Fallstudie: Projekt für IAS – Automatisierung einer Saatgut-Prüflinie
Der führende Systemintegrator IAS Inc. (aus Wisconsin, USA) konnte mithilfe von Visual Components eine vollautomatische Saatgut-Prüflinie konzipieren und verkaufen.
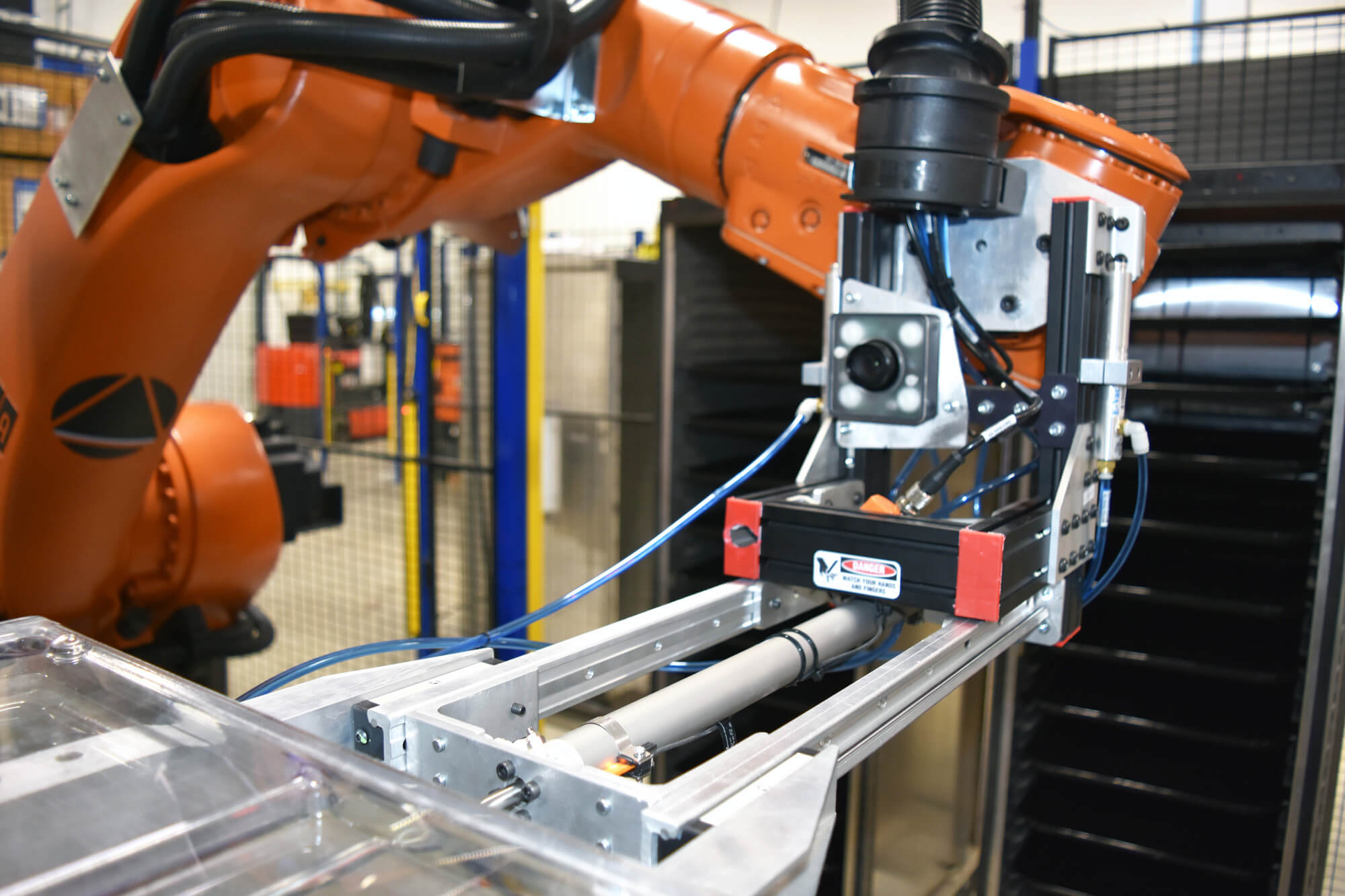
IAS Inc., ein Systemintegrator aus den USA und Kunde von Visual Components, hat uns kürzlich von einem besonderen Projekt für ein Agrarunternehmen der amerikanischen Fortune-500-Liste berichtet. Dabei ging es um die Automatisierung einer Saatgut-Prüflinie.
