Anwenderbericht MAG
MAG bietet Komplettlösungen bis hin zu schlüsselfertigen Anlagen und flexiblen Fertigungssystemen, die mit den Lösungen von Visual Components geplant, simuliert und optimiert werden.
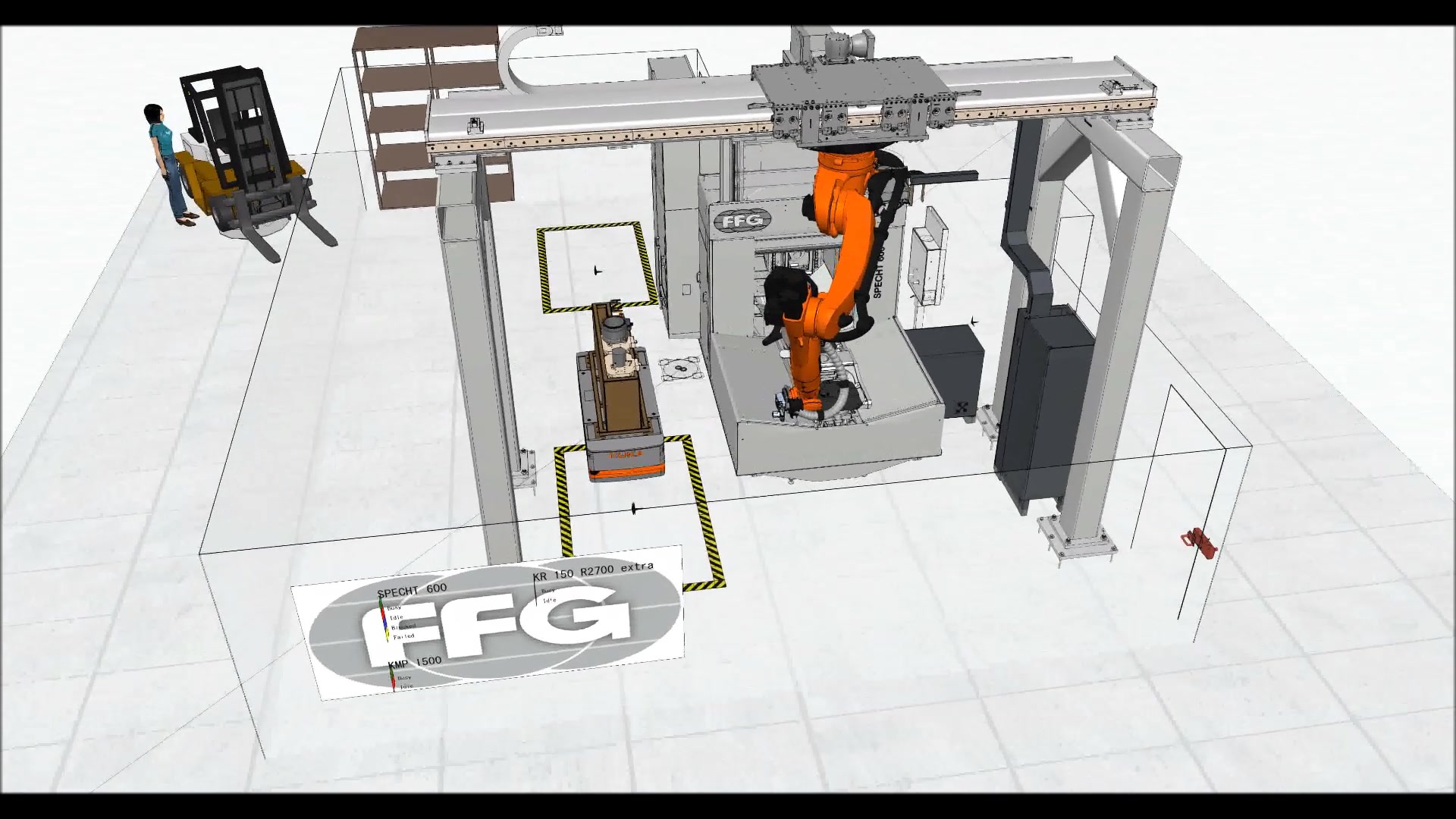
Wie MAG mit Simulation flexible Fertigungssysteme optimiert
Die Automobilhersteller lagern immer größere Teile ihrer Fertigung an Zulieferbetriebe aus. Wegen der zunehmenden Modellvielfalt stehen die Zulieferer vor der Herausforderung, auch kleinere Losgrößen effizient und ökonomisch zu bearbeiten. Die Lösung sind flexible Fertigungszellen, die rasch wechselnde Aufträge autonom bearbeiten und Teile wie Getriebegehäuse, Achsschenkel usw. weitgehend ohne Personal rund um die Uhr fertigen. Ergänzt werden sie durch Mess-, Montage- oder Reinigungsapplikationen, welche die mechanische Zerspanung komplettieren. Planung und Optimierung solcher Fertigungszellen werden entscheidend erleichtert durch Software für die 3D-Fabriksimulation des finnischen Lösungsanbieters Visual Components.
FFG Europe & Americas vereint große Traditionen der deutschen, italienischen, schweizerischen und amerikanischen Werkzeugmaschinenindustrie in einer Gruppe und bietet ein herausragendes Portfolio an Dreh-, Fräs-, Schleif- und Verzahnmaschinen und eine einzigartige Know-how-Basis. Mit den Simulationslösungen von Visual Components können die vielen Parameter eines flexiblen Fertigungssystems zu einer hohen Gesamtproduktivität abgestimmt werden, denn Visual Components optimiert entscheidende Faktoren wie Nebenzeiten, Taktzeiten, Layout-Topologie, Automationstypen, Verfügbarkeiten usw.
AGVs und Roboter be- und entladen die Maschine
