製造業におけるデジタルツインとは
デジタルツインは、単なる静的なモデルやシミュレーションではありません。仮想と現実をつなぐ橋渡しとして機能し、リアルタイムのデータを活用して、現場の状況を把握しながら設備やプロセスを柔軟に制御・最適化することができます。しかし、「デジタルツイン」という言葉には多様な定義があり、誤解されがちです。この記事では、デジタルツインの本質を整理するとともに、製造業における具体的な活用例や今後の展望についてわかりやすくご紹介します。
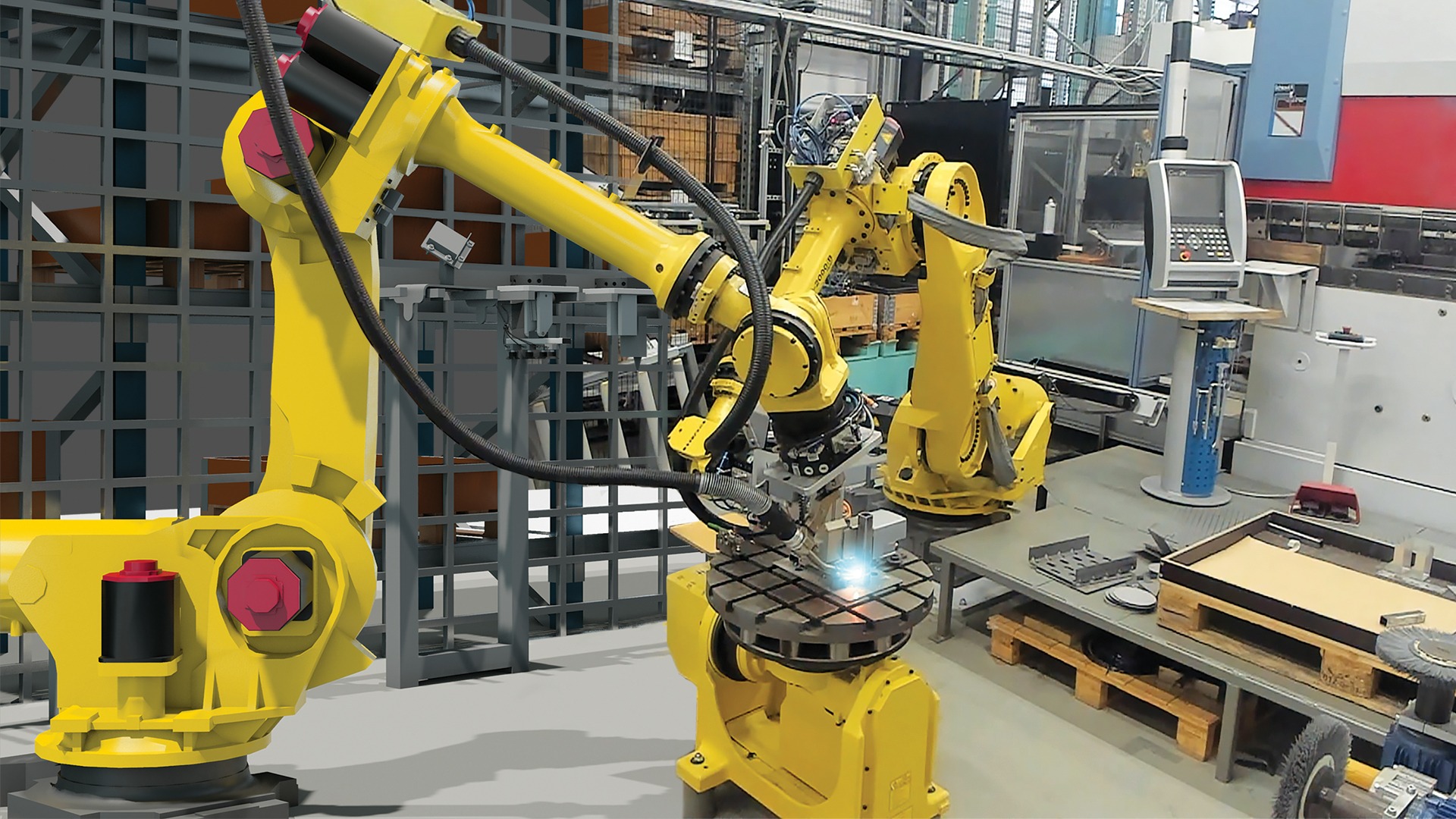
製造業におけるデジタルツインとは
デジタルツインとは何か
製造業で注目されている技術トレンドの1つがデジタルツインです。では、それはどんなもので、何ができるのでしょうか?単なる高度な3Dモデルなのでしょうか?それとも、製造のあり方を根本から変える可能性を持つ技術なのでしょうか?
