Automating robot offline programming with Visual Components OLP software
From one-click programming to fully automated use of model-based definition (MBD), Visual Components OLP software leverages product manufacturing information (PMI) to streamline workflows, eliminate manual robot programming, reduce errors and accelerate production. This enhances collaboration and efficiency throughout product design and manufacturing.
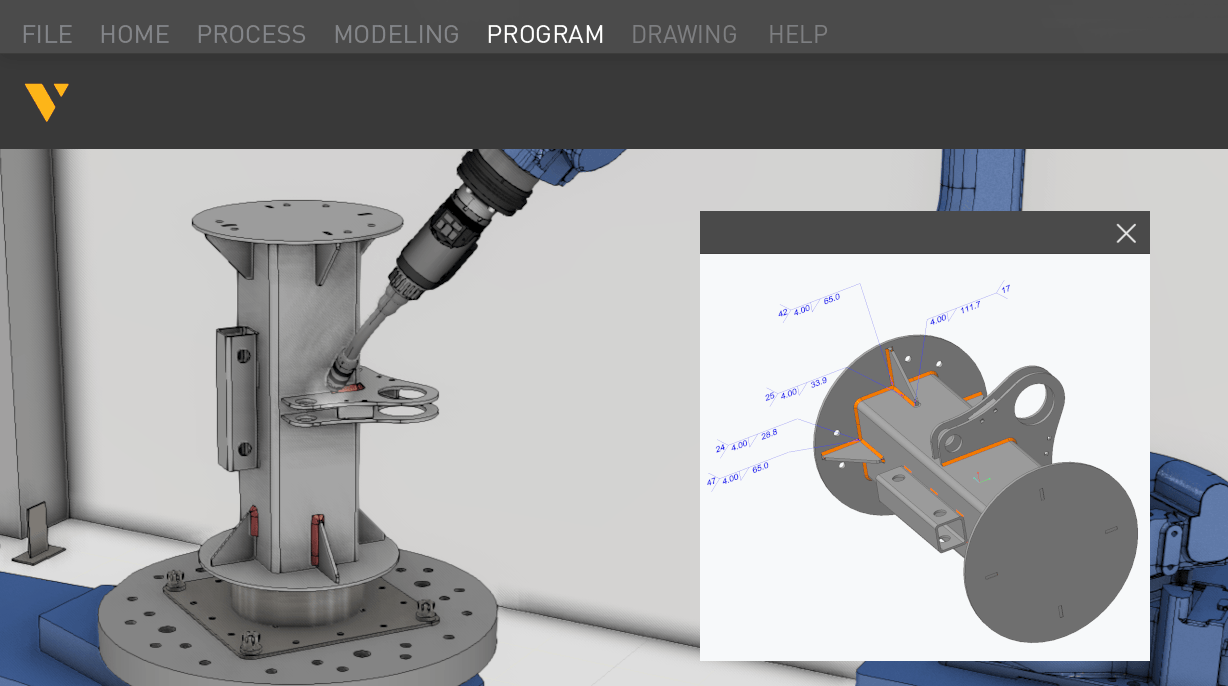
Bridging the gap between product design and manufacturing
In many manufacturing environments, product design and production operate in silos. A product is designed, sent to manufacturing and only then do feasibility issues arise—leading to costly redesigns and delays. Slow feedback loops make it difficult to catch problems early, often resulting in last-minute adjustments and rework.
Robot offline programming (OLP) software bridges this gap by enabling collaboration between design, fixture development and manufacturing before production begins. Visual Components OLP software ensures that product manufacturing information (PMI) is not just stored but actively used to streamline workflows, improve accuracy and accelerate production.
By integrating PMI directly into the automation process, our software clarifies engineering intent, tolerances and process requirements from the start. Whether you’re automating a single task or implementing a digital workflow, Visual Components OLP software supports manufacturers at every level—from one-click programming to fully automated use of model-based definition (MBD).
Let’s explore how Visual Components OLP software supports different levels of automation in manufacturing by leveraging PMI and MBD to enhance efficiency at each stage.
