Wie KOCH Steuerungstechnik mit Visual Components den modularen Anlagen-bau neu definiert
KOCH Steuerungstechnik nutzt Simulation als Rückgrat seines Workflows und begleitet damit jedes Projekt von der ersten Idee bis zur finalen Umsetzung.
Bei der Zusammenarbeit mit HANSWEBER zur Automatisierung einer Bürststation setzte KOCH bereits in der Angebotsphase auf Visual Components. Das Team modellierte Layouts, testete Roboterprogramme, validierte die Systemlogik und führte Designprüfungen in der virtuellen Realität durch.
Lese hier weiter und erfahre, wie die Simulation dieses Projekt vom Konzept bis zur Realisierung maßgeblich unterstützt hat.
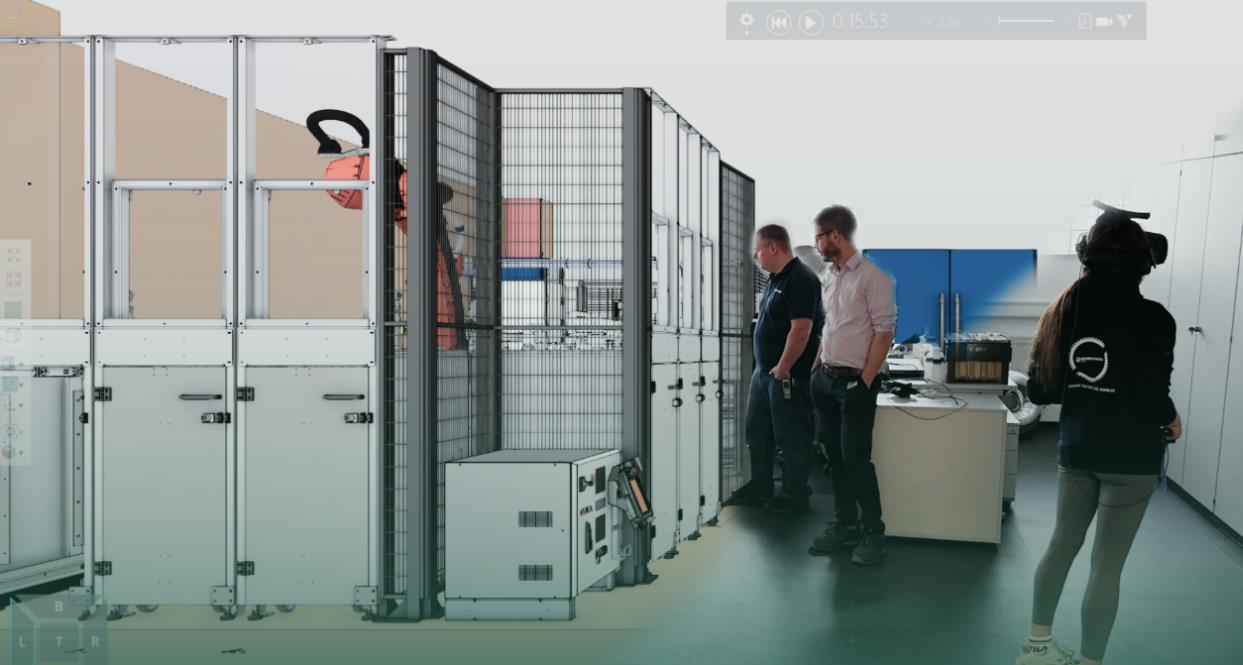
KOCH Steuerungstechnik steht für durchdachte Roboterlösungen im Maschinen¬bau. Von Anfang an setzt das 2021 gegründete Unternehmen aus dem Schwarzwald auf digitale Fabrikplanung mit Visual Components – und das nicht als NiceToHave, sondern als zentrales Werk¬zeug im gesamten Entwicklungsprozess. Ob in der Angebotsphase, bei der Program-mierung oder zur finalen Konstruktions¬freigabe: Der Digitale Zwilling begleitet jedes Projekt von den ersten Ideen bis zur erfolgreichen Inbetrieb¬nahme.
