KONE社、3Dシミュレーションでエレベーターボタンパネルの組立計画を最適化
KONE社イタリア北部の拠点では、2種類の製品バリエーションに対応する新たな組立ラインを計画するにあたり、スムーズな作業の流れを実現しつつ、不良品リスクを最小限に抑える必要がありました。Visual Componentsでさまざまなレイアウト構成をシミュレーション・検証することで、統計的な分析で自信をもって意思決定を行い、実際に設備を導入する前の段階でもプロセス全体を明確に関係者に共有することができました。
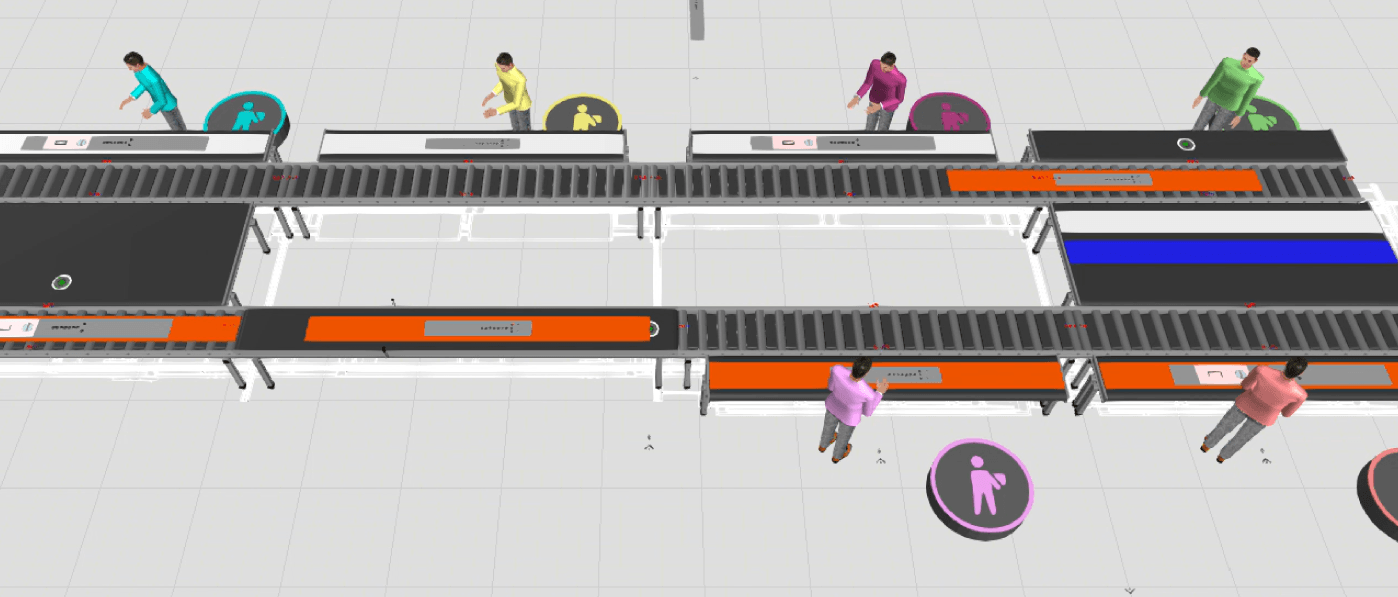
KONE社、3Dシミュレーションでエレベーターボタンパネルの組立計画を最適化
KONE社は、エレベーターや人の移動を最適化するソリューションで業界をリードする、グローバル企業です。同社はイタリア北部の拠点で、エレベーター用車両操作パネル(COP)の組立ラインを新設するにあたり、複数の技術的課題に直面しました。新しい組立ラインには、仕様の異なる2種類のCOPに対応しつつ、手作業を最小限に抑えた、スムーズで正確な組立プロセスが求められていました。このプロジェクトを主導したIndustrial EngineerのEdoardo Mostacchi氏は、従来の計画ツールではこうした要件に十分に対応できないとすぐに判断しました。そして、ラインの設計・検証・改善を実機構築前に行える3Dシミュレーションツール、Visual Componentsの導入を決めました。
COP組立ライン設計で直面した課題
エレベーター用COP(車両操作パネル)の組立ラインを設計するにあたって、KONE社は複数の課題に直面しました。中でも最も重要だったのは、部品の取り扱いと品質の確保です。乗客が操作するボタンや表示器を備えたCOPの前面パネルは、仕上がりに細心の注意が必要な部品で、組立中に傷やへこみが生じることは許されません。こうした損傷は、手直しや廃棄、さらには品質トラブルの原因となるため、組立途中の修正をできるだけ避けることが設計上の重要な条件となりました。
さらに大きな課題となったのが、1本のラインで仕様の異なる2種類のCOPを扱うことでした。一方は比較的シンプルな構造で、もう一方は追加機能を備えた複雑な仕様となっており、必要な作業時間や手順がそれぞれ異なります。どちらの製品も効率よく処理できるようにするには、ボトルネックや待機が発生しない、バランスの取れたライン設計が必要です。しかし、従来の静的なCADレイアウトや作業時間の見積もりでは、異なる製品が実際にどのようにラインを流れ、どこで混雑や遅延が生じるのかを把握するのは困難でした。
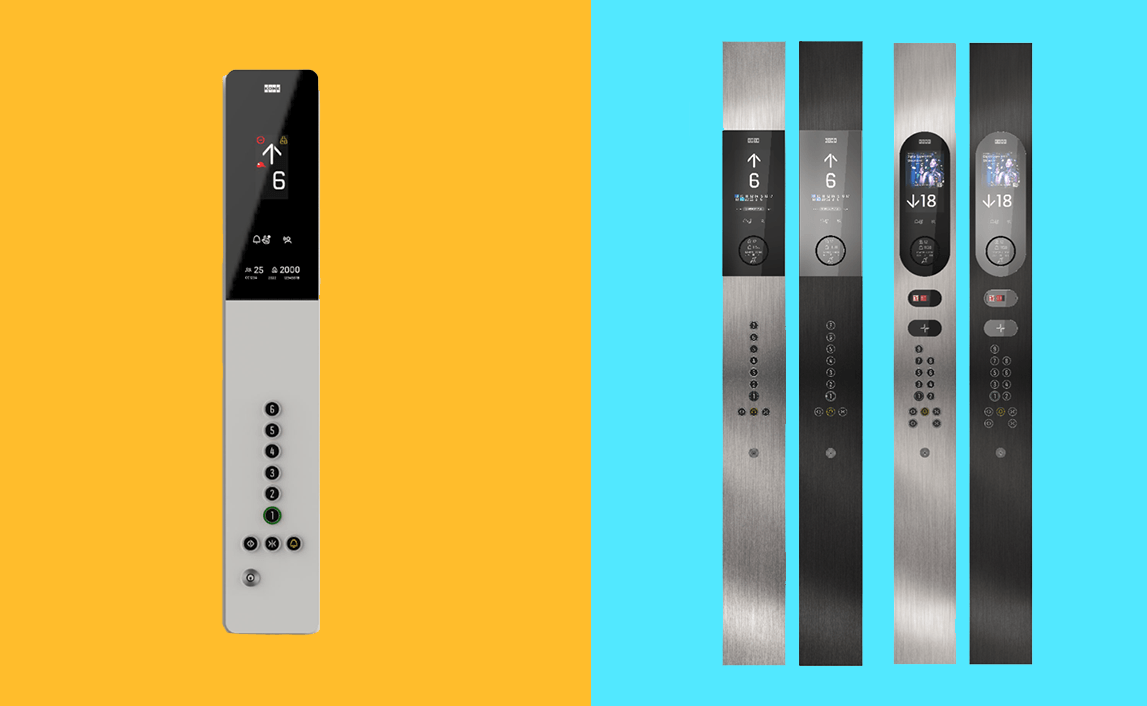