Im Rahmen eines Projekts hat die Abteilung Factory Automation von MAG ein flexibles Fertigungssystem zur mannlosen bzw. mannreduzierten Fertigung konzipiert. Die Zufuhr der Werkstücke erfolgt zunächst mit intelligenten, autonomen Fahrzeugen (KUKA KMP 1500), welche das Fertigungssystem leitwerkgesteuert in perfektem Timing mit den auf Paletten fixierten Werkstücken versorgen. Diese über WLAN angesteuerten AGVs (Autonomous Guided Vehicles) können sich frei und ohne klassische Spurführungs- oder Navigationselemente bewegen; sie weichen Hindernissen dank ihrer Laser-Scanner aus und erreichen eine Positionierungsgenauigkeit von wenigen Millimetern.
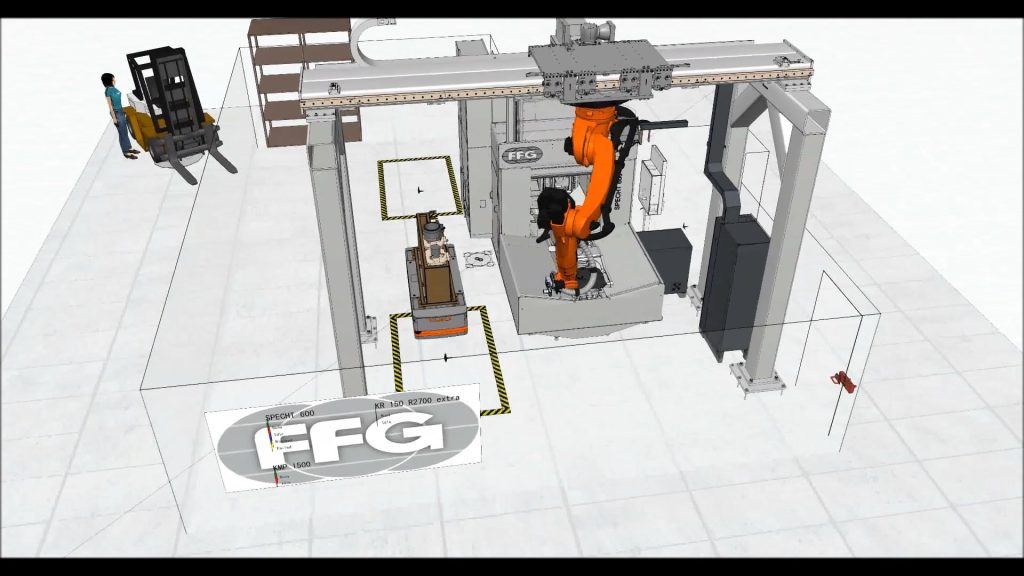
An einem Portal vor dem SPECHT® 600 Bearbeitungszentrum hängt über Kopf ein KUKA Quantec Roboter mit 6 Achsen; eine 7. Achse, die Linearachse längs des Portals, wird ebenfalls von der KR C4 Steuerung mitverwaltet. Der Roboter ist zusätzlich mit einer Kamera SIEMENS Vision MV 400 ausgestattet; damit kann der Greifer des Roboters exakt zur Palette mit dem Werkstück positioniert werden. So kann der Roboter die Werkstückpaletten greifen und dem Bearbeitungszentrum mit seinem Palettenwechsler zuführen. Anschließend schwenkt der Palettenwechsler zur Beladung der Werkzeugmaschine um 180° in den Arbeitsraum.
Neben dem Be- und Entladen der Werkzeugmaschine kann der KUKA Quantec Roboter weitere Zusatzaufgaben übernehmen, z. B. die Spankontrolle, die Beseitigung von Spänenestern und allgemeine Reinigungsaufgaben am bearbeiteten Werkstück. Aber auch Tätigkeiten wie Anfasen und Entgraten können vom Roboter durchgeführt werden, während die Werkzeugmaschine bereits das nächste Werkstück bearbeitet. Und mit der am Roboterarm angebrachten Kamera ist auch eine permanente Qualitätskontrolle realisierbar, z. B. hinsichtlich der Vollständigkeit der am Werkstück durchgeführten Bohrungen.