Wie konsequent KOCH diesen Ansatz lebt und welche Vorteile er bietet, zeigt ein aktuelles Projekt zur Entladeautomation einer Bürststation der Hans Weber Maschinen¬fabrik GmbH (kurz: HANSWEBER).
Prozesse neu gedacht: Vom gehärteten verzunderten Zahnrad zum ab-gestapelten Werkstück
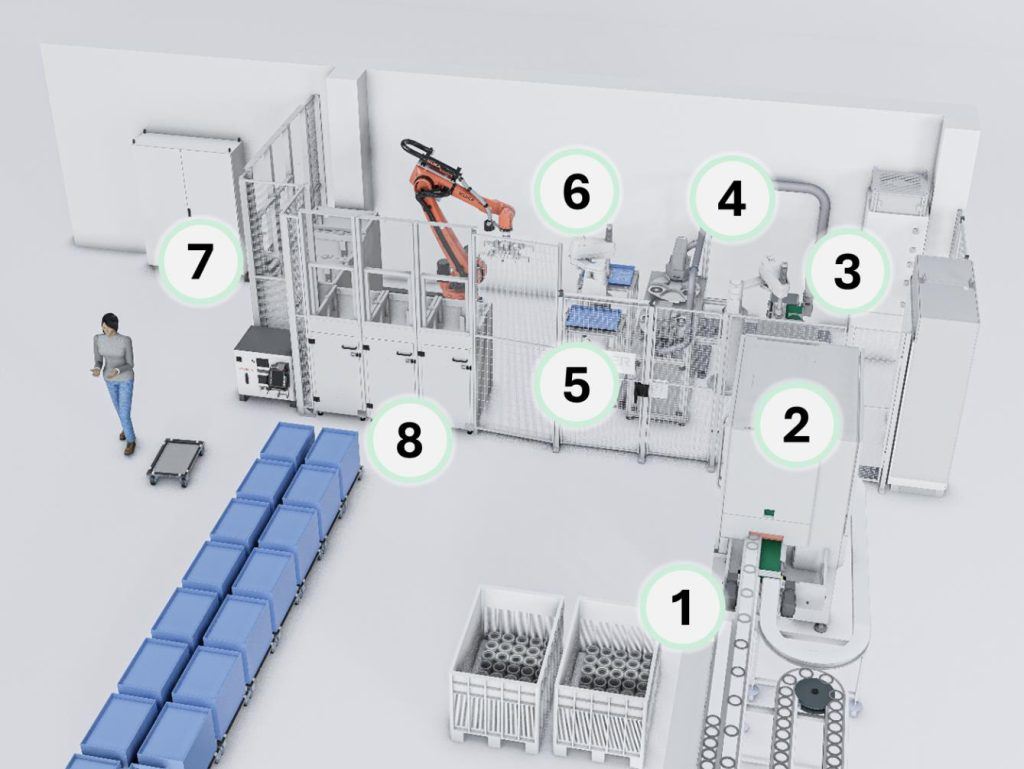
Ein Kunde von KOCH Steuerungstechnik, ein Hersteller von Zahnrad- und Getriebetechnik, setzt in seiner Produktion eine Werkzeug¬maschine des Herstellers HANSWEBER zum Bürsten und Entzundern ein. Die Werkstücke kommen aus dem Härteofen, sind verzundert und mit einer Schmutz¬schicht belegt. Sie werden wie in Abbildung 1 dargestellt manuell aus der Härt¬e-Kiste entnommen und in die Bürst¬station eingelegt (1). Nach dem Bürsten (2) erfolgt die lage¬richtige Ausrichtung der Werkstücke (3), anschließend werden sie durch Lasermarkierung mit einer individuellen ID beschriftet (4) und in Leerkörbe auf zwei Tischen gestapelt (5)(6).
An diesem Punkt setzt die Automation von KOCH Steuerungstechnik ein: Der Entlade¬prozess wird automatisiert. Dabei wird dafür gesorgt, dass die bearbeiteten und markierten Werk¬stücke für die weitere Bearbeitung in Schächten innerhalb vom Drahtkörben abgelegt werden (7)(8).