Visual Componentsは、製造シミュレーション、ロボットオフラインティーチング(OLP)、そしてデジタルツインの実装に強みを持つプラットフォームです。私たちは、こうした技術の活用を提案するなかで、「シミュレーションから始めること」の重要性を一貫して発信しています。
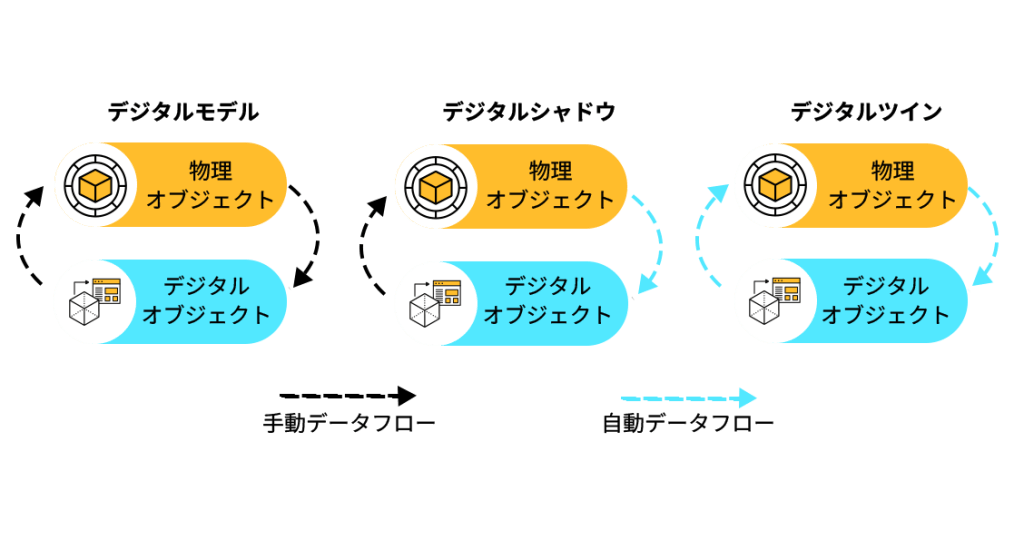
「デジタルツイン」という言葉を語るうえで、まずよくある誤解を解かなければなりません。「高度なデジタルモデル」や「デジタルシャドウ」と同義に扱われることもありますが、これらは本質的に異なる概念であり、明確な違いがあります。
デジタルモデルは、製品や設備、工場レイアウトなどを3Dで表現したものです。静的なモデルやシミュレーションの形を取ることがありますが、現実のデータと連携して動くわけではありません。
デジタルシャドウは、物理システムからリアルタイムでデータを受け取る仮想モデルです。データは一方向に流れるため、状況の把握や分析には使えますが、物理システムへの制御や介入は行えません。
デジタルツインは、物理システムとリアルタイムで双方向にデータをやりとりします。これにより、現場の状態を常に把握し、異常の兆候を早期に検知し、実際のデータをもとにプロセスの最適化ができるようになります。
これまでの内容では、デジタルツインの基本と、誤解されがちなポイントを整理してきました。では次に、製造業の現場でこの技術が実際にどのように使われているかを見ていきましょう。
製造現場の進化を支えるデジタルツインの活用領域
Visual Componentsでは、「工場」や「プロセス」に特化したデジタルツインを提供しています。これらは単なる可視化ツールにとどまらず、シミュレーションと実際の運用データを結びつけ、工場やその工程の効率化を支援します。
では、こうしたデジタルツインは、製造現場のどんな場面で最も効果を発揮するのでしょうか?