既存施設の面積やレイアウトにも制約がありました。限られた床面積の中で、新たなコンベヤーシステムと複数の作業ステーションを配置するには、レイアウトを慎重に設計する必要があります。オペレーターの安全かつ効率的に移動できる動線確保に加え、部品や完成品がワークフローを妨げることなくスムーズに搬入・搬出されるよう配慮しなければなりません。さらに、部品の供給から完成品の検査・梱包までを一貫してつなぐ、シームレスなライン構築も条件でした。こうした複雑な要件は、Excelのようなツールでは対応しきれないレベルに達していました。
プロセスの可視化と関係者間の認識共有も、大きな課題の一つでした。複雑な組立プロセスを、2D図面や抽象的なチャートだけで、現場の監督者、オペレーター、経営幹部といった多様な立場の関係者に正確に伝えるのは困難です。設計担当者たちには、プロセス全体の流れとそのメリットをわかりやすく示し、関係者全員の理解と合意を得る手段が必要でした。
こうした課題を解決するため、設計担当者たちは、Visual Componentsを導入し、シミュレーションを基盤とした設計アプローチを採用することにしました。
シミュレーション中心の設計手法
この組立ラインの基本方針は、「各COPの前面パネルを専用のパレットに取り付けた後は、工程全体を通じて人の手で直接触れることなく処理できるようにする」ことでした。パレットに固定された前面パネルは、そのままコンベヤーシステムに沿って各ステーションを順番に移動します。

Visual Componentsのeカタログに収録されている、Bosch Rexroth社のTS2モジュール式組立コンベヤーシステムを採用することで、各ステーション間におけるパレットのスムーズな移動を実現しました。
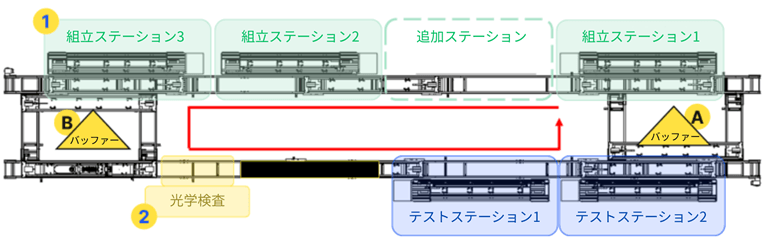
この事例では、COPを載せていない空のパレット専用のバッファーが3つ設けられています。プロセスの流れは、「A」とラベリングされたバッファーエリアから始まります。パレットはこの地点からラインに入り、3つの組立ステーションへと進みます。各ステーションは互いに独立して同時に稼働し、それぞれ1枚のパレットを呼び出して組立作業を完了させます。組立が完了したパレットは、COPを載せたままラインに戻り、次の工程に進みます。その後、「B」と表示された位置にある第2のバッファーへ移動し、パレットは最大3枚までそこに収容されます。各ステーションはパレットの処理を完了すると、バッファーAから次のパレットを呼び出します。これらのバッファーは、工程間のばらつきや軽微な遅延を吸収し、ライン全体の安定稼働を支える役割を果たします。保持するパレットの数はシミュレーション上で調整可能で、スループットや作業の連続性に与える影響を検証できるようになっています。