„Bisher war ein Team von über 100 Personen mit diesem Verfahren beschäftigt, wobei jede einzelne Person alle Vorbereitungsschritte für den Testzyklus durchführen musste“, erklärt Kyle Weise, Marketing Director bei IAS. „Dazu zählten auch langwierige und mühsame Arbeitsschritte wie das Vorbereiten von Wannen, das Auftragen des Saatguts und das manuelle Erfassen von Wannen- und Saatgutdaten.“
Zuerst ging es nur darum, eine einzelne Aufgabe automatisieren, aber bald nahm das viel Projekt größere Dimensionen an: Die gesamte Saatgut-Prüflinie sollte automatisiert werden. Die Zielsetzung wurde schnell komplexer und vielfältiger.
„Der Kunde setzte bisher Zeitarbeitskräfte nach minimaler Einarbeitung ein”, erzählt Kyle Weise. „Er beklagte sich über Qualitätsprobleme, hohe Fluktuationsraten und hohe Lohnkosten.“
Außerdem gab es Probleme mit der Datenintegrität. Der Kunde wollte sicher sein, dass die von jeder Saatgutpartie erfassten und nachverfolgten Daten auch wirklich zuverlässig sind.
Da die Prüfschritte aus vielen Wiederholungen bestanden und strenge Prüfparameter eingehalten werden mussten, bot es sich an, das Verfahren durch Roboterautomatisierung präziser und effizienter zu machen.
Konzipieren der Lösung
Zu Beginn des Projekts besuchte IAS das Saatgut-Prüflabor des Kunden, um mit den Mitarbeitern vor Ort zu sprechen.
„Wir glauben, dass die besten Systeme die internen Prozesse von Unternehmen berücksichtigen“, sagt Kylie Weise. „Zu Beginn eines komplexen Projekts wie diesem treffen wir uns daher zunächst vor Ort mit dem Kunden. Wir lassen uns die bisherigen Arbeitsschritte erklären, fragen nach dem Verbesserungsbedarf und entwickeln auf dieser Grundlage ein besseres System.“