Level 1: Getting started with one-click programming
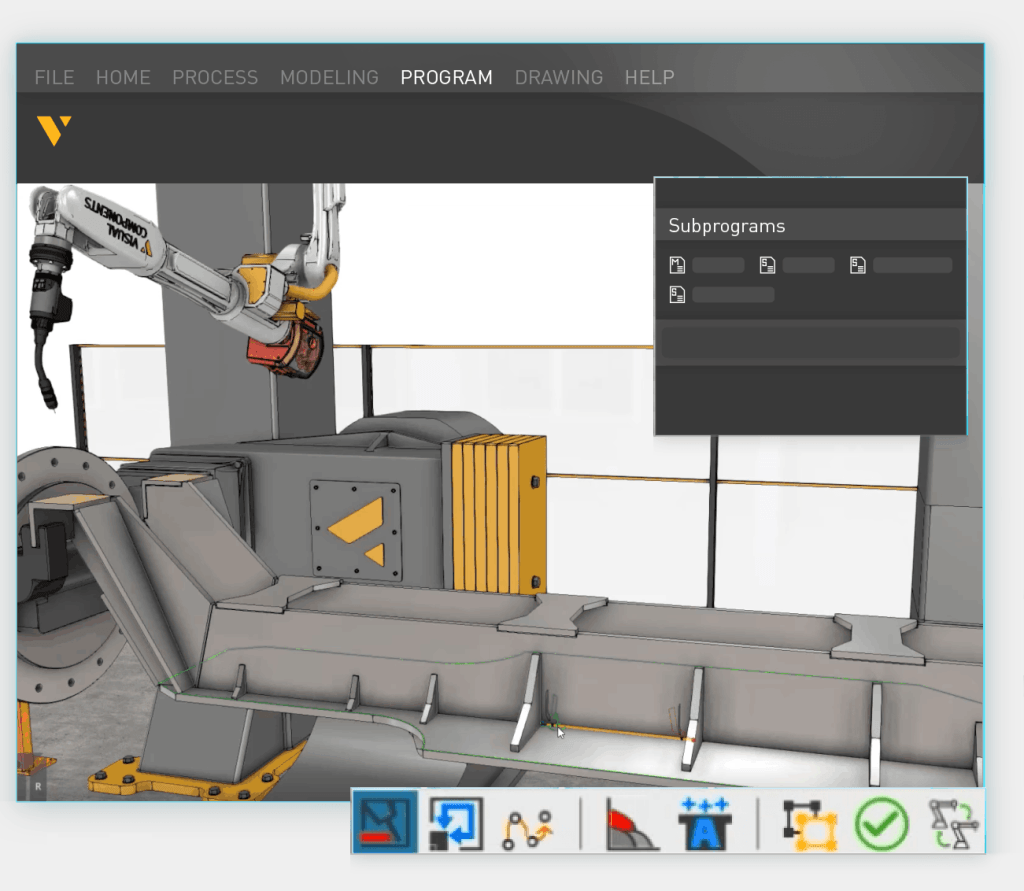
If you’re in the early stages of automation, your goal is probably to reduce manual robot programming without overcomplicating things. One-click programming is a great way to quickly generate programs. At this stage, having CAD models with basic geometric data, predefined toolpaths for common operations and standard process parameters for tasks like welding or cutting is crucial.
One-click programming is a feature within automated programming, designed for ease of use and accessibility. It allows users to generate robot programs with minimal input, making it ideal for early-stage automation where simplicity is key. While more advanced automation levels leverage rule-based programming and digital workflows, one-click programming provides a fast and efficient starting point.