Simulation ermöglicht die Optimierung des Fertigungssystems
Wie hat MAG dieses komplexe Fertigungssystem konzipiert und optimiert? Es kam ja entscheidend darauf an, dass alle Systeme nahtlos ineinandergreifen und dass der gesamte Materialfluss, von der Anlieferung der Paletten bis zu deren Weitertransport zur nächsten Fertigungsstation ohne jede Verzögerung abläuft, und das bei verschiedenen Werkstücken mit unterschiedlicher Bearbeitungsdauer. Die Lösung bestand darin, das gesamte Fertigungssystem zu simulieren, und zwar mit der Software zur 3D-Fabriksimulation von Visual Components.
Mit Visual Components hat MAG sowohl Anordnung und Abmessungen des Fertigungssystems konzipiert und optimiert, als auch die Offline-Programmierung des Roboters vorgenommen. MAG hat mit der Software den gesamten Fertigungsablauf und die reibungslose Zusammenarbeit von AGV, Roboter und Werkzeugmaschine simuliert. Dank der Simulation wurden die Nebenzeiten minimiert, und es konnten Fragestellungen wie die Erreichbarkeit durch den Roboter und die Vermeidung von Kollisionen geklärt werden.
Roboterdaten aus Komponentenbibliothek von Visual Components übernommen
Dabei musste MAG für die Simulation nur relativ wenig Aufwand betreiben, denn dank der zahlreichen CAD-Schnittstellen konnten die geometrischen und kinematischen Eigenschaften der Werkzeugmaschine leicht aus vorhandenen CAD-Daten übernommen werden. Noch dazu sind in der Bibliothek von Visual Components zahlreiche Roboter samt Kinematik, Achsbegrenzungen, Beschleunigungen und Positionsgenauigkeit enthalten. Auch andere gängige Standard-Industriekomponenten wie Förderbänder, Absperrgitter usw. konnten einfach durch Drag-and-Drop aus der Komponentenbibliothek von Visual Components übernommen werden.