バッファーBの下流には、AI(人工知能)とOCR(光学文字認識)を活用した高精度の光学検査システムが配置されています。このシステムは、目視可能な部品が正しく組み立てられているかを自動で確認します。万一不良が検出された場合、該当するパレットはテストステーションを経由せず、自動的にバッファーAへ戻されます。この仕組みにより、不良品を載せたパレットは、必要なツールや部品がそろった組立ステーションへと確実に戻り、再組立が行われるようになっています。
COPが検査に合格すると、パレットはその場で一時停止し、テストステーションからの呼び出しを待ちます。組立ステーションと同様に、テストステーションもパレットを順番に呼び出し、作業が終わると次の工程へ送り出します。パレットがテストステーションに到着すると、COPが正しく機能しているかどうかを確認するテストが実施されます。テスト完了後、COPは手動でパレットから取り外され、自動化ラインの外にある梱包ステーションへと運ばれます。オペレーターは空になったパレットをラインに戻し、パレットは再びバッファーAへ移動して、次の組立サイクルに備えます。このようにして、組立から検査、梱包に至る一連の工程が、途切れることなく循環しています。
「シミュレーションがなければ、最初の設計は手探りで行うことになっていたでしょう。作業者が行う各工程について、これまでの手順書や時間実績をもとに処理時間や負荷を一応試算してはいましたが、それだけでは必要なパレット数や工程全体の流れを正確に把握することはできませんでした。シミュレーションによって、計算やExcelだけでは見えてこないプロセス全体の動きが、はじめて可視化されたのです。」
KONE社、Industrial Engineer、Edoardo Mostacchi氏
検査およびテスト工程も含めてライン全体をシミュレーションすることで、組立プロセス単体ではなく、工程全体の品質管理を最適化できました。実際、バッファーや工程のバランスが崩れるとスループットに悪影響が出るため、品質を安定して維持するには、早い段階での可視化と調整が欠かせません。Visual Components上では、パレット搬送、バッファー、交差コンベヤー、複数のステーション、品質検査といったすべての要素がモデル化され、仮想環境での検証が可能です。こうして構築されたシミュレーションモデルには、予定しているレイアウトやプロセスロジックが反映されており、Edoardo氏をはじめとする設計チームは、これによってライン全体の流れを事前に確認できるようになりました。例えば、ステーションでのパレット滞留や、オペレーターの手待ちといった潜在的な問題もアニメーションで即座に視認でき、改善が必要な箇所が一目で分かります。このように、高精度な可視化によって、設備の設置前にプロセス全体を検証することができるようになりました。これは、静的なCAD図面やExcelの試算だけでは実現できないことです。