Die besondere Herausforderung: Aus der Werkzeugmaschine (Bürststation) kommt alle zwei bis drei Sekunden ein neues Werk¬stück. Das bedeutet: Auf engstem Raum muss ein reibungs¬loser, taktzeitoptimierter Ablauf garantiert sein.
Simulation ab Tag eins: Wie der Digitale Zwilling entsteht
Schon in der Angebotsphase beginnt KOCH mit dem Aufbau eines Digitalen Zwillings. Georg Schepers, kaufmännischer Geschäftsführer und verantwortlich für den technischen Vertrieb, modelliert auf Basis der firmeneigenen Visual Components-Bibliotheken eine erste Lösung. Obwohl er nicht über eine technische Ausbildung verfügt, kann er ein funktionales Simulationsmodell erstellen, das dem finalen Roboterzellenlayout zu rund 80% entspricht. Ermöglicht wird dies durch einen systematisch aufgebauten Pool aus modularen Teilsystemen mit definierten Schnitt¬stellen.
Hierbei geht es nicht nur um die Roboterbewegungen. KOCH betrachtet den gesamten Material¬fluss – vom vorherigen Prozess (Härten) bis zur Weiterverarbeitung nach dem Bürsten. In der Simulation werden deshalb auch die Maschinenbediener dargestellt: Wann müssen sie Material holen? Wie oft fahren sie Leerkörbe durch die Halle? Welche Wege der Maschinenbediener ver¬ursachen Engpässe?
In einem Digitalen Zwilling lassen sich verschiedenste Szenarien einfach durchspielen. So zeigte sich etwa, dass weniger Schächte am Ende zu einem besseren Ergebnis führten: Weniger Trans¬porte bedeuten mehr Effizienz. Diese Erkenntnisse fließen bereits in die Angebotsphase ein – ein echter Vorteil für den Kunden, der von Anfang an weiß, was ihn erwartet.
Virtuelle und physische Produkt-Validierung im Maschinenbau – Institut für Produkt und Service Engineering der Hochschule Furtwangen und KOCH gehen neue Wege
Dabei basiert die Modellbildung des Digitalen Zwillings auf dem X-in-the-Loop-Ansatz. Für die Entwicklung von modernen Automatisierungslösungen muss ein I¬ngenieur in der frühen Phase der Produktentwicklung in der Lage sein, einzelne Teil¬systeme, trotz des fehlenden Gesamt¬systems, in einer systemnahen Umgebung testen zu können.
Des Weiteren erfordern die hochkomplexen Funktions¬vernetzungen, das Zusammen¬wirken von mechanischen, elektrischen und informations¬technischen Kom¬ponenten in den heutigen Automatisierungen systematische und komplexe integrative Ent¬wicklungs¬prozesse und Entwicklungs¬umgebungen. Hierbei muss die Validierung und nicht nur Verifizierung von Anfang an und kontinuierlich über die Entwicklung hinweg syste¬matisch durchgeführt werden. Der Grund¬gedanke ist, dass durch eine kontinuierliche Validierung im Entwicklungsprozess ein steter Abgleich zwischen den Zielen und Zwecken des Produktes sowie dem jeweils erreichten Entwicklungs-stand durchgeführt wird. So¬mit¬ steuert die Validierungs¬aktivität den kompletten Produkt-entstehungs¬prozess, trägt erheblich zum Wissens¬gewinn bei und regt immer wieder neue kreative Lösungen an.
Eine mögliche Lösung des X-in-the-Loop-Ansatzes für die Validierung eines Teil¬systems, in diesem Fall die Roboterzelle zum Entladen der Bürstmaschine, wird in der folgenden Abbildung durch zwei überlagerte Layer a) und b) dargestellt. Die Layer zeigen jeweils die virtuelle und die physischen Ausprägungen des Systems in Development (SiD) und des Connected Systems (Restsystems).
