シミュレーションで実現する、生産ラインの最適化
スループットの向上、ボトルネックの解消、リソースの有効活用など、製造現場では常にプロセス改善が求められています。しかし、最適化は決して容易なことではありません。適切なツールがなければかえって複雑になり、思うように進みません。そこで有効なのが、シミュレーションです。仮想空間で変更案を事前に検証・調整し、関係者と共有することで、現場への影響を最小限に抑えながら、確実な計画立案が可能になります。
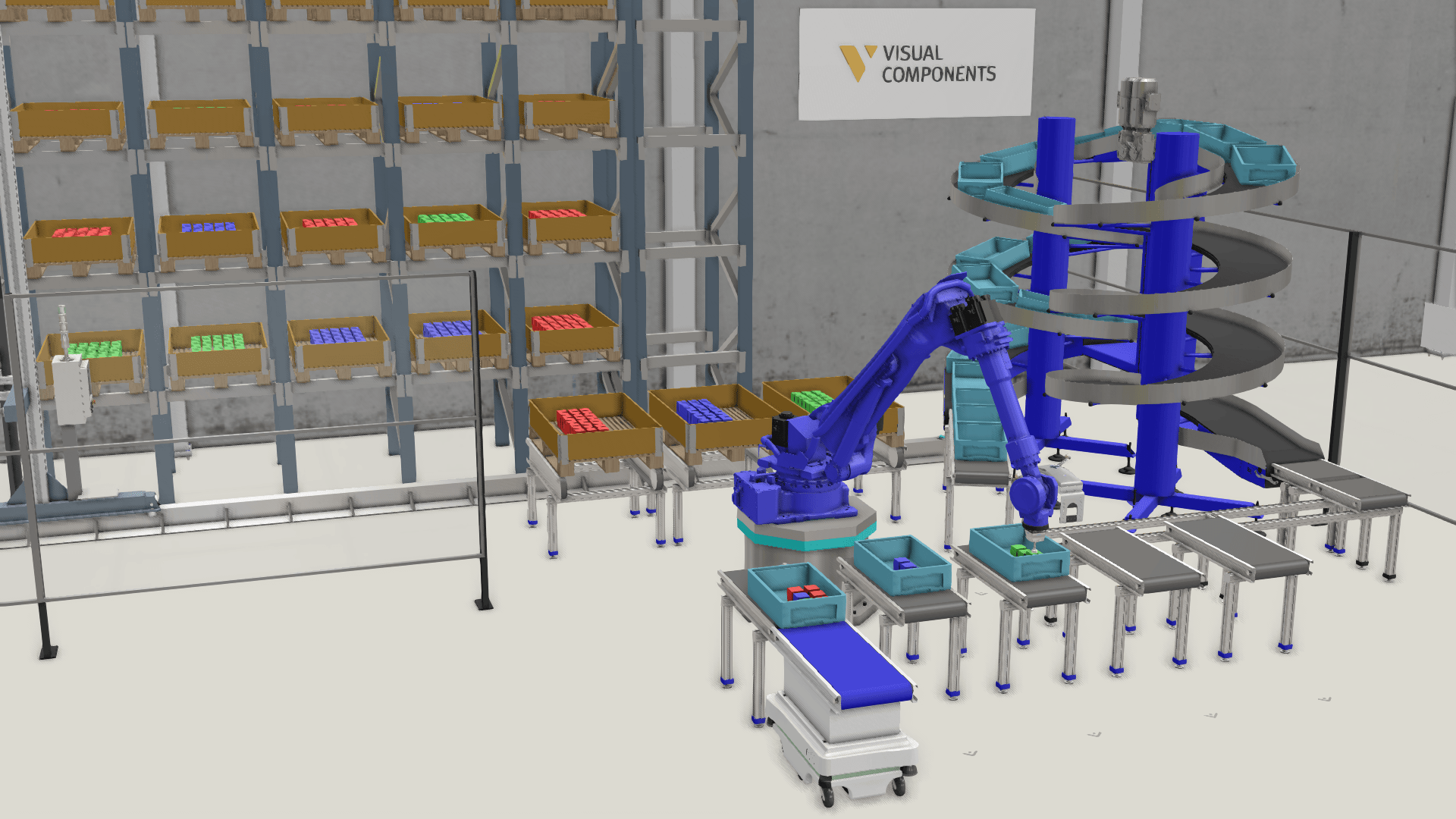
シミュレーションで実現する、生産ラインの最適化
どの現場でも「生産性を高めたい」「無駄を減らしたい」という思いは共通しています。とはいえ、実際に最適化を進めるとなると、思わぬ障壁に直面することも少なくありません。改善のつもりで行った変更が、新たなボトルネックやダウンタイムを引き起こしたり、既存のやり方に慣れた従業員の反発を招いたりすることもあります。
リーン生産方式やシックスシグマといった従来の手法は、現場の効率化に大きく貢献してきましたが、実際の現場で試しながら進める必要があるため、一定のリスクは避けられません。考えるべきなのは、生産を止めずに、失敗のコストを抑えながら、どうプロセスを磨いていくかということです。
この点で、シミュレーションは大きな力を発揮します。仮想環境でレイアウトやワークフロー、自動化の効果を事前に把握できるため、現場に導入する際も自信を持って進められます。
既存プロセスが最適化しづらい背景
現在でも、多くの現場では、紙ベースの図面や2Dレイアウト、手作業による分析といった旧来型のアプローチに依存しています。こうした方法では変化に対応しづらく、効率化の障壁となることがあります。