Level 2: Rule-based automation for more efficiency
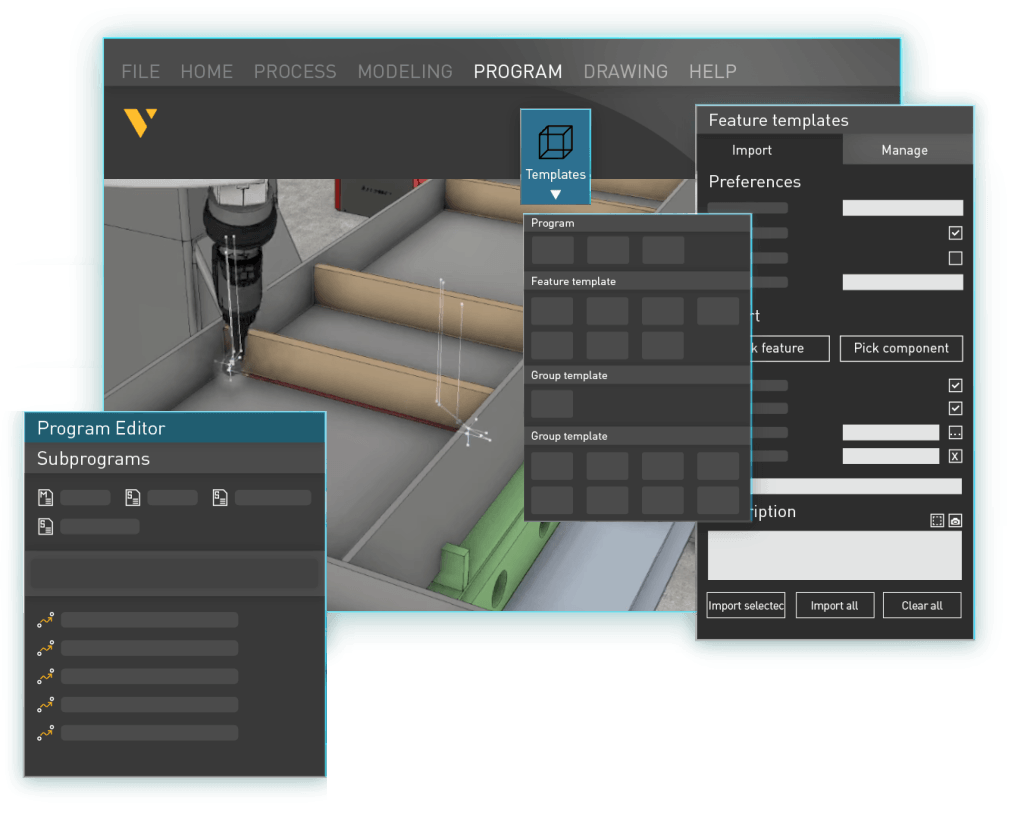
Once you’ve got the basics down, the next step is to make automation smarter. Rule-based automation allows manufacturers to apply standard rules to similar parts, saving time and reducing variability. To make this work, you need feature-based models that define key elements like holes, slots and weld seams, along with predefined manufacturing rules and logic.
Visual Components OLP software enhances rule-based automation by identifying features from CAD models and applying standardized predefined manufacturing parameters. This reduces the time spent on manual weld path creation and ensures consistent weld programming across parts.
By aligning welding paths, cutting strategies and fixture setups with engineering intent, the software minimizes manual adjustments and enforces process consistency, boosting efficiency without compromising quality.