バーチャルコミッショニング
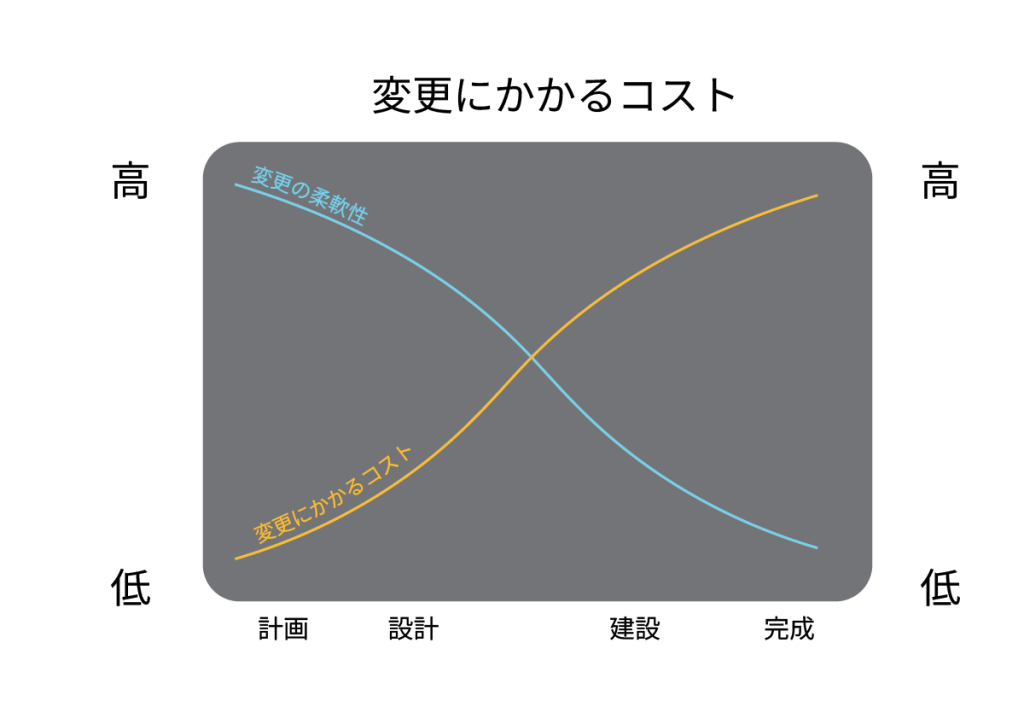
バーチャルコミッショニングは、問題の早期発見に役立つ手法ですが、デジタルツインを活用すれば、その効果をさらに高めることができます。従来のバーチャルコミッショニングでは、仮想環境で自動化を事前にシミュレーションできますが、このプロセスはあくまで一方向的なもので、システム稼働後に発生する現実の変化をシミュレーション側に反映させることはできません。
デジタルツインを導入すれば、システム稼働後も継続的に運用できる仕組みに変わります。例えば、自動車の診断システムのように、常に状態を監視し、問題の兆候を検知し、最適な対応を提案できるようになります。これにより、導入前の検証だけでなく、稼働中のモニタリングや予知保全、性能改善まで一貫して対応可能になります。
こうした双方向のデータ連携は、コンプライアンスや安全基準への適合を継続的に確認するうえでも有効です。リアルタイムの稼働データを活用することで、導入時だけでなく、日々の運用でも基準を満たしているかどうかを常に把握できます。
変化に強いプロセス設計を支える仕組み
製造プロセスは日々変化します。
突発的なボトルネック、需要の変動、機械の摩耗、製品構成の変更など、計画通りにいかない要素は数多く存在します。デジタルツインがあれば、あらかじめ定義したシナリオに依存せず、現場の状況に合わせてプロセスを柔軟に調整しながら、運用を最適化できます。
例えば、ある包装工場では、生産量の変動や供給の遅れによって特定エリアでコンベヤーが混雑することがあります。こうした場合でも、デジタルツインによって流れの乱れをリアルタイムで把握し、コンベヤー速度の調整や搬送ルートの変更、バッチサイズの見直しなど、迅速かつ的確に対応できます。
人材育成と技術継承を支えるデジタルツイン
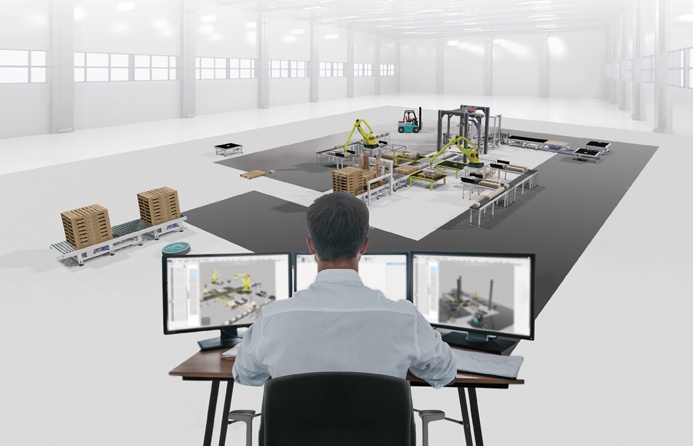
製造現場で新たな人材を育てるのは簡単ではありません。複雑な機器、安全リスク、稼働中の生産ライン、厳しい生産スケジュールが重なり、実践的な学習機会が制限されがちです。デジタルツインを活用すれば、現場さながらの状況を仮想空間で再現し、安全な環境でトレーニングできます。