例えば、新たなコンベヤーを導入して搬送効率を高めようとしても、レイアウトが不適切であれば、生産ラインを一時停止し、機器配置や配線を大幅に見直す必要が生じ、結果として多大なコスト負担を招く可能性もあります。
技術面だけにとどまらない、組織的な課題
- ROIの不確実性:投資効果が明確でなければ、経営層の承認は得にくい
- 視点のズレ:エンジニア、現場担当者、マネジメントがそれぞれ異なる観点から「最適化」を解釈しているため、優先順位が一致しない
- 変化への抵抗感:従業員には、長年慣れ親しんだやり方を変えることに抵抗感があり、すぐに効果が見えないと受け入れが難しくなる
McKinsey & Company社の調査によると、データを活用したプロセス最適化を実現し、自動化の取り組みを広く展開した企業では、労働生産性が最大で30%向上しています。一方多くの企業は、社内外の関係者から協力を得られず、テストプロジェクト段階で足踏みしている状況です。
従来ツールの限界
これまでの製造現場では、以下の手法が一般的でした。
- CAD図面や2Dスキーマ:レイアウトの全体像を把握するには有効だが、動きのある挙動の可視化には対応していない
- PowerPointや報告書:変更点の説明には活用できるが、プロセスの流れを伝えるには不十分
- 手作業での動線・動作時間調査:非効率な箇所の発見には役立つが、労力がかかり、全体を網羅するのは難しい