IAS stellte schnell fest, dass alle Bereiche im Prüflabor voneinander abhingen, weswegen es am Anfang ausschlaggebend war, jeden einzelnen Bereich in Module aufzusplitten und eine übergeordnete Architektur zu entwickeln. Auf dieser Grundlage konnten die Ingenieure die einzelnen Arbeitsschritte separieren und gleichzeitig den übergeordneten Prüfrahmen aufrechterhalten.
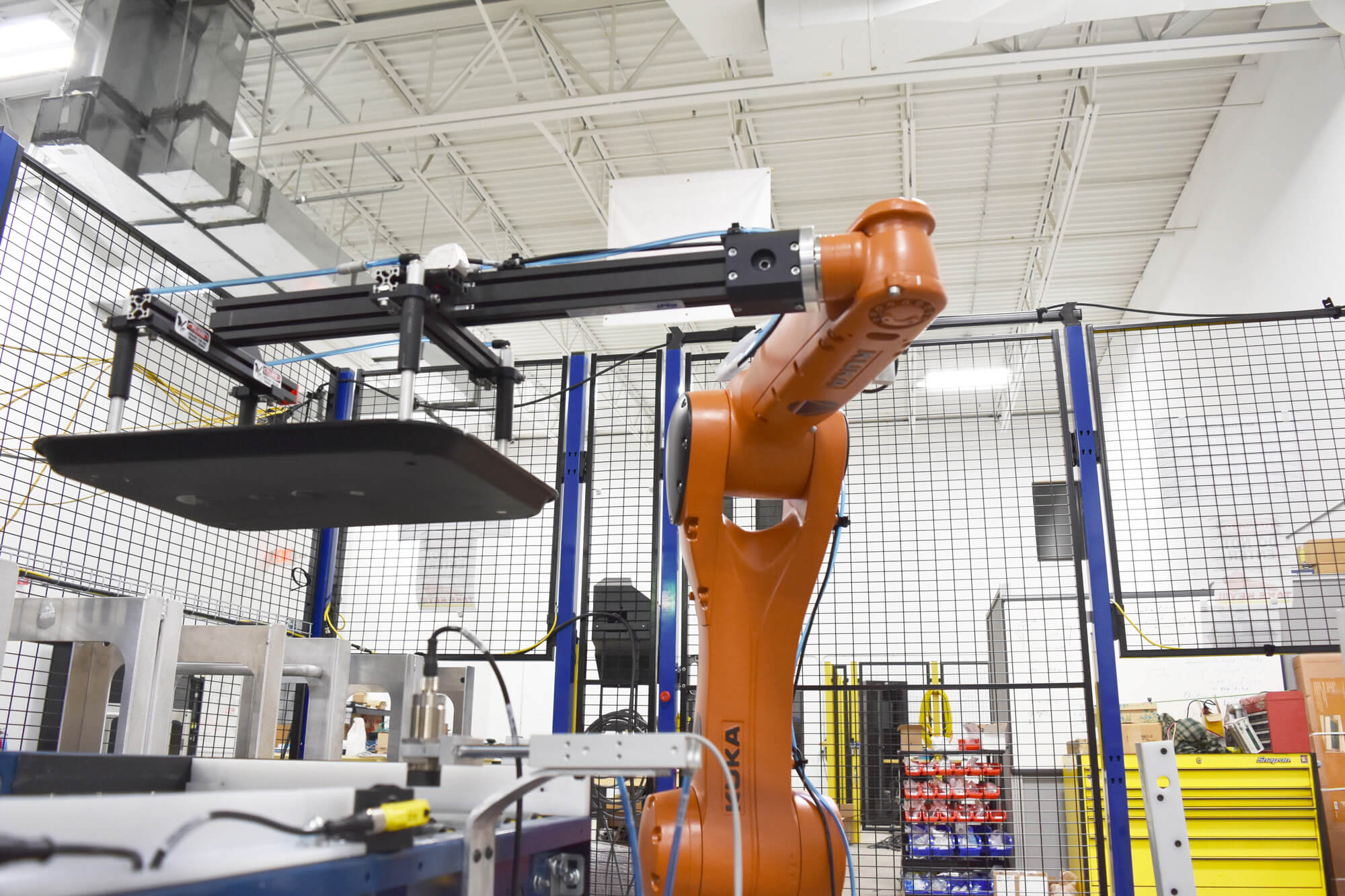
Um dem Kunden den Nutzen des Konzepts unter Beweis zu stellen und zu veranschaulichen, nutzte IAS die 3D-Produktionssimulationssoftware von Visual Components.
„Mit Visual Components konnten wir Layouts erstellen und unsere Entwürfe simulieren und dadurch dem Kunden die kreativen Ideen und Kompetenzen unseres Teams vor Augen führen“, erklärt Kyle Weise.
Visual Components hat auch dabei geholfen, die Kommunikation und den Austausch zu Beginn des Projekts zu optimieren und zu beschleunigen.
„Wir konnten unserem Kunden Simulationen und virtuelle Modelle des Systems zeigen, Feedback von ihm bekommen und schnell Änderungen an den Konstruktionen vornehmen. Das Kundenfeedback ist auf diese Weise effizient und schnell in den Prozess eingeflossen“, sagt Kyle Weise.
„Der Kunde war frühzeitig umfassend darüber informiert, welche Lösung wir für ihn entwickeln, und alle Beteiligten wussten, was zu tun war.“
Mit Visual Components konnten wir Layouts erstellen und unsere Entwürfe simulieren und dadurch dem Kunden die kreativen Ideen und Kompetenzen unseres Teams vor Augen führen.
Kyle Weise, Marketing Director bei IAS
Der Prozess
Die von IAS für dieses Projekt konzipierte Lösung bestand aus sechs Hauptstationen: Entnehmen von Wannen, Entnehmen von Behältern mit Saatgut, Auftragen von Saatgut, Inspektion der Saatgut-Anordung, Stampfen des Saatguts in Position und Beladen der Wagen für den Prüfraum. Der Prozess beginnt an der Station für die Wannen-Entnahme.