Level 3: Going fully digital with model-based definition (MBD)
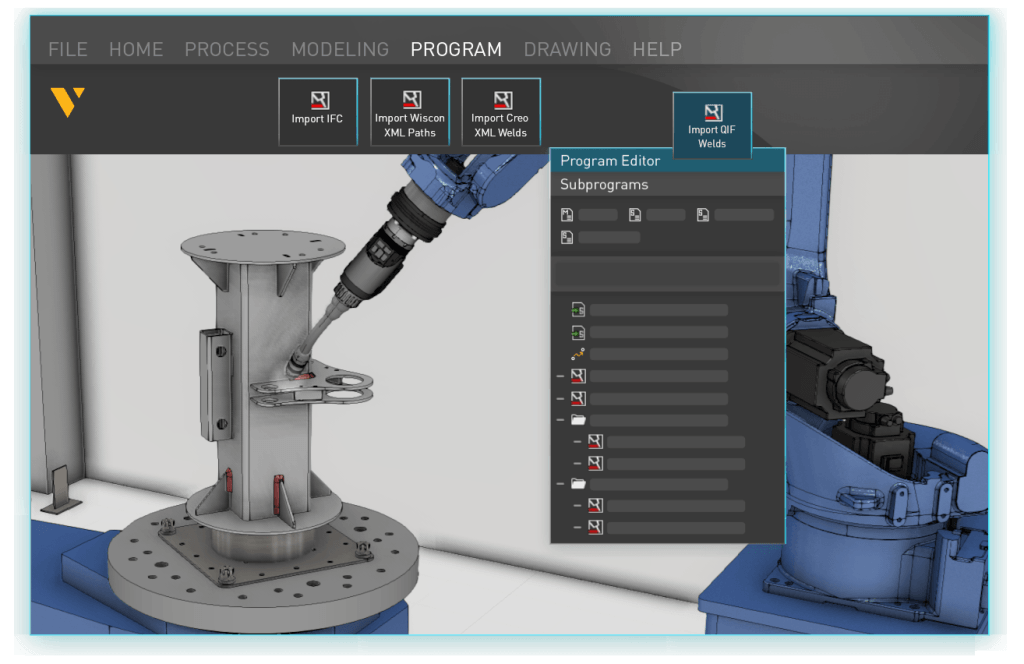
At this level, manufacturers replace traditional 2D drawings with fully annotated 3D models that contain all the data needed to manufacture a part. This is known as model–based definition (MBD). By embedding product manufacturing information (PMI)—such as weld symbols, tolerances, materials and process notes—directly into the CAD model, MBD creates a single, authoritative source of truth across design and production.
Visual Components OLP software makes this model-driven workflow practical and efficient. The software extracts PMI from companion files or embedded metadata in supported CAD formats to generate robot toolpaths, eliminating the need for manual input. Weld sizes, positions and joint types are applied directly from the design data, which reduces programming time, minimizes interpretation errors and ensures consistent execution.
Because Visual Components supports all major robot brands, it offers flexibility without locking users into specific hardware. Teams can standardize their automation processes across mixed robot fleets—whether they’re just beginning with robotics or scaling up existing operations.
In the fully digital phase, advanced features like collision detection and adaptive path solving come into play. The software identifies potential clashes and ensures robot motion is both safe and efficient. Integration with real-world sensors—such as cameras, laser scanners and force-torque sensors—lets the system validate part positioning and dynamically apply offsets. This sense and adjust capability helps account for real-world deviations from CAD, improving quality and reducing the need for manual corrections on the shop floor.
The result is faster, more accurate robot programming that aligns seamlessly with your digital design intent—paving the way for scalable, high-quality production.
Ready to take the next step in robot offline programming automation?
No matter where you are in your automation journey, having the right tools makes all the difference. Visual Components OLP software enables high-level automation in robot offline programming—helping manufacturers move beyond manual programming to fully digital workflows.
By leveraging PMI and MBD, you can streamline robot programming, improve accuracy and eliminate manual processes. With the right automation strategy, you’ll improve collaboration, reduce errors and future-proof your production.
Want to know how Visual Components OLP software can support your automation journey? Let’s talk.