こうした方法では、課題の把握はできても、安全にテストしたり、関係者と視覚的に共有したりするには限界があります。そのため、多くの企業が3D製造シミュレーションを導入し、仮想空間であらかじめ検証を行いながら、関係者の合意をスムーズに得られる環境を整えようとしています。
3Dシミュレーションで、リスク低減とスピードを両立
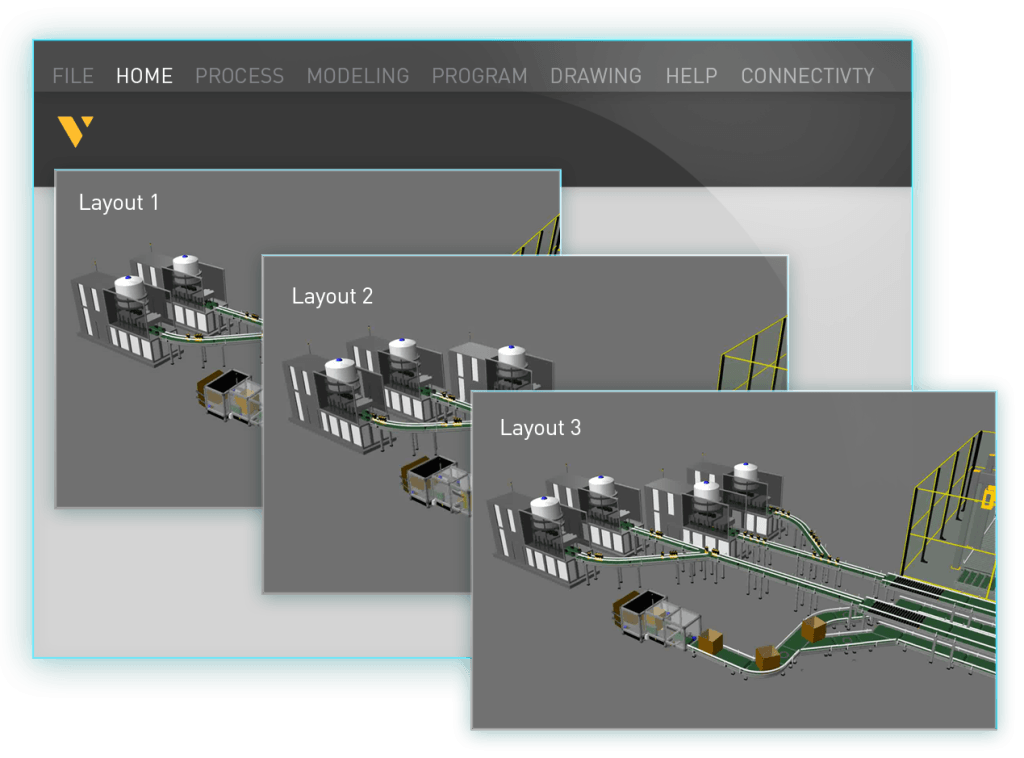
プロセス変更を不確実なまま進めるのではなく、3D製造プロセスシミュレーションを活用することで、管理された仮想環境のなかで複数のシナリオを比較・検証できます。これにより、変更内容に対してすべての関係者が理解・納得したうえで、計画を着実に進められます。さらに、Visual Componentsのようなツールによるバーチャルコミッショニングを使用すれば、PLCロジックやロボットの制御プログラムを含む自動化システムを、現場導入前にテスト・検証できます。新しい生産レイアウトの評価や自動化の統合、ワークフローの調整なども、実環境に影響を及ぼす前に結果を予測し、的確に対応策を講じることが可能です。
3D製造シミュレーションの主な効果
- 部門間連携の強化:エンジニア、現場スタッフ、マネジメントが共に変更点を把握し、意思統一を図れる
- 生産リスクの低減:仮想環境での事前テストにより、現場への影響を最小限に抑えられる
- 根拠ある意思決定:実際のデータをもとに計画を検証し、勘や感覚に頼らない判断ができる
- 改善スピードの加速:実機を使わずに複数案を比較し、検討サイクルを短縮できる
大きな失敗を恐れて改善に踏み出せない企業にとって、シミュレーションは、コストのかかるミスを避けつつ、確信を持って意思決定を行うための有効な手段となります。
シミュレーションで構想を現実に