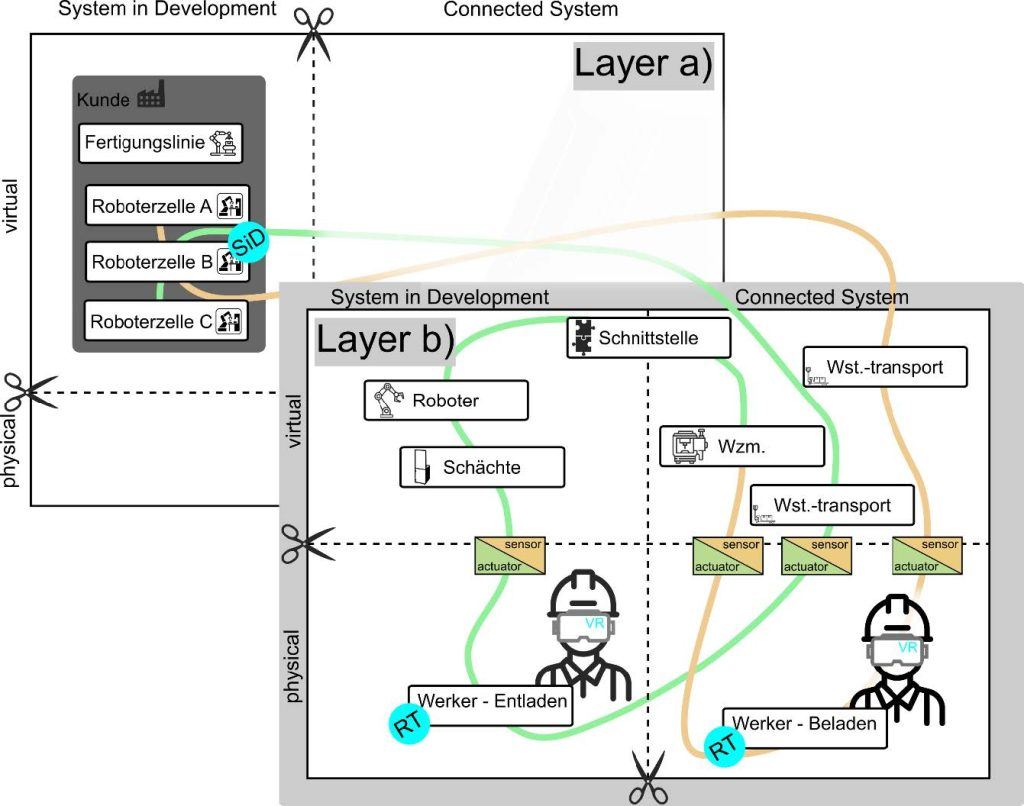
Der Layer a) zeigt die Fertigungslinie des Kunden mit zwei bestehenden Roboter¬zellen (A) und (C), vgl. Abbildung 2. Zwischen die beiden bestehenden Roboterzellen soll die neue Roboter-zelle für das Bürsten integriert werden. Wie die Abbildung zeigt, wird eine gesamt¬heit¬liche Validierung angestrebt. In der Simulation wird nicht nur die Roboterzelle, sondern der Werk-stück¬transport über die gesamte Fertigungs¬linie, hier repräsentativ, von der vorherigen Roboter-zelle (A) zur nach¬folgenden Roboter¬zelle (B), inklusive der Bürstmaschine und ihren gekoppelten Teil¬systemen betrachtet.
Im Layer b) wird die Roboterzelle mit der Bürstmaschine im Detail analysiert. Der Werk¬stück-transport zur Werkzeugmaschine (1) und das Beladen ist ein Teil des virtuellen und physischen Rest¬systems, welcher in der Simulation über das Process Modeling in Visual Components und mittels Virtual Reality abgebildet wird. Über Sensoren und Aktuatoren in der Simulation kann mit der Bürst¬maschine physisch interagiert und die Bürstmaschine mit Werk¬stücken beladen werden.
Der Werkstücktransport in der Bürstmaschine (2), die Lage¬prüfung (3), das Beschriften (4) und das Stapeln der Werkstücke in Leerkörbe (5)(6) wird ebenfalls über Process Modelling abgebildet. Zwischen der Werkzeug¬maschine und dem Roboter wird die Logik der Schnitt¬stelle zwischen den beiden Robotern verifiziert.