従来の教育手法では、紙のマニュアルや座学、限られた実地訓練を通じて学ぶのが一般的でした。デジタルツインを活用すれば、リアルタイムかつインタラクティブな環境で学習できます。従業員は、機械の操作を確認したり、生産シナリオを試したり、トラブル対応をシミュレーションで体験したりと、実際の生産を止めることなく実践的に学べます。こうした仕組みにより、実務に入るまでの準備が効率化され、必要なスキルも短期間で習得できます。
教育は本配属後も続くものです。新たな自動化システムやフローの導入に合わせて、現場でのスキルも進化させる必要があります。デジタルツインがあれば、業務の変化に応じてトレーニングプログラムを柔軟に更新でき、実務と教育の両立が図れます。
デジタルツインを活用し、人材育成を継続的かつ柔軟なプロセスにすることで、企業は製造業における慢性的な人手不足に対し、さまざまな対策を講じることができます。
シミュレーションから始めるべき理由
工場全体をリアルタイムかつ双方向に連携する完全なデジタルツインという考えは、理想的に聞こえます。しかし、ほとんどの企業では、すべての機器やシステム、データを完全に連携させる準備ができていません。コストや複雑さの面でハードルが高いと感じているからです。
そこで現実的かつ効果的な選択肢となるのが、シミュレーションです。Visual Componentsのようなプラットフォームを使えば、リアルタイム接続や複雑な統合なしで、制御された安全な環境でシステムの検証・改善・最適化を行えます。レイアウト設計やプロセスの流れ、自動化の構想などを自由に試せるため、導入初期のリスクを大幅に低減できます。
Visual Componentsのeカタログには、3Dで高精度に作成された各種設備コンポーネントが多数収録されており、ゼロからのモデリングは不要です。すぐにシミュレーションを開始でき、実運用に向けた準備を着実に進めることができます。
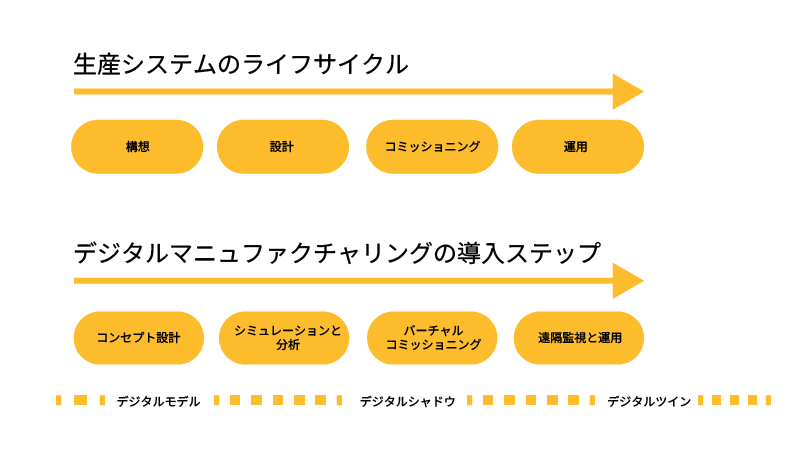
工場全体を一度に刷新するのではなく、まずは1つの工程から着手し、構想の具体化、改善の検証、そして段階的な拡張へとつなげていく――これが現実的かつ着実なアプローチです。デジタルトランスフォーメーションは、一夜にして完結するものではありません。シミュレーションはその第一歩として、リスクを抑えながら、デジタルツインを現場に無理なく取り入れる手段となります。
