シミュレーションから始める、よりスマートな倉庫計画
人件費やその他のコストを抑えつつ、初日から効率よく稼働する倉庫を設計するにはどうすればよいでしょうか?鍵になるのは、Visual Componentsのようなシミュレーションツールを使った、事前の十分な検討と検証です。
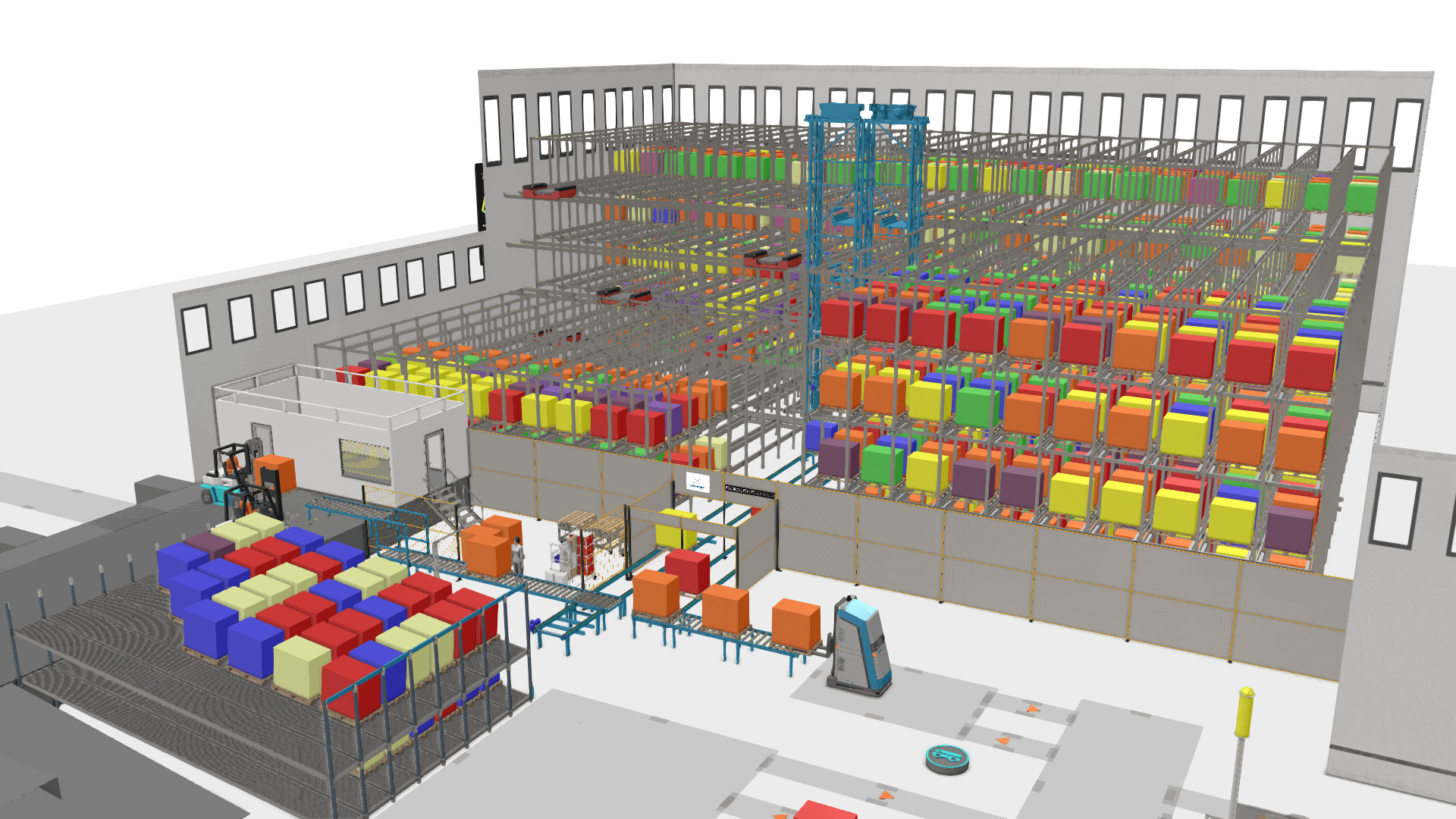
適切に設計されていなければ、当然倉庫は適切に機能しません。
当たり前のように聞こえるかもしれませんが、事前計画が不十分な倉庫では、生産性が最大で20%も低下する可能性があります。例えば、動線が長すぎたり、棚とピッキングステーションの距離が離れていたりすると、移動に時間がかかって作業効率が落ちます。回転率の高い商品が取りにくい場所にある場合も、余計に時間がかかってしまいます。また、適切に設計されていない倉庫は、新たなボトルネックや非効率を招く要因にもなりかねません。
計画的な倉庫づくりの土台
構造や機能はさまざまですが、効率性と柔軟性を両立することは、どの倉庫にも共通の課題です。大量保管を優先する場合も、迅速な出荷や流通拠点としての役割を重視する場合も、スムーズな運用と変化への対応力が求められます。
レイアウトや作業効率を改善するには、まず現場に潜む課題を特定することが重要です。無駄なスペースや時間のかかるピッキング、作業エリアの混雑などは、いずれもコスト増加や生産性低下の原因となります。特に繁忙期には、こうした問題が顕在化しやすく、継続的な改善の必要性が高まります。