Der Roboter, welcher aus den Schächten Leerkörbe entnimmt (7) und die Drahtkörbe mit den Fertig¬teilen in Schächte stapelt (8) ist das SiD (System in Development) in der virtuellen Domäne. Zur vollständigen Betrachtung ist nicht nur die Schnittstelle zur Bürstmaschine in der Simulation abgebildet, sondern auch alle notwendigen Sensoren und Aktuatoren, die dem Roboter zur Verfügung stehen. Somit kann zum Beispiel über die Gabellichtschranken am Korbgreifer das Roboter¬programm für das Eintauchen in den Schacht verifiziert werden. Der Roboter taucht mit seinem Korbgreifer so lange in den Schacht ein, bis über einen geschalteten Interrupt ein Korb detektiert wird. Der Roboter wird in Visual Components über das KUKA.Sim AddOn konfiguriert und programmiert.
Ein Maschinenbediener, der die Roboterzelle sowohl mit Leerkörben belädt (7) als auch die Körbe mit den gebürsteten Fertigteilen entlädt (8), interagiert mit Sensoren und Aktuatoren mittels Virtual Reality mit der Roboterzelle, zum Beispiel über das implementierte Human Machine Interface (HMI). Der Werkstück¬transport zur nachfolgenden Roboterzelle (C) ist wieder Teil des virtuellen Restsystems und wird über das Process Modelling in Visual Components abgebildet.
Über den X-in-the-Loop-Ansatz kann somit die Roboterzelle in einem gesamtheitlichen Kontext mit den Wechselwirkungen zu anderen interagierenden Teilsystemen validiert werden. Dies ermöglicht KOCH in der frühen Phase der Produkt¬ent¬wicklung einzelne Teil¬systeme, trotz des fehlenden Gesamt¬systems, in einer system¬nahen Umgebung testen zu können!
Vom virtuellen Modell zur realen Roboterbewegung
Im Verlauf des Projekts entwickelt sich der Digitale Zwilling ständig weiter. Neue Werkstücke, alternative Szenarien und optimierte Abläufe werden integriert, bis das Modell stabil ist und in die Umsetzung übergeht.
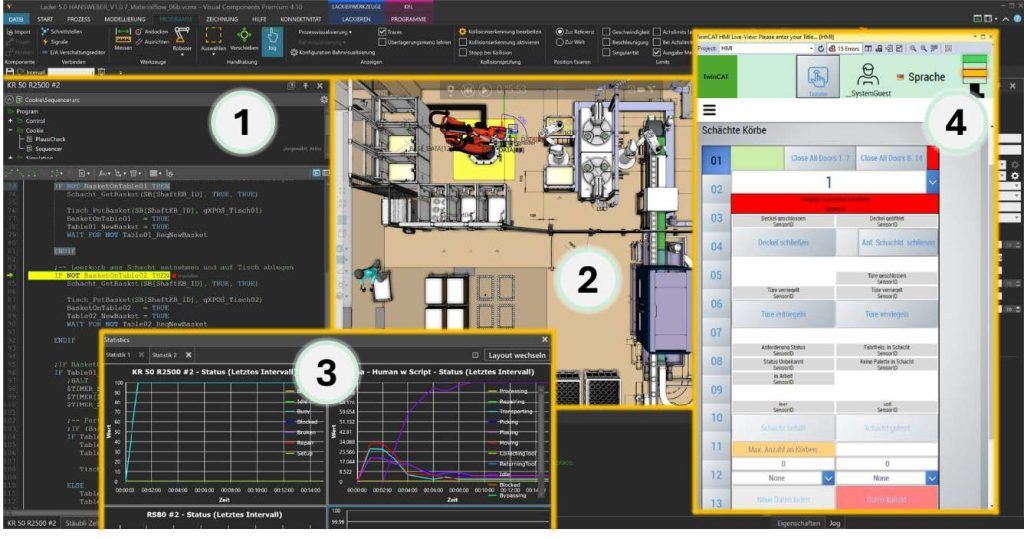
Roboterprogramme werden innerhalb von Visual Components finalisiert, Be¬wegungs¬abläufe definiert und Schnittstellen verifiziert. In komplexeren Projekten wie etwa einem 3-Schacht-Lader¬system wird die Simulation mit BECKHOFF TwinCAT gekoppelt, um NC-Achsen in Verbindung mit Sensorik und Aktuatorik realitätsnah zu testen. Die NC liefert Soll-Positionen, die in der Simulation übernommen und geprüft werden. Auch die HMI wird in die Simulation ein-ge¬bunden: Per Webbrowser kann die Bedienoberfläche im digitalen Modell ange¬zeigt und getestet werden. So entsteht eine ganzheitliche Betrachtung der Roboterzelle, lange bevor das erste reale Bauteil gefertigt ist.