シミュレーションの本質的な価値は、構想と現実のギャップを埋めることにあります。理論や経験だけでなく、現実に近いデジタルモデルを構築することで、導入前から確信を持った判断が可能になります。
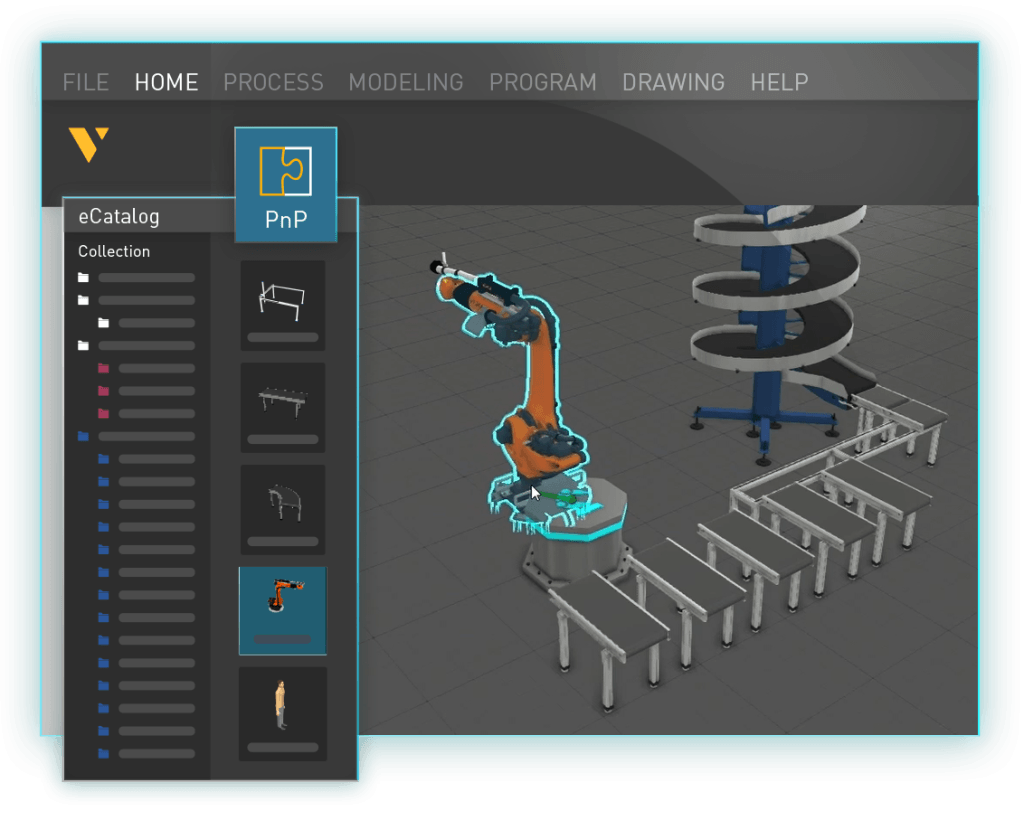
Visual Componentsのeカタログのような既製ライブラリには、産業用ロボットや機械、自動化機器の3Dコンポーネントが豊富に揃っています。これらを活用して生産シナリオを数分以内に構築し、さまざまなレイアウトを検証できます。これにより、設備同士の連携を確認し、ボトルネックを特定したうえで、実環境への導入前にプロセスを最適化できます。
プロセスモデリングでできること
- ワークフローや資材の流れのマッピング
- 自動化ルールや制約条件のモデル化
- 設備間の動作や連携のシミュレーション
工場レイアウトツールを併用すれば、2D図面や点群データ、CADモデルを取り込んで、生産空間の高精度なデジタルツインを構築できます。これにより、空間設計やリソース配置の精度が高まり、既存設備とのスムーズな統合が可能になります。
データを活用した意思決定の実践
シミュレーションは単なる可視化手段ではなく、改善効果を数値で裏付ける検証ツールです。主要な指標を記録・分析することで、プロセス改善に向けて、データを活用した的確な意思決定が行えます。
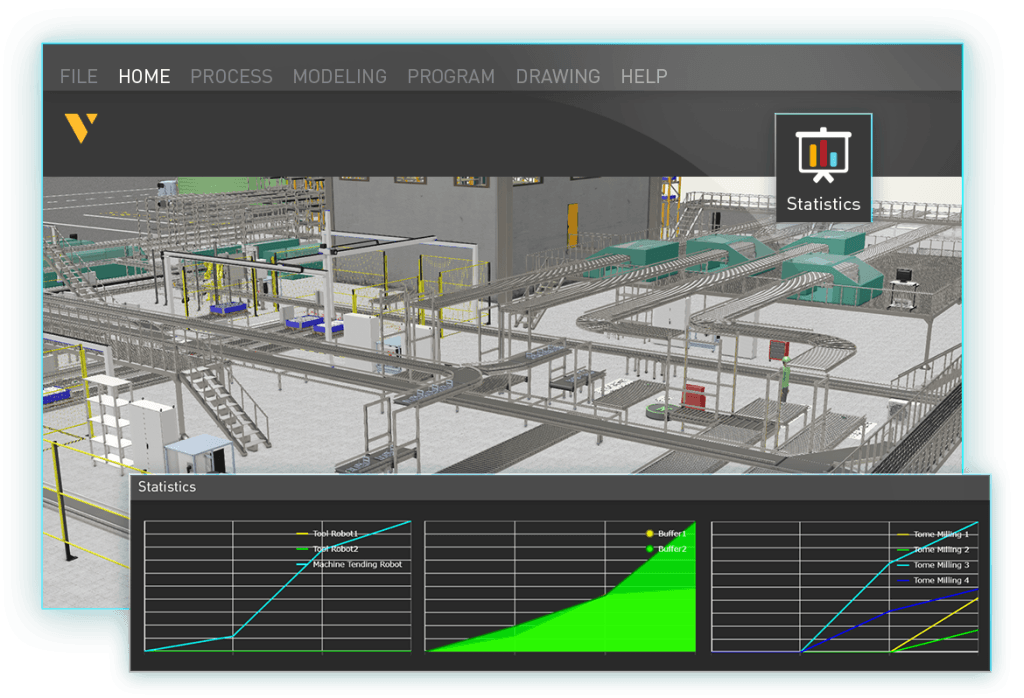
シミュレーションを活用すれば、生産現場の状況を次のような視点で的確に把握できます。
- サイクルタイム:各工程にかかる時間は?
- ボトルネック:どこで滞留が発生し、どう解消できるか?