シミュレーション手法とMTM分析
KONE社は、シミュレーションの技術的信頼性を高めるために、Visual Componentsの3Dモデリングと統計分析機能に、産業工学に基づく時間分析を組み合わせた厳密な手法を採用しました。中でも核となったのが、すべての手作業にMTM(作業時間測定法)のデータを適用するアプローチです。MTMは、あらかじめ設定された標準時間を各作業ステップに割り当てる分析手法です。KONE社では元々、COPの組立作業にかかる標準時間や、それに準じた時間研究データを計測していました。ネジの締め付けやワイヤーの接続、部品のテストといった作業にかかる時間を、データとして各ステーションの作業内容に反映することで、推定ではなく実測に基づいた正確なサイクルタイムを導き出すことができ、より信頼性の高いシミュレーションを実現しました。
「シミュレーションを使って、さまざまなシナリオを検証しました。ステーションの数を3台と4台で変えたり、パレットの数や製品の量を調整したりして、スループットやリソース稼働率を比較しました。こうして得られたデータが、意思決定の確かな根拠になりました。」
KONE社、Industrial Engineer、Edoardo Mostacchi氏
シミュレーションは、実際の生産(8時間のフルシフトや、ラインが安定稼働に至るまでの十分なサイクル数)を想定して行われました。実行中は仮想センサーとカウンターが稼働し、テストに合格したCOPユニット数、各パレットの工程ごとの滞在時間、オペレーターの稼働率といったデータが記録されます。これらのデータはすべて、Visual Componentsから抽出・分析が可能です。KONE社は複数のシナリオを仮想環境で再現し、それぞれの構成に対して検証を実施しました。そうすることで、パラメーターやレイアウトを調整しながら、各要素の変更が全体のパフォーマンスにどう影響するかを確認できました。
最適な設計を見極めるために、シミュレーションで検証した構成要素
- 組立ステーションの数:KONE社は、組立ステーションを3台にする場合と4台にする場合のシナリオを比較しました。シミュレーションを通じて、生産目標を達成するためにステーションを増設すべきか、それとも3台構成のまま軽微な調整をすることで対応できるかを検証できました。
- パレットの流通量:システム内を循環するパレットの数も重要な検討要素でした。シミュレーションにより、ボトルネックを回避しながら安定したフローを保てる、最適なパレット数を見極めることができました。
- バッファーの容量と配置:バッファーのサイズや設置場所も、ワークフロー全体の効率を左右する要因です。不要な中断を避けるために、シミュレーションでさまざまなバッファー構成を試行・検証しました。