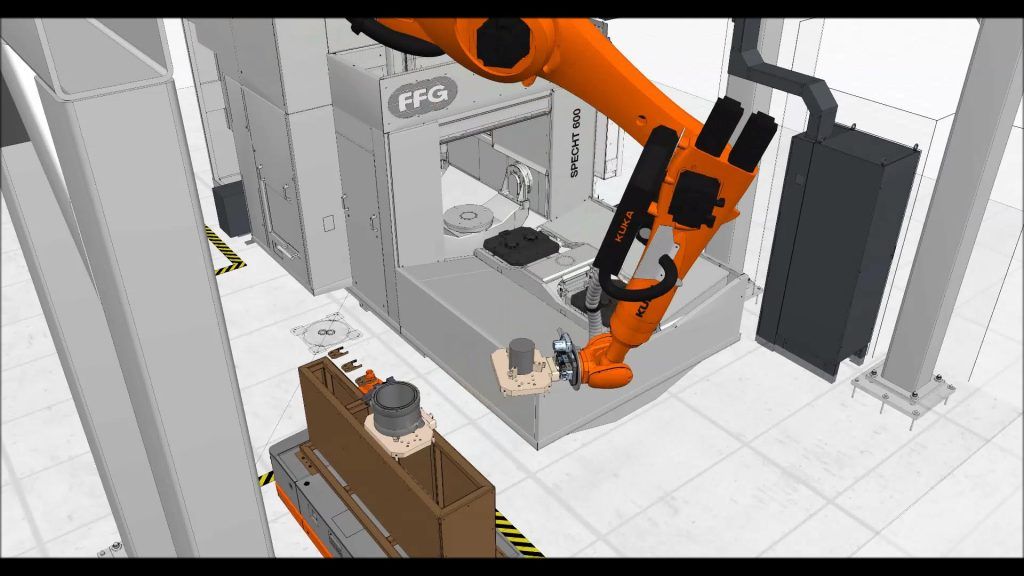
Marcel Deeß, Projektleiter Digitale Fabrik / Automation bei MAG, der für das Projekt verantwortlich war, berichtet: „Die CAD-Modelle der Werkstücke kommen in fast allen Fällen als 3D-Modelle, im STEP- oder IGES-Format oder als native Daten. Mit Visual Components gibt es keine Probleme mit dem Einlesen der CAD-Modelle. Wir haben auch Erfahrungen mit anderen Simulationstools, aber diese scheinen uns viel komplizierter; man meint oft, das kommt aus den 80er Jahren. Die Software von Visual Components dagegen ist sehr logisch aufgebaut.“
Die Einarbeitung in das System wurde dadurch erleichtert, dass sich die Bedienungsoberfläche an AutoCAD orientiert, das den Ingenieuren von MAG vertraut ist. Falls sie mal nicht weiterwussten, half ein Anruf beim Support von Visual Components weiter.
Die CAD-Modelle der Werkstücke kommen in fast allen Fällen als 3D-Modelle, im STEP- oder IGES-Format oder als native Daten. Mit Visual Components gibt es keine Probleme mit dem Einlesen der CAD-Modelle.
Marcel Deeß, Projektleiter Digitale Fabrik / Automation bei MAG
Simulation deckt frühzeitig Schwachstellen im System auf
Dank der Simulation mit Visual Components konnte MAG die Länge, Höhe und Position des Portals, das den Roboter trägt, exakt so dimensionieren, dass der Roboter alle gewünschten Positionen unter Berücksichtigung seiner Achsenbegrenzungen in kurzer Zeit anfahren konnte, ohne dass es zwischen Roboter, Palette und Maschine zu Kollisionen kam. Ausschlaggebend für die Vermeidung von Schwachstellen im System war die Simulation mit ihrer realistischen Modellierung dynamischer Wechselbeziehungen.