- リソース活用:設備や人材は有効に使われているか?
複数のシナリオを比較することで、現場での試行錯誤に頼らず、最適な構成を見つけ出せます。
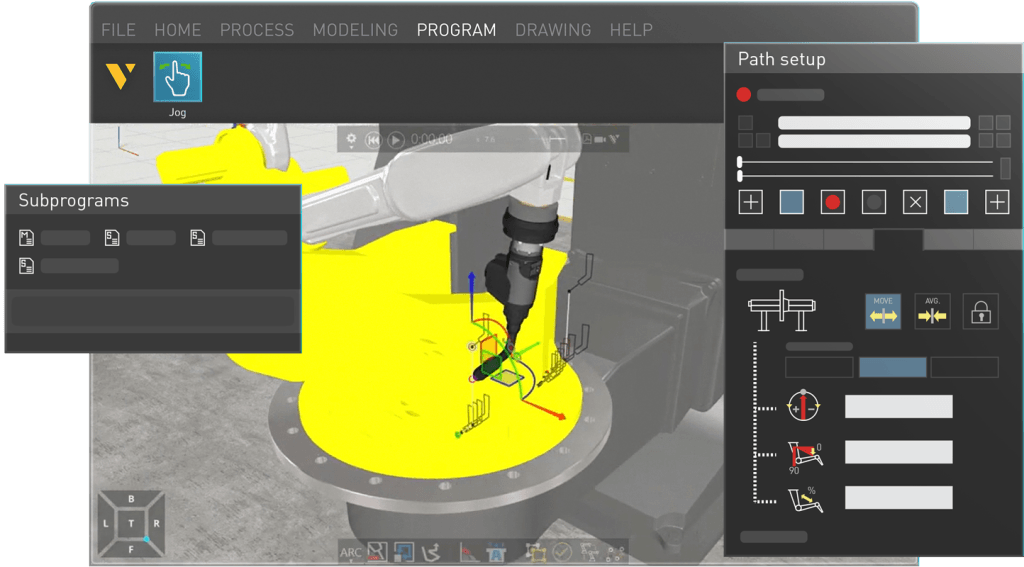
自動化やロボット導入を検討する企業にとって、ロボットオフラインティーチング(OLP)は、現場導入前に動作を完成させるための実践的なアプローチです。従来のように現場でロボットに直接ティーチングするのではなく、仮想空間上で動作を設定・検証できるため、ダウンタイムを最小限に抑えながら、スムーズかつ確実に導入を進められます。
プロセス改善を加速するシミュレーションの力
Henry Ford氏の流れ作業に始まり、今日のスマートファクトリーに至るまで、製造現場は常に効率化を追求して進化してきました。従来の最適化手法も一定の成果を上げてきたものの、変化のスピードと複雑性が増すなかで、予測力や柔軟性の面では限界が見えてきています。
シミュレーションを活用すれば、すべての変更を事前に仮想環境で検証し、実際のデータに基づいて部門間で足並みを揃えて進められるため、手探りの最適化から脱却できます。その結果、メーカーは以下のことに取り組めるようになります。
- 生産を止めることなく、改善策を計画・検証
- 自動化戦略を導入前に見直し・最適化
- 実際のデータをもとにした、確信を持ったプロセス改善
このようなシミュレーション主導のアプローチは、競争力を維持・強化するために不可欠な選択肢です。今や「導入するかどうか」ではなく、「いかに早く実践に移すか」が問われています。
まずは、シミュレーションのメリットを体感してみませんか?