Abbildung 3 zeigt die Simulationsumgebung Visual Components. Auf der linken Seite ist das Fenster für das KUKA.Sim Addon (1) dargestellt. Mit Hilfe von KUKA.Sim kann ein Roboter konfiguriert und in der KUKA Robot Language (KRL) programmiert werden. Mittig ist das Gesamt-layout Automation – Bürstmaschine mit Roboterzelle dargestellt (2). Mittig unten ist das Fenster für die Analyse der einzelnen Roboter, der Werkzeugmaschinen und der Maschinen¬bediener (3). Über die Charts können Aussagen getroffen werden, wie die einzelnen Teil¬systeme ausgelastet sind, welche Auswirkungen Pausenzeiten haben oder wie sich eine Störung auf den gesamten Materialfluss auswirken kann. Auf der rechten Seite kann über BECKHOFF TE2000 (4) mit der Simulation interagiert werden, um zum Beispiel die Bedien¬barkeit zu validieren.
Freigabe in der virtuellen Welt – mit allen Beteiligten
Ein zentrales Element der Projektmethodik bei KOCH ist die interaktive Konstruktions¬freigabe mittels Virtual Reality (VR). Statt zweidimensionaler Zeichnungen taucht der Kunde in eine begehbare VR-Welt ein. Dort kann er Laufwege kontrollieren, Sichtlinien prüfen oder zum Beispiel auch Sicherheitsabstände verifizieren.
Wichtig ist die Beteiligung aller relevanten Personen: Werksleitung, Instandhaltung, Projekt-verantwortliche und auch die künftigen Maschinenbediener erleben die Anlage aus ihrer jeweiligen Perspektive. Und sie geben wertvolles Feedback – etwa zu Positionen von Kabel-rinnen, Fluchtwegen oder ergonomisch ungünstigen Details. Diese Hinweise fließen in das Modell ein. So entsteht eine Lösung, die in der Praxis funktioniert und alle Beteiligten mitnimmt.
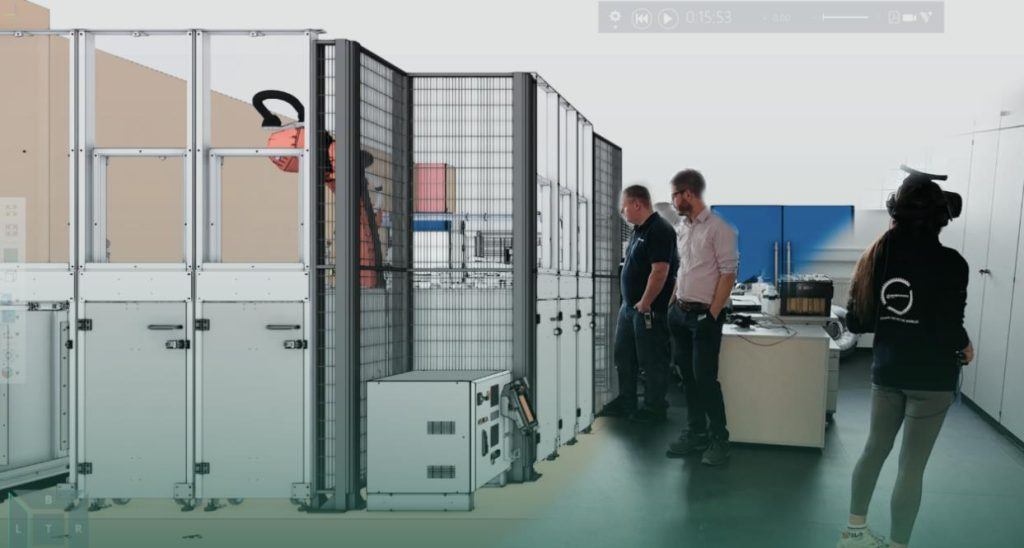
Inbetriebnahme auf Knopfdruck
Wenn die reale Anlage aufgebaut ist, wird das in Visual Components entwickelte Roboter-programm auf die Robotersteuerung übertragen. Christian Koch, Inhaber und ver¬antwortlich für alle technischen Themen, spielt die Bewegungsprogramme direkt ein. Dank der realitäts¬nahen Simulation verläuft die Inbetriebnahme schnell und reibungslos. Wo früher tage¬lang vor Ort programmiert werden musste, reichen heute oft wenige Stunden. Die Kunden profitieren nicht nur von der Geschwindigkeit, sondern auch von der Sicherheit, dass die Anlage exakt das leistet, was im Vorfeld definiert wurde. Unerwartete Probleme? Fehlanzeige.