„In der Wannen-Entnahmestation entnimmt ein Roboter leere Wannen aus Wagen”, erläutert Kyle Weise. „Die Wannen werden dann für das Saatgut vorbereitet, indem ein Nährstoffgel aufgetragen oder ein feuchtes Blatt Papier in die Wanne gelegt wird. Die Wannen werden anschließend zur Aussaatstation transportiert.“
In der Zwischenzeit werden mit Saatgut gefüllte Gläser einer robotergestützten Station zugeführt, an der ein Roboter die Gläser entnimmt, die Deckel abschraubt und dann auf ein Doppelband setzt. Das Band transportiert die Gläser zu einem weiteren Roboter, der die Gläser anhebt und das Saatgut in ein Dosiersystem schüttet. Die leeren Gläser werden wieder auf die Förderanlage gestellt und wegtransportiert.
An der Aussaatstation trägt ein Dosiersystem das Saatgut gleichmäßig im Muster 10 x 10 auf die Wannen auf. Die Wannen erreichen anschließend eine Inspektionsstation, an der mittels Kameras geprüft wird, ob die Saatanordnung korrekt ist und ob sich fremde Objekte oder beschädigtes Saatgut in den Wannen befinden. Bei Bedarf ersetzt ein Pickroboter fremde Objekte oder beschädigtes Saatgut durch Saatgut aus derselben Partie und ordnet es gemäß dem Muster von 10 x 10 an.
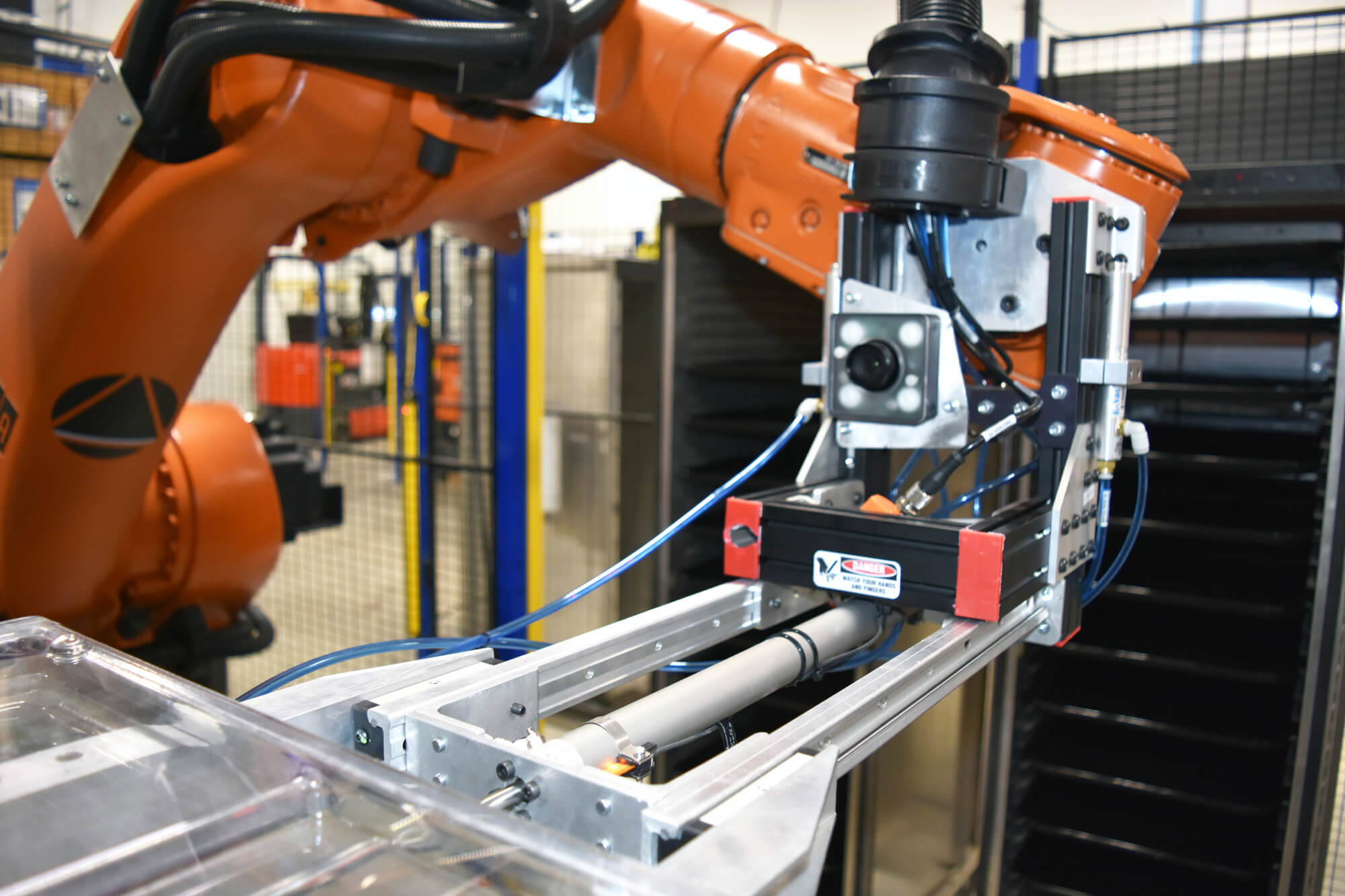
Die Konzeption dieses Inspektionsprozesses war einer der technisch anspruchsvollsten Teile des Projekts.