シミュレーションが貴社の業務にどのように役立つか、実際の導入事例やROIの試算も交えてご説明いたします。ぜひお気軽にお問い合わせください。
Further reading
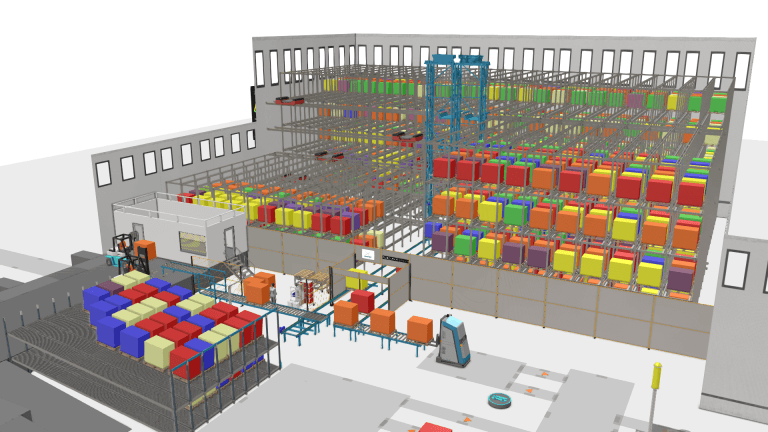
シミュレーションから始める、よりスマートな倉庫計画
人件費やその他のコストを抑えつつ、初日から効率よく稼働する倉庫を設計するにはどうすればよいでしょうか?鍵になるのは、Visual Componentsのようなシミュレーションツールを使った、事前の十分な検討と検証です。
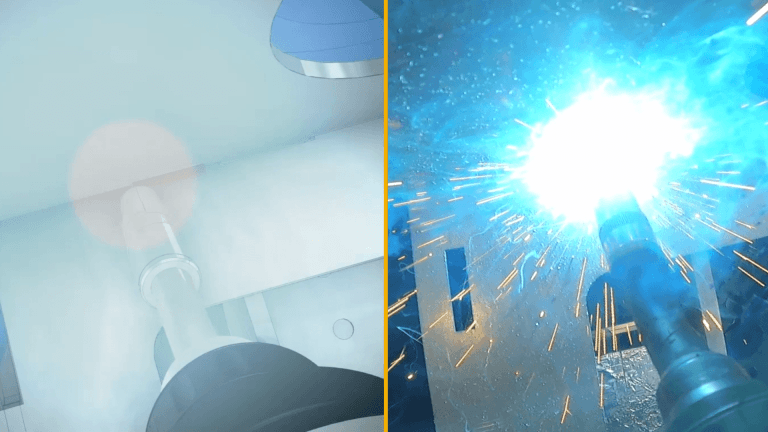
ロボットオフラインティーチング(OLP):完全ガイド(事例付き)
ロボットオフラインティーチング(OLP)を基礎から応用まで幅広く解説したガイドです。本ガイドでは、トピックの紹介に続いて、よくある誤解やOLPが解決する課題、その利点、そして実際の成功事例について詳しく説明します。