倉庫管理システム(WMS)や動線分析ツールを活用すれば、混雑が起きやすい場所や無駄な移動が発生しているルートなど、具体的な課題を可視化できます。ただし、課題を把握するだけでは不十分です。レイアウトの見直し、自動化機器の配置、ワークフローの整理といった要素を相互に関連づけながら、全体として無理のない流れを構築することが重要です。
倉庫設計の初期段階
優れた倉庫設計には、論理的な思考と柔軟な発想の両方が求められます。スペースを最大限に活用し、業務をスムーズに流しながら、将来的な変化にも柔軟に対応できなければいけません。そのためには、保管効率と作業のしやすさを両立させ、無駄のない動線を確保する必要があります。また、自動化の導入にあたっては、工程がかえって煩雑にならないよう注意が必要です。例えば、ロボットピッキングシステムを導入すれば、注文処理の精度を最大99.9%まで高めることができますが、ピッキングゾーンと梱包エリアの距離が離れていたり、混雑の発生を考慮していなかったりすると、その効果を十分に引き出せません。
とはいえ、いかに計画が綿密であっても、現場での実際の動きや制約をすべて予測することはできません。机上では完璧に見えるレイアウトも、現場で期待通りに機能しないことは少なくありません。だからこそ、設計を実行に移す前に、シミュレーションによる検証と改善を重ねておくことが、これまで以上に重要になっています。
倉庫設計にシミュレーションを活用すべき理由
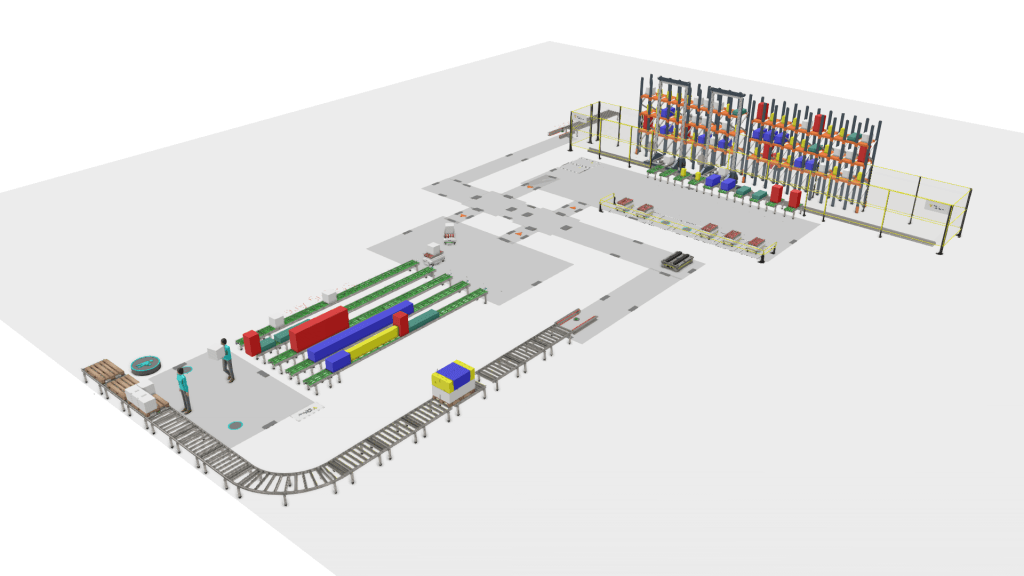
設計段階でシミュレーションを活用することで、現場での失敗から学ぶよりもリスクを大幅に抑えることができます。
シミュレーションを活用することで、企業は以下のような検証や分析を行えます。
- 保管レイアウトの違いがピッキング時間に与える影響の比較