Further reading
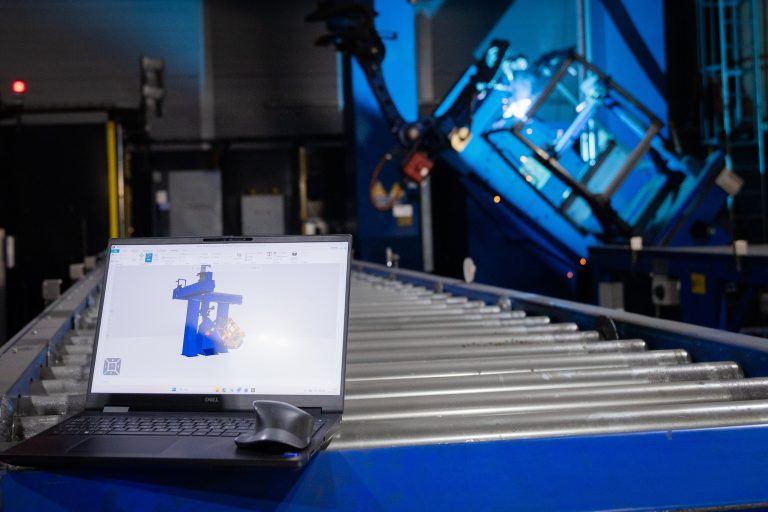
How offline programming software improves robotic welding efficiency
Offline programming software makes robotic welding more efficient by enabling manufacturers to create and optimize robot programs directly in a digital environment. It supports a wide range of processes including...
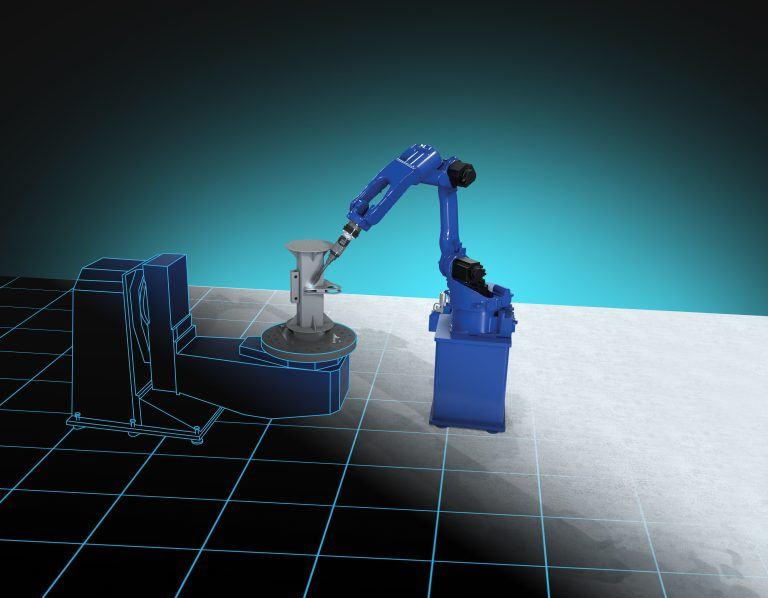
Next-level robot offline programming automation with model-based engineering
Explore how model-based engineering enables the next level of robot offline programming automation by connecting design and manufacturing through model-based definition. With validated manufacturing data exported via Capvidia tools to...
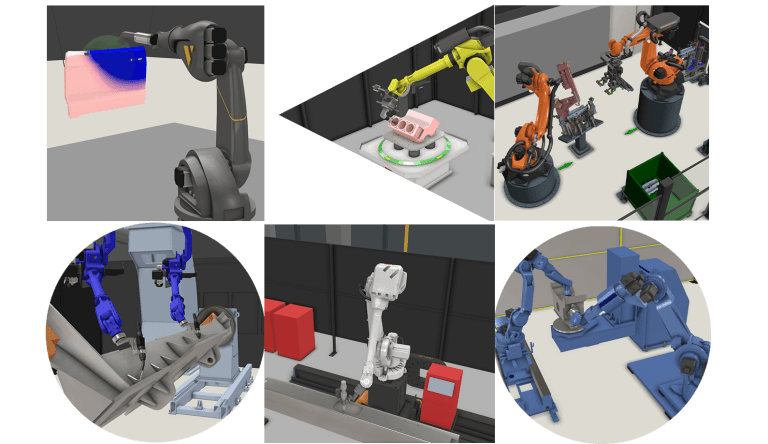
Robot programming for industrial processes with Visual Components OLP software
Robot programming is advancing with offline programming, enabling manufacturers to optimize robotic tasks virtually without disrupting production. This minimizes downtime, improves accuracy and streamlines processes like welding, spraying, processing and...