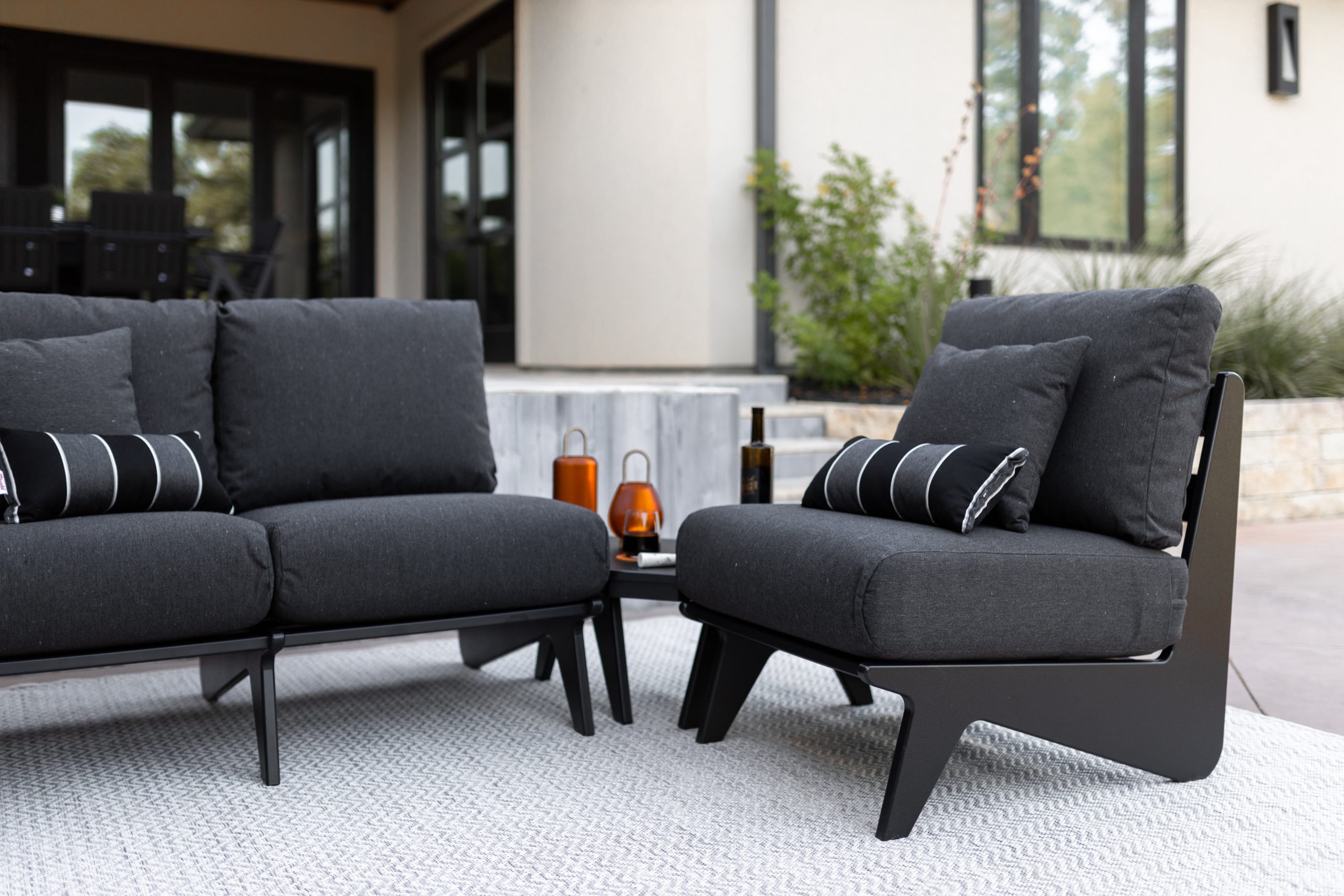
About Visual Components
Founded by a team of simulation experts and amassing over 20 years in business, Visual Components is one of the pioneers of the 3D manufacturing simulation industry. The organization is a trusted technology partner to a number of leading brands, offering machine builders, system integrators, and manufacturers a simple, quick, and cost-effective solution to design and simulate production processes and offline robot programming (OLP) technology for fast, accurate, and error-free programming of industrial robots.