- 人・機械・フォークリフト・製品の動きをシミュレーションし、混雑の発生前にリスクを検知
- AGVやコンベヤー、ロボットの性能評価と自動化の効果測定
- 需要変動をモデル化し、ピーク時の対応力を事前に確認
- 積み下ろしやトラック動線、在庫の流れを見える化し、入出荷の効率を改善
事前にこうした検証を行うことで、試行錯誤にかかるコストを抑えつつ、より納得感をもって判断が下せます。事前に成果を確認できるため、安心して導入に踏み切れるのです。特に、自動倉庫システム(AS/RS)やロボットを導入する場合、高さや構造の強度を考慮した設計が求められるため、レイアウトやスペースの最適化は早い段階から進めておくことが重要です。
Visual Componentsが支える、戦略的な倉庫設計と運用管理
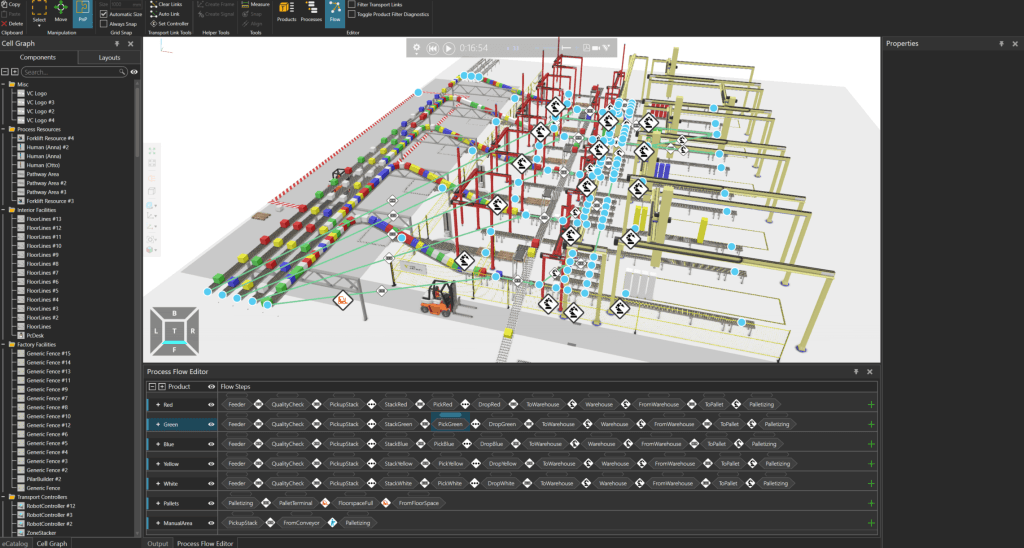
シミュレーションの効果を最大限に活かすには、目的に適したツールの選定が不可欠です。Visual Componentsは、直感的な仮想設計環境を提供します。これにより、倉庫レイアウトの設計から検証、最適化までを効率よく進められます。
倉庫計画の精度を高める3Dレイアウト設計
Visual Componentsの3Dレイアウトツールを使えば、倉庫のレイアウト作成や修正がスムーズに行えます。3,500点以上のシミュレーション対応コンポーネントを収録したeカタログから、必要な部品をドラッグ&ドロップで配置するだけで、すぐに仮想レイアウトが完成します。CADデータの取り込みにも対応しており、現実の構成に近いレイアウトを仮想空間に反映できます。複数のレイアウト案を比較しながら、事前にスペースの活用方法を検討することも可能です。
ワークフローを可視化するプロセスモデリング