AI×デジタルツインが切り拓く、製造業の新たな可能性
デジタルツインの進化は、製造業にこれまでにない価値をもたらしつつあります。今後はAIとの統合により、予測精度や自己最適化の能力が一層高まり、故障の兆候を検知するだけでなく、最適な対応策の提示まで自動で行えるようになります。AIによる予測分析は、在庫管理の最適化や廃棄物の削減、需要変動に応じた柔軟な生産体制の構築などにおいて、欠かせない役割を担うようになるでしょう。AIとデジタルツインを組み合わせることで、メーカーは本当の意味で「データに基づく意思決定」ができるようになります。
さらに技術が浸透すれば、工場全体をカバーするデジタルツインの活用も標準化されていく見込みです。稼働状況をリアルタイムで把握・最適化することで、サステナブルなものづくりへの転換も加速します。廃棄物の削減、エネルギー使用の最適化、環境負荷の低減といった面でも、大きな効果が期待されます。
いますぐに行動すべき理由
いまこのタイミングでデジタルツインの導入に踏み出した企業は、将来的に大きな競争優位性を獲得できます。
Visual Componentsは、シミュレーションやプロセス検証の初期段階から、ロボットティーチング、そしてフルスケールのデジタルツイン構築まで、あらゆる段階を支援する包括的なプラットフォームと製品を提供しています。
シミュレーションやバーチャルコミッショニングを活用し、製造オペレーションの次なるステージを目指す企業の皆さま。ぜひお気軽にお問い合わせください。製造業の未来はすでにデジタルへと進化しています。Visual Componentsが、その第一歩をご支援します。
Further reading
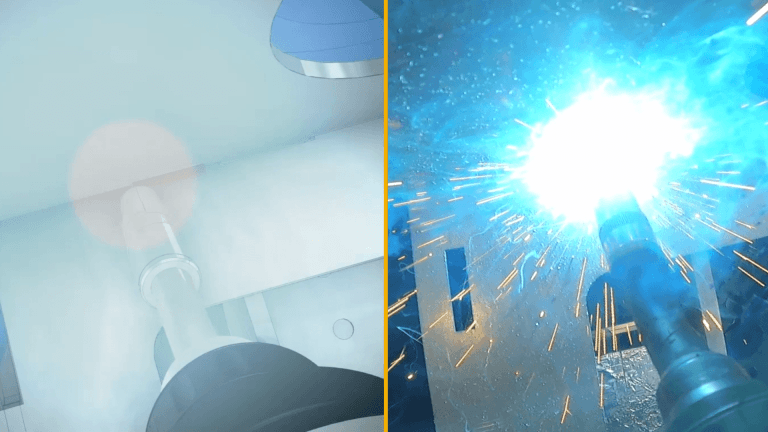
ロボットオフラインティーチング(OLP):完全ガイド(事例付き)
ロボットオフラインティーチング(OLP)を基礎から応用まで幅広く解説したガイドです。本ガイドでは、トピックの紹介に続いて、よくある誤解やOLPが解決する課題、その利点、そして実際の成功事例について詳しく説明します。