- 手直し率:過去の実績データに基づき、不良率を5%としてモデル化しました。
- 製品構成比率:シンプルなCOP30%、複雑なCOP70%などの、複数のパターンで検証を行いました。
最適なライン構成の見極め
「シミュレーションを通じて、ループ内のパレット数は10台が最適であると分かりました。それ以上になるとシステムが渋滞し、逆に少なすぎると一部のステーションが待機状態になってしまいます。最適なバランスを見つけるには、仮想環境での検証が不可欠です。」
KONE社、Industrial Engineer、Edoardo Mostacchi氏
徹底したシミュレーションと分析を経て、エンジニアリングチームはすべてのプロジェクト目標を達成できる構成を導き出しました。最終的な組立ラインは、COP用の手動組立ステーションを3台配置し、品質チェック機能を組み込んだパレット搬送型のコンベヤーシステムを採用する設計となりました。シミュレーションにより、3台のステーションでも、適切なパレット数とバッファーサイズを維持すれば、2種類のCOPバリエーションを効率よく処理できることが確認できたからです。また、パレットの最適数は10台であることが分かりました。この数であれば各ステーションはほぼ常時稼働し、オペレーターの生産性を保ちながらも、ライン上での滞留を防げます。10台未満では、部品の到着待ちによって一部のステーションがアイドル状態になり、スループットが低下しました。逆に10台を超えるとパレットがバッファーで滞留し始め、完成品の数が増えないままプロセスが混雑する傾向が見られました。つまり、パレット10台という構成が、連続した生産フローを維持するのに最もバランスが取れていることが分かったのです。こうして設計から検証までをデジタル上で行えたことで、KONE社は十分な根拠を持って実装へと進むことができました。
プロジェクトの成果と今後の展望
KONE社がイタリアで構築した新しいCOP組立ラインは、Visual Componentsのシミュレーションソフトウェアを活用することで、無事に完成しました。製品品質の確保、生産目標の達成、ステークホルダーとの円滑なコミュニケーションといったプロジェクトの目標を、すべて達成できました。
この取り組みを通じて明らかになったのは、仮想環境を活用した組立計画により、従来の方法では実現できないプロセス全体の最適化が可能になるということです。得られた効果は、生産量の向上や品質改善といった目に見える成果に加え、チーム内の認識の統一や意思決定に対する自信といった、目に見えないメリットにも及びました。
Visual Componentsについて