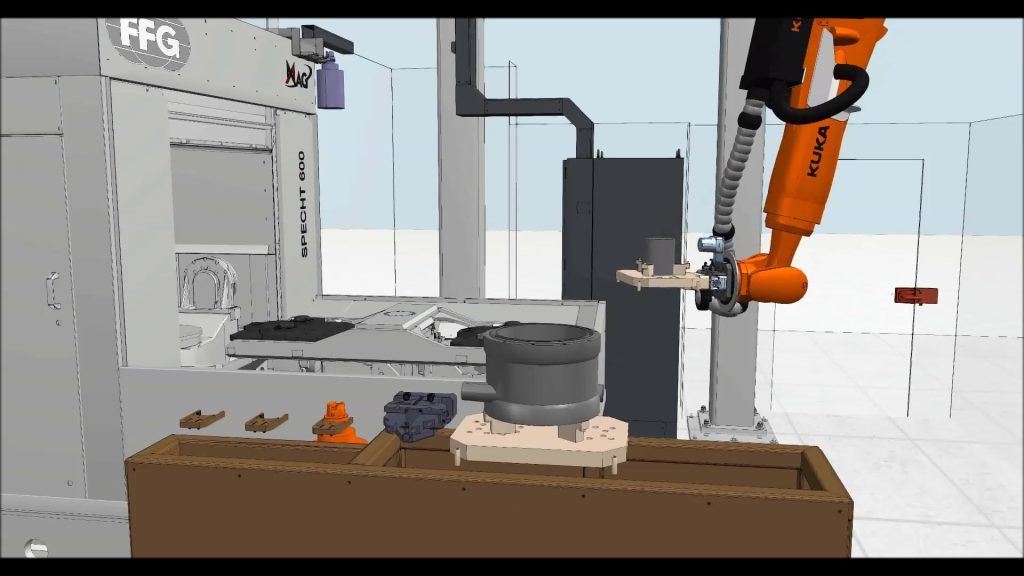
Als Ergebnis der Simulation wurden Virtual-Reality-Daten generiert, ferner 3D-PDFs und Videos, die den simulierten Ablauf der Fertigung aus allen möglichen Perspektiven zeigten. Außerdem hat Visual Components Statistiken und Tabellen generiert, ferner Zeichnungen im DWG-Format, welche die Anordnung von Maschine, Roboter und Portal dokumentierten. Auch Daten zur Ansteuerung des Roboters konnten direkt aus Visual Components übernommen werden.
Simulation mit Visual Components hat MAG viel Zeit und Geld gespart
Hat sich die Simulation mit Visual Components gelohnt? Die Antwort von Marcel Deeß von MAG fällt eindeutig aus: „Auf jeden Fall, denn die Simulation hat uns viel Zeit und Geld gespart! Und die Simulation wurde nicht nur intern sehr gut aufgenommen, z. B. von unserem Vertrieb, sondern auch die Kunden sind begeistert, wenn sie „ihre“ Anlage bereits in einem frühen Planungsstadium sehen können. Mit Visual Components können sie zum Beispiel Position und Parameter eines Roboters ändern, um das System exakt nach ihren Bedürfnissen zu optimieren. Das vermeidet nicht nur kostspielige Fehler in der Planung, sondern es unterstützt uns auch in der Angebotsphase und hilft uns, erfolgreicher zu verkaufen.“
Weil das Projekt so erfolgreich verlaufen war, wurde es auch auf der Messe AMB 2018 ausgestellt. Neben der realen Fertigungszelle wurden der mit Visual Components modellierte „digitale Zwilling“, die Simulation und ihre Ergebnisse auf Bildschirmen präsentiert. Bei Kunden und Interessenten kam sehr gut an, dass Prozess- und Anlagensimulation schon in der Planungsphase für höchste Transparenz sorgen.