Mehr als ein Tool: Simulation als Grundprinzip
Für KOCH Steuerungstechnik ist Simulation kein optionales Hilfsmittel, sondern grund¬legender Bestandteil des gesamten Engineering Prozesses. Das Unternehmen kennt das „Old Normal“ – also Anlagenbau ohne Digitalen Zwilling – schlicht nicht. Seit Gründung ist Visual Components im Einsatz und hat sich als unverzichtbares Werkzeug etabliert. Digitaler Zwilling ist das „New Normal“ bei KOCH – und zwar nicht aus einem Innovationsanspruch heraus, sondern aus Überzeugung und Erfahrung.
„Ich frage mich eher, wie Leute das nicht einsetzen können – und sich dann wundern, wieso ihre Projekte nicht profitabel abschließbar sind“, sagt Georg Schepers. „Wir haben das noch nie anders gemacht. Und ich kann mir auch nicht vorstellen, wie man das ohne Simulation macht – das Risiko ist ja immens!
Zukunft inklusive: Fernzugriff vom Digitalen Zwilling auf Kundensysteme
Schon heute plant KOCH den nächsten Schritt: die Einbindung von Echtzeitdaten in den Digitalen Zwilling. Ziel ist, bei Serviceeinsätzen aus der Ferne überprüfen zu können, in welchem Zustand sich Roboter, NC-Achsen, Sensoren und Aktuatoren befinden. Eine „Echtzeit“-Daten-synchronisation zwischen Kundensystem und dem Digitalen Zwilling via Fern¬zugriff könnte nicht nur Support-Anfragen effizienter gestalten, sondern langfristig auch die Verfüg¬barkeit von Produktionsanlagen steigern.
Fazit: Simulation als Wettbewerbsvorteil
Das Projekt der HANSWEBER-Automation war mit einer Laufzeit von sechs Monaten kein Sonder¬fall. Im Gegenteil: Es steht exemplarisch für den Standardprozess bei KOCH. Was wie ein Geheimrezept klingt, basiert auf zwei klaren Prinzipien: modularer Anlagenbau und konsequente Simulation. Gemeinsam sorgen sie dafür, dass KOCH Steuerungs¬technik Anlagen realisiert, die technisch überzeugen, wirtschaftlich funktionieren und die Kunden begeistern. Visual Components ist dabei nicht nur Software, sondern Teil der Unternehmens-DNA.
Über Visual Components
Visual Components wurde von einem Team von Simulationsexperten gegründet und ist mit über 25 Jahren Erfahrung einer der Pioniere der 3D-Fertigungssimulation. Das Unternehmen ist ein zuverlässiger Technologiepartner zahlreicher führender Marken und bietet Maschinenbauern, Systemintegratoren und Herstellern eine einfache, schnelle und kostengünstige Lösung für die Planung und Simulation von Produktionsprozessen und die Offline-Roboter-Programmierung (OLP) für eine schnelle, genaue und fehlerfreie Programmierung von Industrierobotern.
Kontaktiere uns noch heute, um zu erfahren, wie unsere Lösungen deinem Unternehmen helfen können.