Visual Componentsはシミュレーションの専門家チームによって設立され、25年以上の実績を持つ3D製造シミュレーション業界の先駆者の一つです。主要なブランドの信頼できる技術パートナーであり、機械メーカー、システムインテグレーター、製造業者に、シンプルで迅速、かつコスト効率の高いソリューションを提供しています。Visual Components社のソリューションを使用して、製造プロセスの設計とシミュレーション、ロボットオフラインティーチング(OLP)を行うことで、産業用ロボットの迅速で正確かつエラーのないティーチングを行うことができます。
当社のソリューションを活用するメリットについて詳しく知りたい方は、ぜひお気軽にお問い合わせください。
Further reading
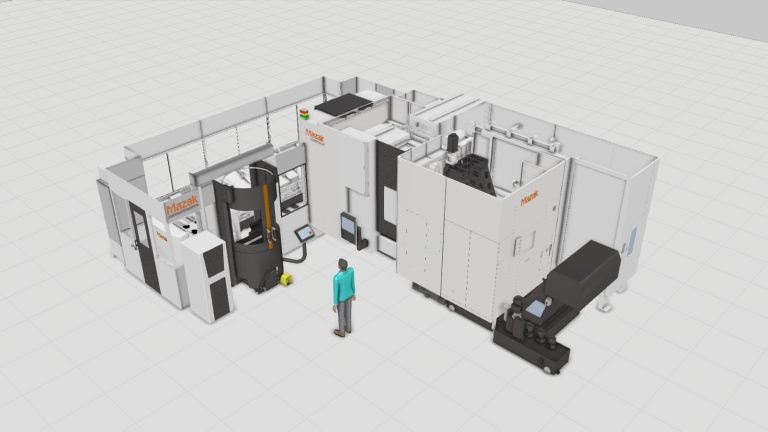
CNC加工の可視化:Mazak UK社、Visual Componentsで提案スピードと顧客理解を加速
CNC工作機械の世界的リーダーであるMazak UK社は、特にPALLETECHシステムの複雑さを従来の2D図面で伝えることに課題を抱えていました。この問題は顧客との円滑なコミュニケーションを妨げ、提案までの時間を長引かせる原因となっていました。しかし、Visual Componentsの導入により状況は一変。プロジェクト計画と実行時間を大幅に短縮し、効率性を飛躍的に向上させただけでなく、顧客とのエンゲージメントも強化され、新たな成果を生み出しています。
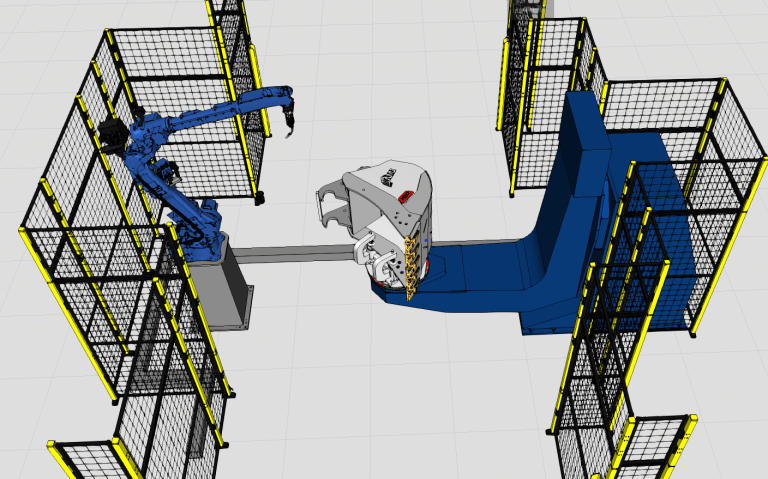
溶接工不足への対応:AMI Attachments社がVisual Components OLPを活用して生産効率を向上させた方法
北米を代表する重機アタッチメント製造業者のAMI Attachments社は、生産効率を向上させ、市場の変化する需要に応えると同時に、溶接技術者の不足という課題に直面していました。Visual ComponentsのOLPソフトウェアを導入することで、ティーチング時間を70%削減し、生産効率と品質の向上を実現しました。
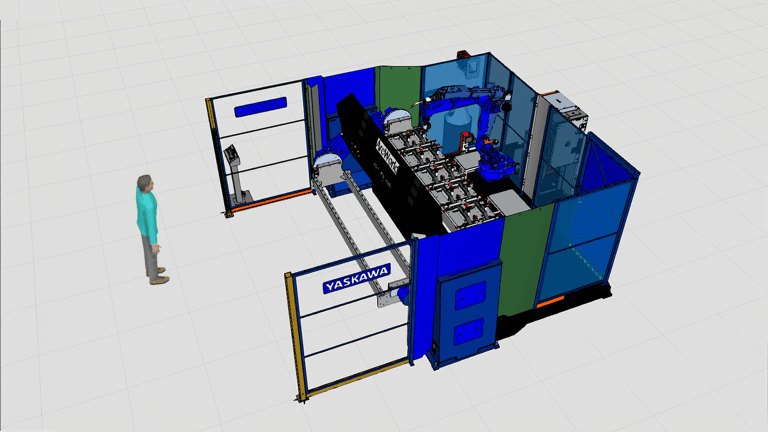
溶接におけるイノベーションと伝統:Berlin Gardens社がVisual Components Robotics OLPを活用して前進した方法
高品質の屋外用家具で有名なBerlin Gardens社は、家具の需要が伸び続ける中で、製造プロセス、特に溶接の自動化において課題に直面していました。Visual Components Robotics OLPの導入により、アルミニウム製の固定具を家具の底部に溶接するような複雑なタスクに対して、ロボットを効率的にティーチングすることができ、安定したスピードと品質での生産を実現しました。