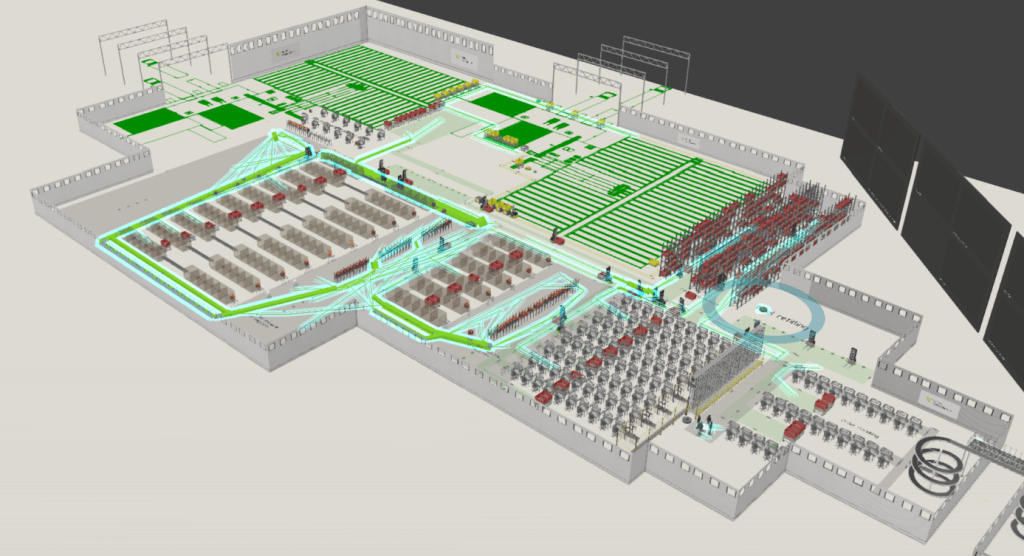
倉庫の効率は、ワークフローの構築次第で大きく変わります。Visual Componentsのプロセスモデリング機能を使えば、資材の流れを仮想環境でシミュレーションし、さまざまなピッキング方式や保管戦略を検証できます。運用に支障が出る前に、ボトルネックとなる箇所を見つけて対策を講じることが可能です。
自動化を成功に導くバーチャルコミッショニング
AGVやコンベヤー、ロボットといった自動化設備を十分にテストせずに導入してしまうと、かえって非効率化の原因になることがあります。Visual Componentsのバーチャルコミッショニング機能を使えば、シミュレーションと実際の制御システムを接続し、導入前に動作を細かく検証できます。
これらの機能を組み合わせることで、無駄なコストを抑えながら、安定性と効率性を兼ね備えた倉庫を構築できます。
仮想空間での設計を現場での実装へ
シミュレーションで設計を検証・改善した後は、それを現場に実装していくステップに入ります。どれほど計画を練っていても、拙速な導入によって現場に負荷がかかってしまうと、期待した成果は得られません。大きな変更ほど、現場の混乱を避けつつ、その効果を最大限に引き出せるよう、段階的に進めることが重要です。
すべてを一度に変えるのではなく、まずは効果が大きく、日常業務を止めずに進められる部分から取り組むのが現実的です。例えば、ピッキングエリアの見直しや保管レイアウトの調整、コンベヤーの配置最適化などは、即効性のある改善につながります。