Want to learn more about the benefits of our solutions for your business? Contact us today!
Further reading
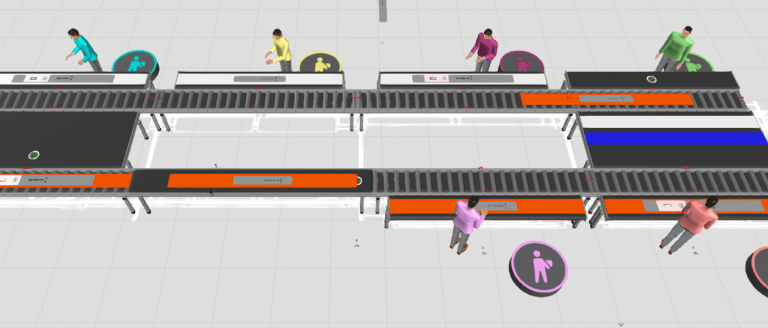
Elevating assembly planning for elevator button panels at KONE with 3D simulation
Planning a new assembly line for two product variants, KONE’s Northern Italy site needed to ensure smooth flow and minimal risk of defects. With Visual Components, they simulated and tested...
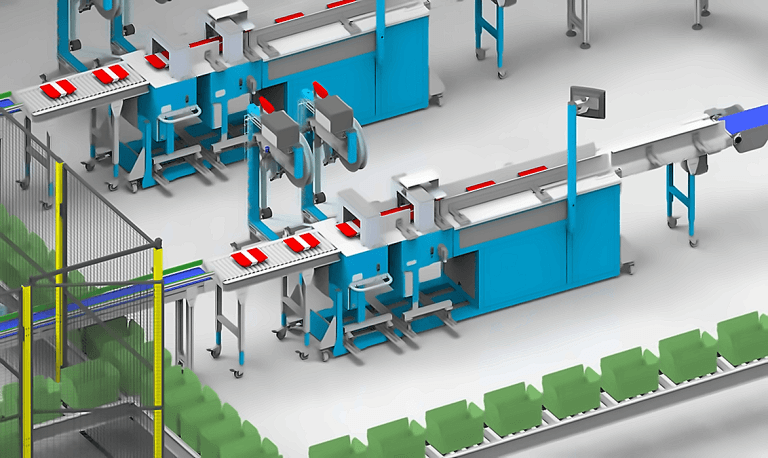
How Hollander Techniek designed an automated custom meal packaging system with Visual Components
When Uitgekookt set out to automate its meal packaging process, they needed a system that could handle custom orders with speed and precision. Hollander Techniek used Visual Components to design...
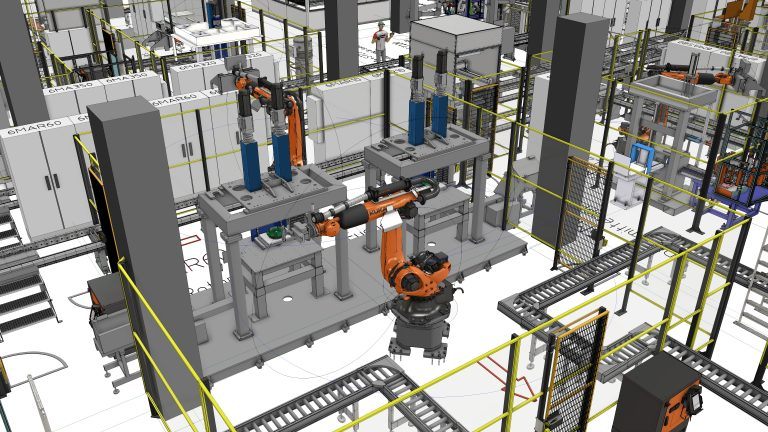
How EMIL SCHMID MASCHINENBAU designed a high-speed battery assembly plant with Visual Components
Facing the challenge of designing a fully automated battery assembly plant for a customer, EMIL SCHMID MASCHINENBAU turned to Visual Components. With 3D simulation and an extensive library of factory...