„Die präzise Inspektion organischer Materialien kann problematisch sein, denn es ist nicht immer eindeutig, welche Parameter auf eine Beschädigung hinweisen“, sagt Kyle Weise. „Faktoren wie Farbe, Form und Größe können variabel sein und nicht als Indikator für bestandene/nicht bestandene Inspektionen in Frage kommen.
Für diese Problemlösung haben wir maschinelles Lernen eingesetzt. Unser Team für die optische Prüfung trainierte ein neuronales Netzwerk mit den Parametern des Saatguts und kam so zu überzeugenden Ergebnissen.“
Nach der Inspektion werden die Wannen an eine robotergestützte Stampfstation geschickt, an der das Saatgut in die Wannen gestampft wird. Die Wannen werden danach an eine robotergestützte Wagenstation transportiert, an der sie auf Wagen geladen und indexiert werden. Sind die Wagen befüllt, werden sie in Prüfräume gebracht, in denen das Saatgut keimen kann.
Nach Abschluss des Prüfverfahrens werden die leeren Wannen aus dem Prüfraum herausgefahren und robotergestützt aus den Wagen entnommen, bildlich erfasst, gereinigt und wieder in die Wagen umgeladen, auf denen sie zurück an den Anfang der Prüflinie gebracht werden.
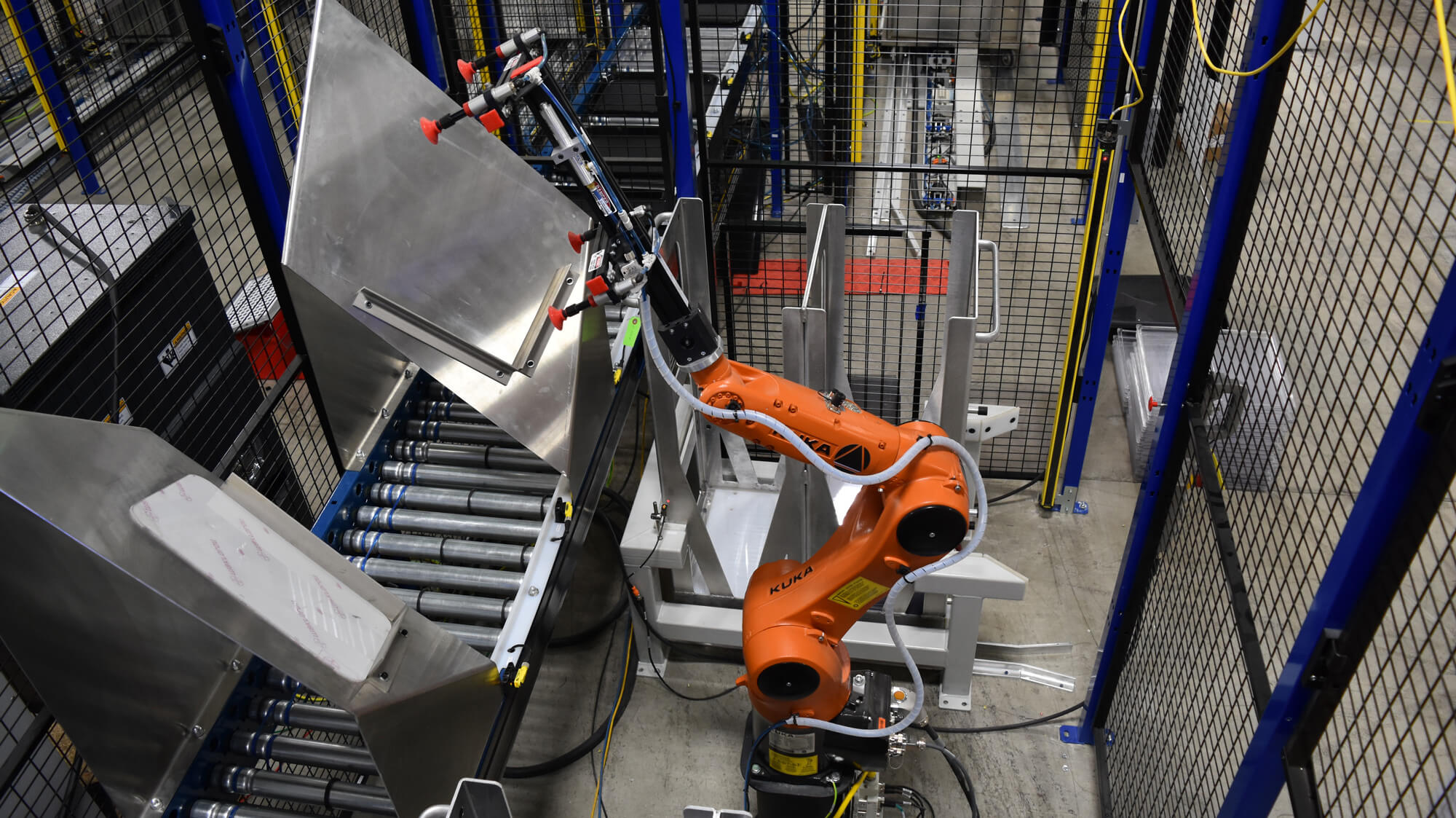
Der Prozess wird von Montag bis Freitag in zwei Schichten durchgeführt.