また、レイアウト設計と同様に重要なのが、導入後のパフォーマンスを継続的に確認することです。注文処理の速度、混雑の発生箇所、資材の流れなどをモニタリングし、設計通りに機能しているかを見極める必要があります。改善が必要な場合も、まずシミュレーションで効果を確認してから現場に反映することで、確実で無理のない改善が可能になります。
これからの倉庫設計
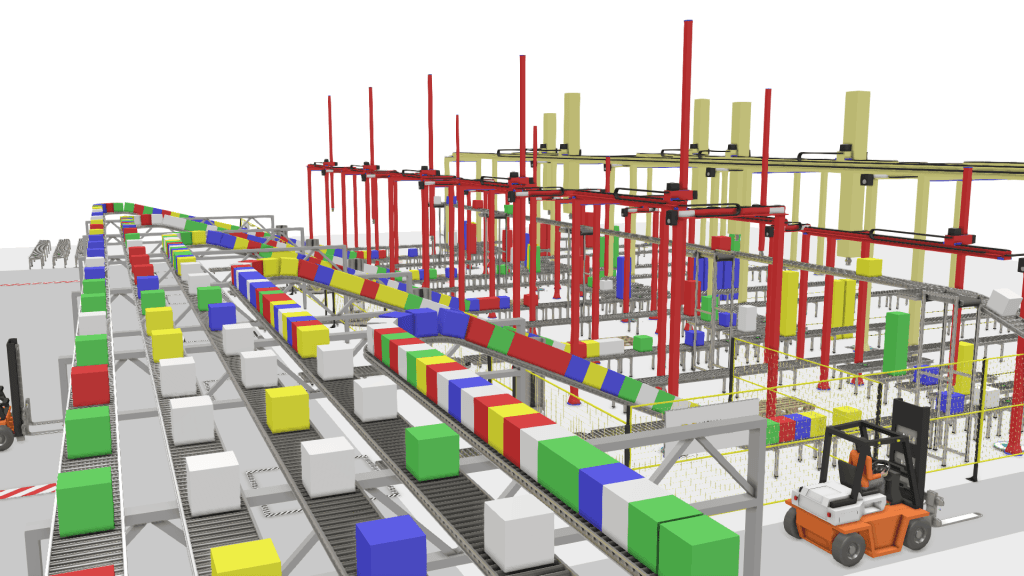
倉庫を取り巻く技術の進化に伴い、設計のあり方も大きく変わりつつあります。倉庫管理システム(WMS)と連携したデジタルツイン(実際の倉庫と連動する仮想モデル)を活用すれば、倉庫の状況をリアルタイムで把握しながら、レイアウトの調整や運用の最適化を継続的に行うことができます。さらに、AIを活用した自動化、省エネルギーやサステナビリティを重視した設計も、今後の倉庫設計に欠かせない要素となっています。
倉庫設計をよりスマートに
倉庫設計は、効率性・拡張性・コスト管理の基盤となる重要なプロセスです。計画が甘ければ、業務の混乱や生産性の低下、コストの増大といった問題を招きかねません。
シミュレーションを活用することで、倉庫設計は勘や経験に頼るものから、実際のデータに基づく合理的なプロセスへと進化します。具体的には、以下のような取り組みが可能になります。
- 限られたスペースを有効に活用し、資材の流れを最適化したレイアウト設計
- 導入前のシミュレーションによる計画の妥当性検証とリスク低減
- 業務変化に対応できる、継続的な改善体制の構築
Visual Componentsは、こうしたシミュレーションを、企業の競争力を高めるための戦略的な手段と位置づけています。既存倉庫の改善から新設プロジェクトまで対応可能で、効率性と柔軟性を兼ね備えた倉庫づくりを力強く支援します。