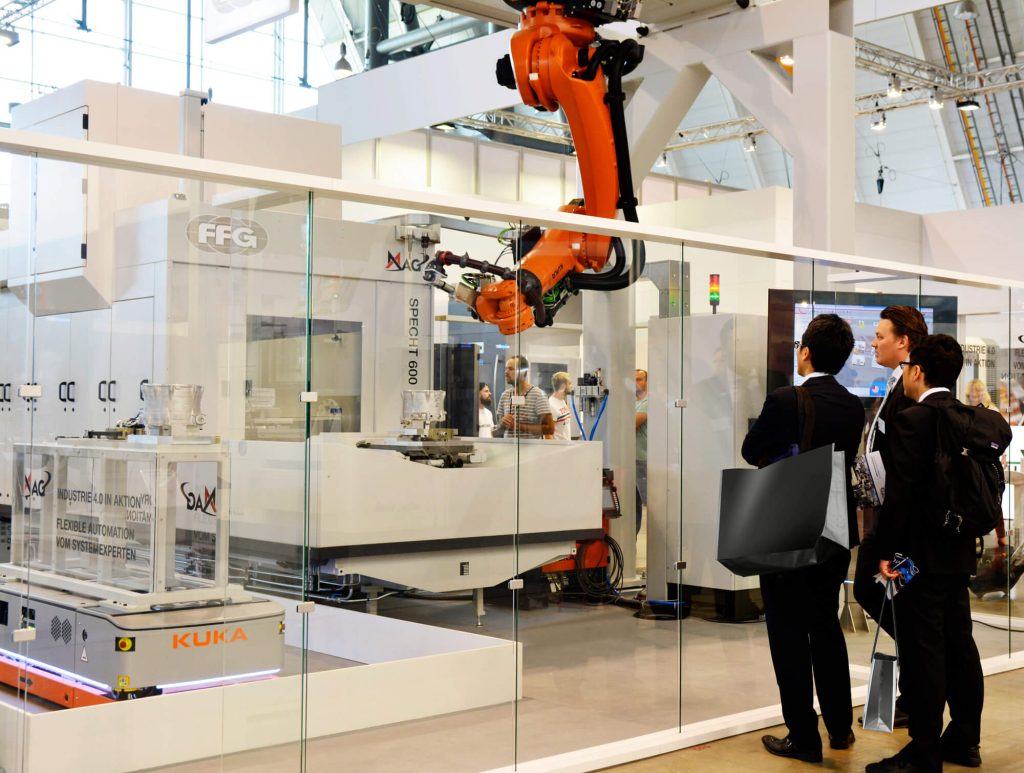
Mit Visual Components können sie zum Beispiel Position und Parameter eines Roboters ändern, um das System exakt nach ihren Bedürfnissen zu optimieren. Das vermeidet nicht nur kostspielige Fehler in der Planung, sondern es unterstützt uns auch in der Angebotsphase und hilft uns, erfolgreicher zu verkaufen.
Marcel Deeß, Projektleiter Digitale Fabrik / Automation bei MAG
Flexible und intelligente Fertigung – dank Simulation
MAG und Visual Components zeigen, wie die Fertigung der Zukunft näher am Kunden, flexibler und intelligenter sein kann. Dank Robotik und Automatisierung in der Produktion können die Stückkosten so weit gesenkt werden, dass es wieder attraktiv wird, auch in Hochlohnländern zu fertigen. Digitalisierung, Automatisierung und Simulation helfen dabei, dass Unternehmen bei der Standortwahl nicht mehr nur auf die Arbeitskosten achten.