Zum Weiterlesen
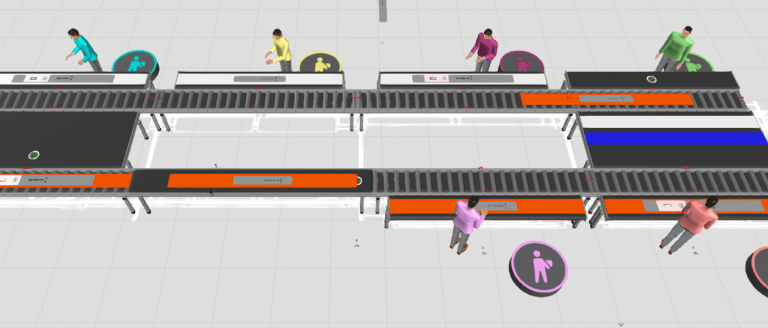
Wie KONE die Montageplanung von Aufzugstableaus durch 3D-Simulation verbessert
Bei der Planung eines neuen Montagebands für zwei Produktvarianten musste der norditalienische Standort von KONE einen reibungslosen Ablauf und ein minimales Fehlerrisiko sicherstellen. Mit Visual Components simulierten und testeten sie...
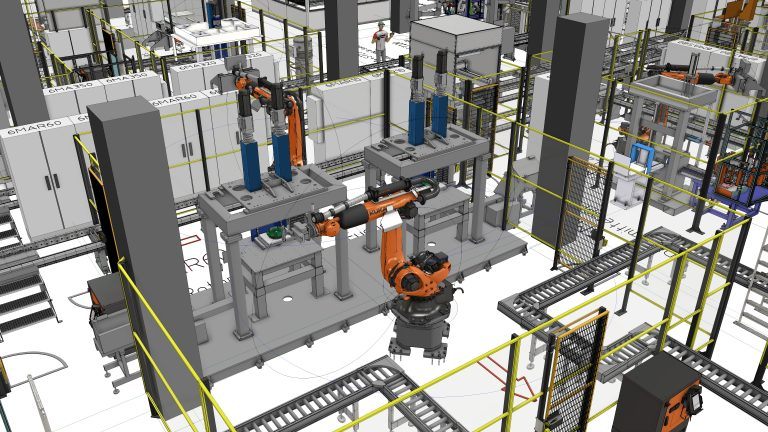
Ein Hidden Champion setzt auf Visual Components
Um die Herausforderung der Entwicklung einer vollautomatischen Batteriemontageanlage zu meistern, wandte sich EMIL SCHMID MASCHINENBAU an Visual Components. Mit 3D-Simulation und einer umfangreichen Bibliothek von Fabrikkomponenten half Visual Components dem...
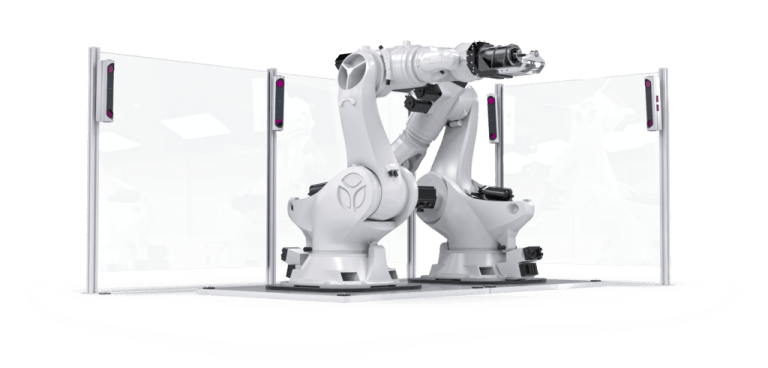
INSPHERE steigerte mit Visual Components den Umsatz und festigte das Kundenvertrauen
INSPHERE, ein führender Anbieter im Bereich fortschrittlicher Messtechniklösungen und hat sich der Verbesserung von Präzision und Effizienz in der automatisierten Fertigung verschrieben. Mit ihrem innovativen IONA-System erfüllen sie den Bedarf...