Für diese Problemlösung haben wir maschinelles Lernen eingesetzt. Unser Team für die optische Prüfung trainierte ein neuronales Netzwerk mit den Parametern des Saatguts und kam so zu überzeugenden Ergebnissen.
Kyle Weise, Marketing Director bei IAS
Das Ergebnis
Die fertige Linie besteht aus 12 Robotern, 13 Kameras und verschiedenen RFID-Lese-/Schreibbereichen. Weitere 15 integrierte Kameras werden eingesetzt, um die Wagenbewegungen an den Eingängen der Prüfräume zu überwachen. IAS entwickelte eine maßgeschneiderte Automatisierungslösung für den Saatgut-Prüfprozess dieses Kunden.
„IAS konnte uns eine einsatzbereite Komplettlösung liefern“, sagt Kyle Weise. „Dazu gehörten das elektrische und mechanische Systemdesign, die Programmierung, das Testen, die Konstruktion und die Installation.“
Das Ergebnis des Projekts ist eine Steigerung des Durchsatzes und eine Senkung der Arbeitskosten. Darüber hinaus hat der Kunde dank IAS wieder Vertrauen in seine Daten.
„Der Kunde kann den gesamten Prozess nun nachverfolgen“, sagt Kyle Weise. „Bei der Datenanalyse profitiert er von einer höheren Datensicherheit und -rückverfolgbarkeit.“
IAS konnte uns eine einsatzbereite Komplettlösung liefern. Dazu gehörten das elektrische und mechanische Systemdesign, die Programmierung, das Testen, die Konstruktion und die Installation.