倉庫の課題をシミュレーションでどのように解決できるか、ぜひお問い合わせください。
Visual Componentsについて
Visual Componentsは、3D製造シミュレーション分野で25年以上の実績を持つ専門チームによって設立されました。現在では、2,400社を超えるグローバル企業に導入されており、40社以上のパートナー企業と連携。マシンビルダー、システムインテグレーター、製造業のお客様に向けて、製造プロセス設計やロボットオフラインティーチング(OLP)を、簡単・迅速・低コストで実現できるソリューションを提供しています。
Further reading
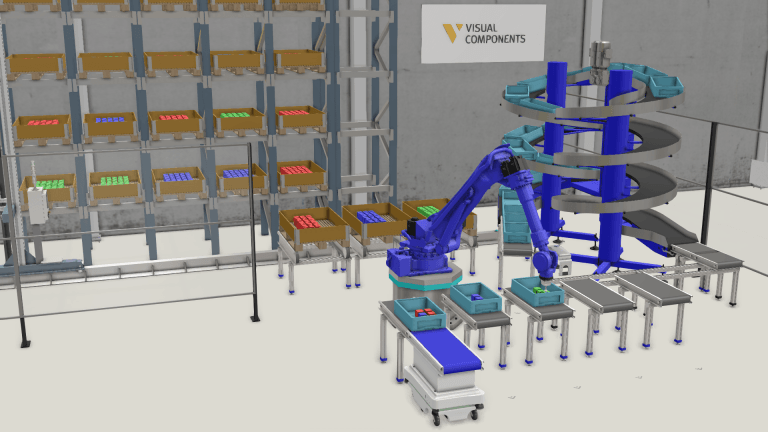
シミュレーションで実現する、生産ラインの最適化
スループットの向上、ボトルネックの解消、リソースの有効活用など、製造現場では常にプロセス改善が求められています。しかし、最適化は決して容易なことではありません。適切なツールがなければかえって複雑になり、思うように進みません。そこで有効なのが、シミュレーションです。仮想空間で変更案を事前に検証・調整し、関係者と共有することで、現場への影響を最小限に抑えながら、確実な計画立案が可能になります。
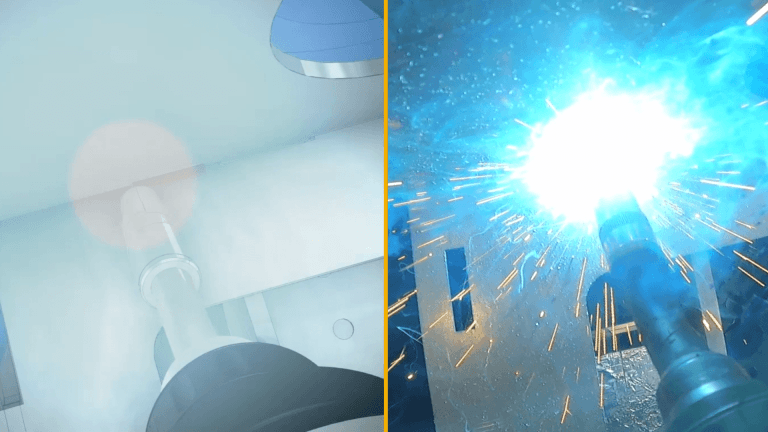
ロボットオフラインティーチング(OLP):完全ガイド(事例付き)
ロボットオフラインティーチング(OLP)を基礎から応用まで幅広く解説したガイドです。本ガイドでは、トピックの紹介に続いて、よくある誤解やOLPが解決する課題、その利点、そして実際の成功事例について詳しく説明します。