Über MAG
Das Unternehmen MAG IAS GmbH (MAG) mit Sitz in Eislingen/Fils gehört zu FFG Europe & Americas. FFG vereint große Namen der Werkzeugmaschinenindustrie und bietet mit Marken wie VDF Boehringer, Hessapp, MAG, Witzig & Frank und anderen ein herausragendes Portfolio an Dreh-, Fräs-, Schleif- und Verzahnmaschinen. MAG bietet Komplettlösungen bis hin zu schlüsselfertigen Anlagen und flexiblen Fertigungssystemen, die mit den Lösungen von Visual Components geplant, simuliert und optimiert werden. Das Herzstück solcher flexiblen Fertigungssysteme sind kundenspezifisch konfigurierbare Bearbeitungszentren wie z. B. die SPECHT®-Baureihe von MAG.
Bei FFG werden die Aktivitäten von DIGITAL FACTORY und INDUSTRY 4.0 in der neuen Marke DIGITAL FRIENDS zusammengefasst.
Schauen Sie sich den Originalartikel hier an: Mit Simulations-Know-how zielsicher zur optimalen Fertigungszelle.
Zum Weiterlesen
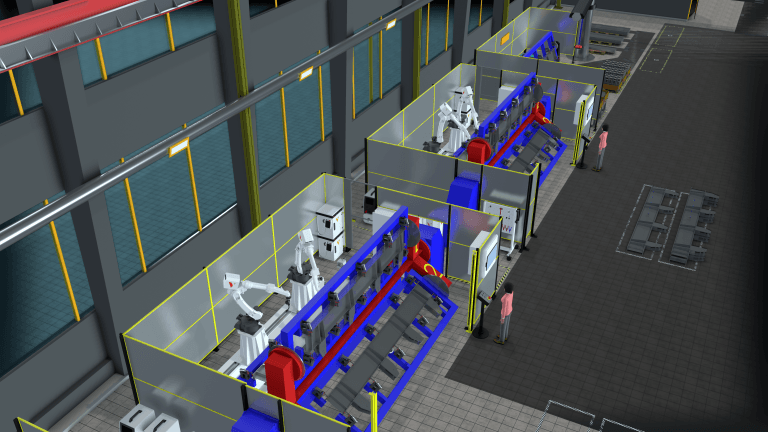
BENTELER Anwenderbericht: Die Entwicklung der Fertigungstechnik von morgen
Gemeinsam mit BENTELER Automobiltechnik setzt das Karlsruher Institut für Technologie moderne Fabrikplanungssoftware von Visual Components ein, um innovative Produktionstechnologien zu entwickeln.
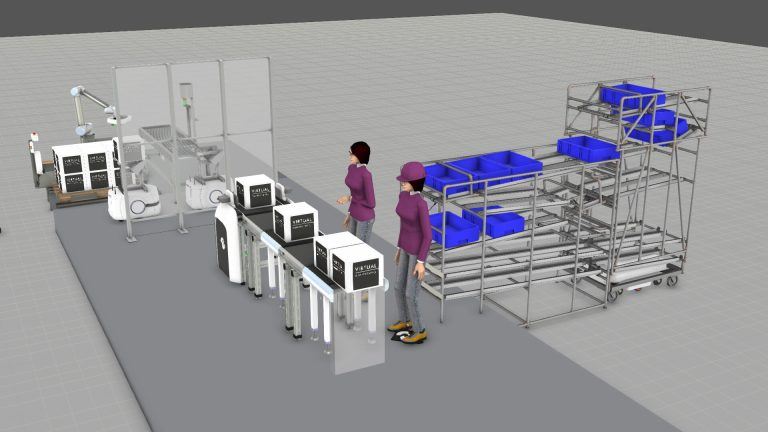
Fallstudie eines Virtual Manufacturing-Projekts: Umsatzsteigerung mit 3D-Simulation
Virtual Manufacturing, Entwickler von schlanken Produktionsprozessen und Value-Added-Reseller von Visual Components-Lösungen, kennt die Stärken der Simulation in der Produktion. In dieser Fallstudie befassen wir uns mit einem kürzlich abgeschlossenen Projekt...