Kyle Weise, Marketing Director bei IAS
Zum Weiterlesen
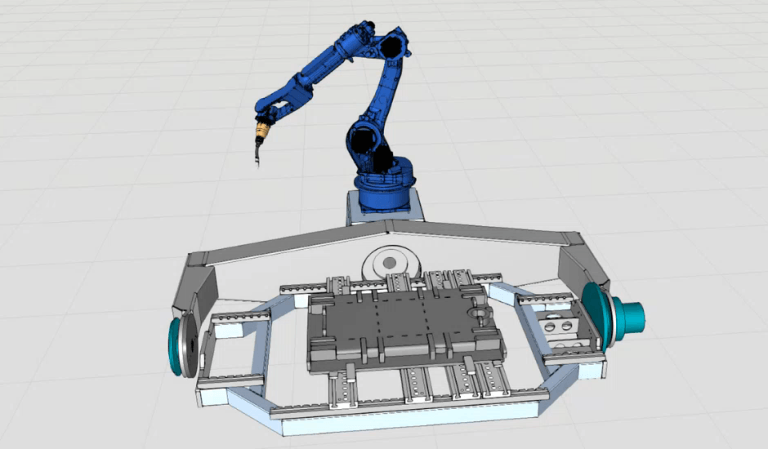
Komplexe Schweißarbeiten in ihrer gesamten Bandbreite und Detailtiefe meistern: Wie Bunorm Maschinenbau die Qualität und Effizienz mit Visual Components OLP gesteigert hat
Bunorm Maschinenbau, ein Spezialanbieter in der Maschinenindustrie, ist bestrebt, seine Infrastruktur auf einem hohen Niveau zu modernisieren und flexibel zu gestalten. Mit ihren weitreichenden Möglichkeiten steht die Steigerung der Produktionseffizienz...
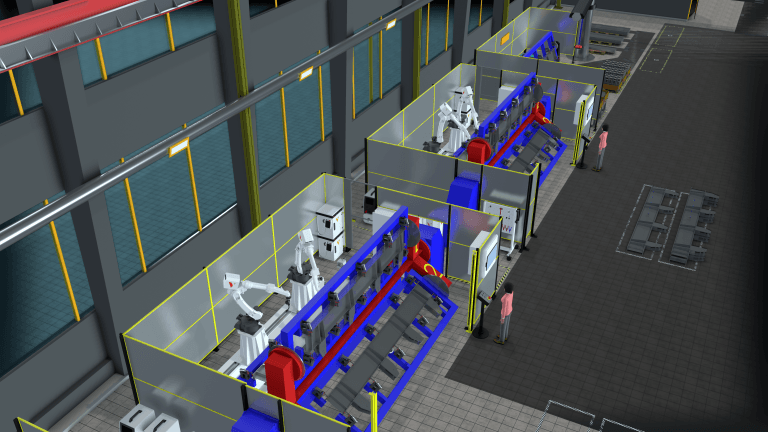
BENTELER Anwenderbericht: Die Entwicklung der Fertigungstechnik von morgen
Gemeinsam mit BENTELER Automobiltechnik setzt das Karlsruher Institut für Technologie moderne Fabrikplanungssoftware von Visual Components ein, um innovative Produktionstechnologien zu entwickeln.
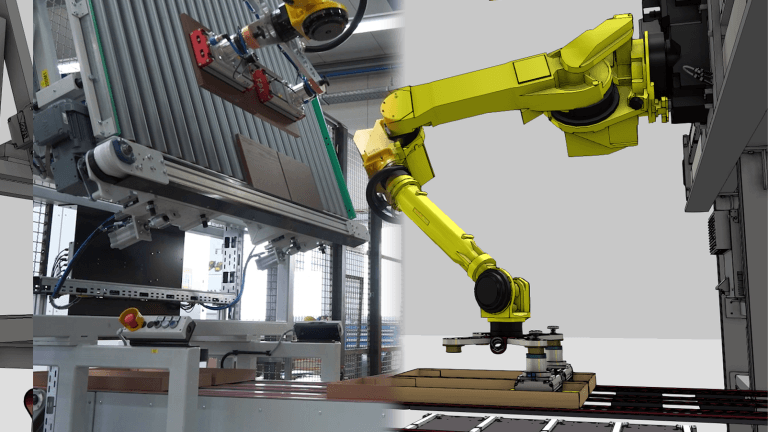
Verpackung in Perfektion: Wie Wächter Packautomatik mit Visual Components die Variationen bei Möbelverpackungen bewältigt
Möbel waren früher überwiegend teure, handwerklich hergestellte Einzelstücke, die teilweise über Generationen genutzt wurden. Heute werden die meisten Möbel in Massen- und Serienproduktion aus MDF- oder Spanplatten hergestellt, oft auch...